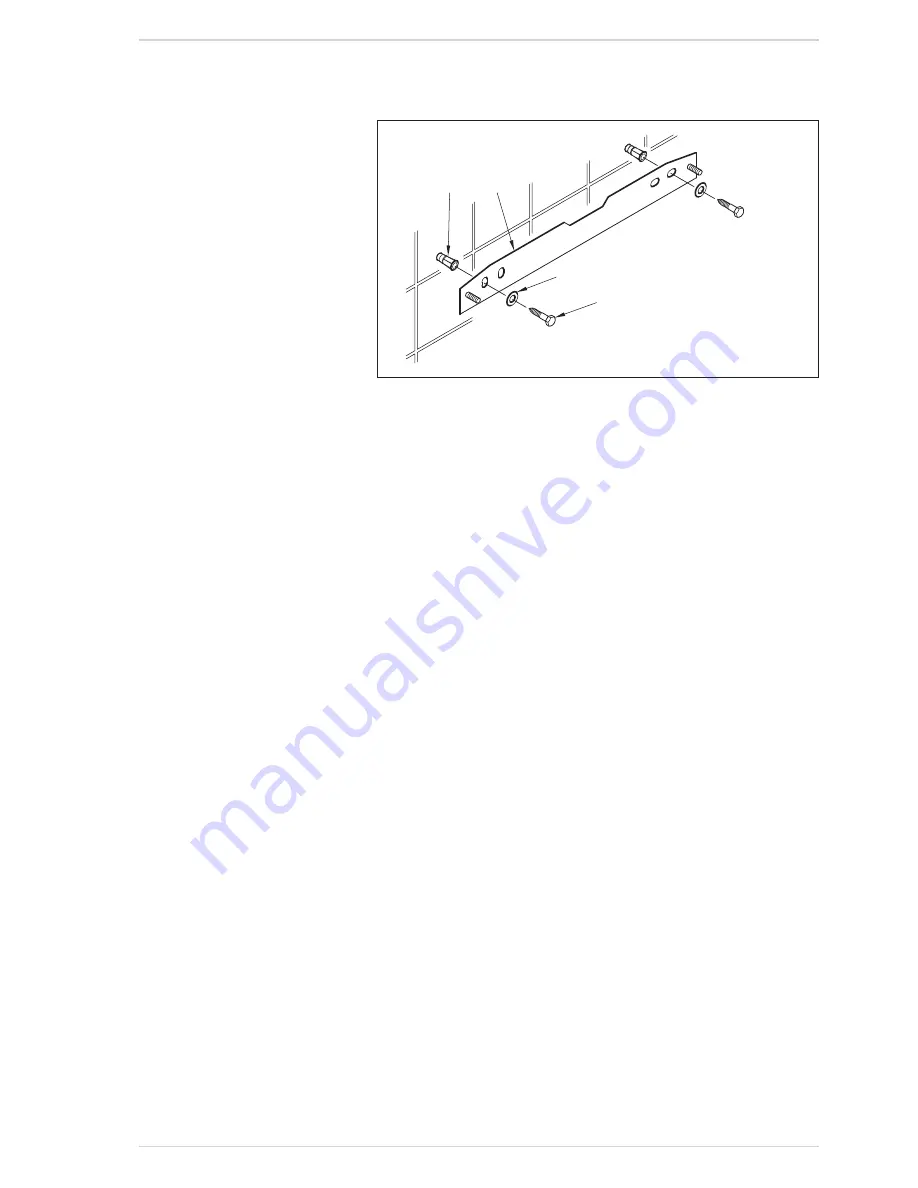
It is important that the boiler is initially
filled and started for the first time using
the method shown in 2.3.3 section e).
This procedure should also be used
when refilling after draining a boiler.
The boiler must be installed in a fixed
location and only by specialized and
qualified person in compliance with all
instructions contained in this manual.
The installation of this boiler must
be in accordance with the relevant
requirements of the current Gas Safety
(installation and use), the local building
regulations, and and I.E.E. wiring
regulations.
Detailled recommendations
for air supply are given in BS5440:2.
