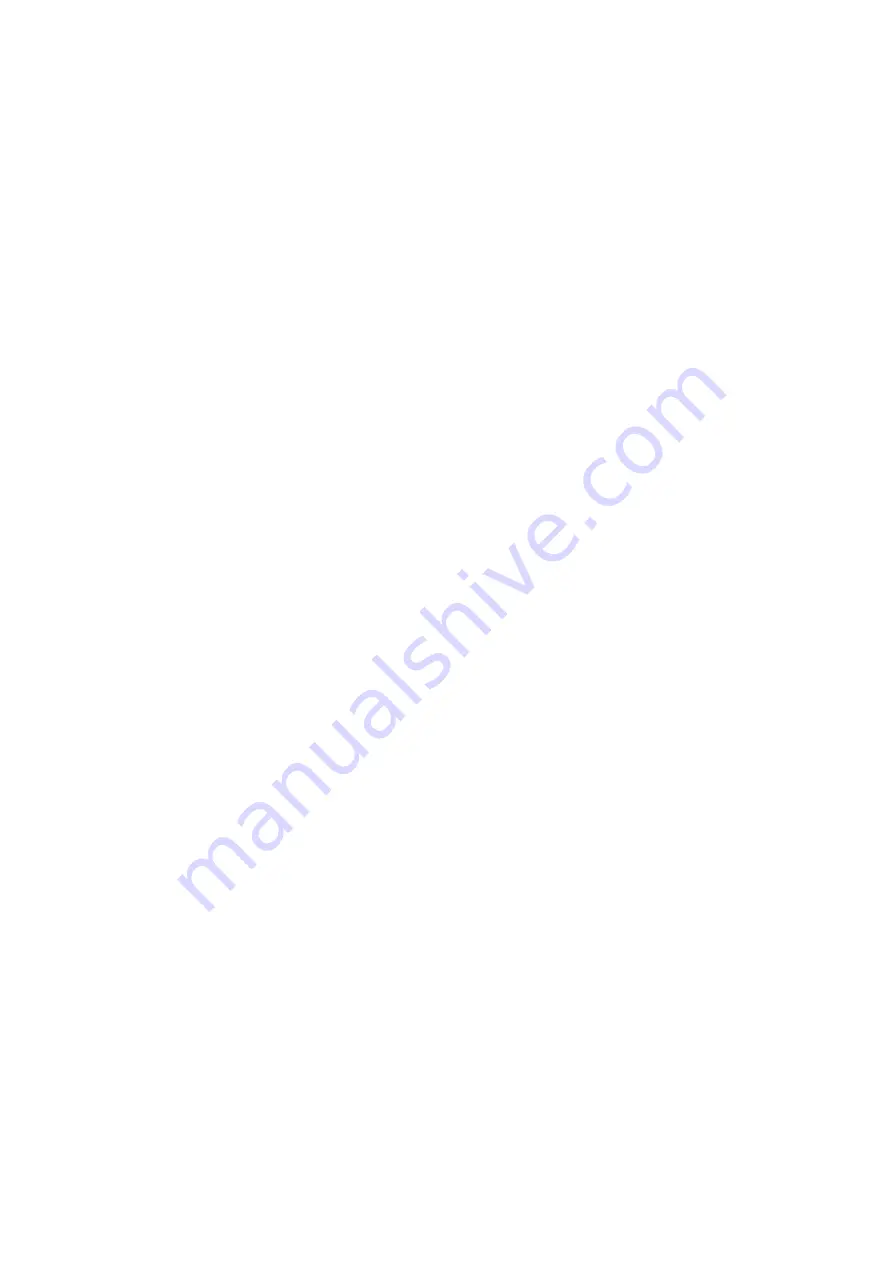
9 OF 20
ADJUSTING THE MITER ANGLE
z
A miter cut is one that is at an angle across the horizontal surface of the material. You will
commonly make 45º miter cuts to join two pieces in a right angle corner. A 30º cut is often used for
a scarf joint or to make a chamfered end.
z
To make a miter cut, loosen the Miter Lock Knob by turning it approximately 1/4 turn
counterclockwise. Press down the Thumb Lever to unlock the Table. While holding the Thumb
Lever down, move the Table to the desired angle. The Miter Angle Indicator will indicate the
selected angle. The table will lock into place at often used miter angles, including 22.5º, 30º, 45º,
and 90º on both left and right sides.
z
With the Table adjusted to the desired angle, place the work piece flush against the Fence, secure
it with the Hold Down Clamp and make the cut.
ADJUSTING THE BEVEL ANGLE
z
A bevel cut is one that is at an angle to the vertical plane of the material.
z
Bevel cuts can be used to miter relatively wide and thin material. Bevel cuts can be used in
combination with a miter cut to form a compound angle. Compound angle cuts are often used in
crown moldings, picture frames and similar trim materials.
z
To set the bevel angle, loosen the Bevel Lock Handle at the rear of the saw. To do this, press in the
Lock Button and rotate the Handle 1/2 turn counterclockwise. Move the blade assembly left to the
desired angle. You can read the angle on the Bevel Angle Indicator. Lock the blade assembly into
position by pressing in the Lock Button and rotating the Bevel Lock Handle clockwise. Tighten
firmly but not over-tight.
z
Make a sample cut in a piece of scrap and check to be sure the bevel angle is correct. If it is not,
correct the angle before cutting your work material.
USING THE DEPTH STOP
z
If you want to make a kerfing or rabbet cut which does not cut through the work piece, you can use
the Depth Stop Screw to control the depth of the cut.
z
To limit blade assembly travel, turn the Depth Stop Screw clockwise. The further you screw down
the Depth Stop Screw, the shallower the cut will be.
z
After the desired cut has been made, return the Depth Stop Screw to its open position by turning it
counterclockwise.
GENERAL OPERATING INSTRUCTIONS
z
When the Handle is lowered, the Blade Guard raises automatically. When the Handle is raised the
Blade Guard returns to its safety position. Keep hands clear of the Blade when the Handle is
lowered. Never interfere with the proper movement of the Blade Guard.
z
There are locking mechanisms for the miter angle and the Slides. Unlock the Table to set the miter
angle, then re-lock it before making the cut. Unlock the Slide using the Slide Lock Wing Screw
before making a cut if the work material is too wide to “chop.”
z
To rotate the Table, press down the Miter Thumb Lever, rotate the Table to the desired angle, then
release the Miter Lock Lever. Notches are machined into the Base of the tool, which will lock the
Table into several often used miter angles. These angles are 0º (centered), 15º, 22.5º, 30º and 45º
both left and right cut.
z
On wider pieces, you will have to slide the blade while making the cut. To unlock the Slide, loosen
Summary of Contents for 46463
Page 16: ...16 OF 20 DIAGRAM ...