The following notes are for general
guidance: it is not necessary to have a
purpose provided air vent in the room
or compartment in which the appliance
is installed.
2.1 ANTI-FREEZE
FUNCTION
The boilers are equipped with anti-freeze
function which activates the pump and
the burner when the temperature of the
water contained inside the appliance
drops to below value PAR 10. The anti-
freeze function can only operate if:
– the boiler is correctly connected to
the gas and electricity supply circuits;
– the boiler is switched on;
– the boiler ignition is not locked out;
– the essential components of the boiler
are all in working order.
In these conditions the boiler is protected
against frost down to an environmental
temperature of -5°C.
ATTENTION: In the case of installation
in a place where the temperature drops
below 0°C, the connection pipes must
be protected.
2.2
FIXING THE WALL
MOUNTING BRACKET (fig. 4)
– Mark the position of the two wall
mounting bracket fixing holes and the
flue/air duct hole on the appropriate
wall(s).
– Drill the two fixing holes using a 10
mm masonry drill and fit the plastic
plugs provided.
– Accurately measure the wall thickness,
and note this dimension for later use.
– Secure the wall mounting bracket in
position using the screws provided.
Ensure that it is the correct way up,
as indicated in fig. 4.
2.3
CONNECTING UP SYSTEM
Before connecting the boiler it is
recommended that the system be
flushed in accordance to BS 7593, to
eliminate any foreign bodies that may be
detrimental to the operating efficiency
of the appliance. When connecting up
the boiler the clearances in fig 1 should
be respected.
The boiler is supplied with a valve pack
part number 5184817A. The boiler can be
filled and pressure tested prior to any
electrical supply being connected with
the use of the analogue pressure gauge.
A safety valve set at 3 bar is fitted to the
appliance, the discharge pipe provided
should be extended to terminate safely
away from the appliance and where
a discharge would not cause damage
to persons or property but would be
detected. The pipe should be a minimum
of 15 mm Ø and should be able to
withstand boiling water, any should
avoid sharp corners or upward pipe
runs where water may be retained.
Gas Connection
The gas connection must be made
using seamless steel or copper pipe.
Where the piping has to pass through
walls, a suitable insulating sleeve must
be provided. When sizing gas piping,
from the meter to the boiler, take into
account both the volume flow rates
(consumption) in m
3
/h and the relative
density of the gas in question. The
sections of the piping making up the
system must be such as to guarantee
a supply of gas sufficient to cover the
maximum demand, limiting pressure
loss between the gas meter and any
apparatus being used to not greater
than 1.0 mbar for family II gases (natural
gas). An adhesive data badge is sited
inside the front panel; it contains all the
technical data identifying the boiler and
the type of gas for which the boiler is
arranged.
2.3.1 Connection of condensation
water
trap
To ensure safe disposal of the condensate
produced by the flue gases, reference
should be made to BS6798:2009.
The boiler incorporates a condensate
trap which has a seal of 75 mm, therefore
no additional trap is required. The
advised method of connection to the
condensate trap is by using 20 mm
overflow pipe with a socket attached to
cover the condensate trap connection.
The condensate should ideally be
discharged internally into an internal
waste pipe(washing machine/sink
waste) or a soil pipe to avoid the risk
of freezing.
External pipe runs should be avoided, but
if it is necessary, the pipework should be
at least 32mm and protected from the risc
of freezing with a waterproof insulation
and the length kept to a minimum and
not exceeding 3 m. termination should
be into an external gully or purpose
made soakaway.
NOTE: All pipework must have a
continuous fall from the boiler and must
be resistant to corrosion by condensate,
copper or steel is NOT suitable.
It should be noted that the connection
of a condensate pipe to a drain may
be subject to local building control
requirements.
2.3.2 Dealing with condensate
See APPENDIX A for guidance on the
disposal of condensate.
2.3.3 Requirements for sealed water
systems (fig. 5)
The heating system design should be
based on the following information:
a) The available pump head is given in
fig. 14.
b) The burner starts if the system
pressure is sufficient to operate the
pressure switch.
c) The appliance is equipped with an
internal by-pass that operates with
system heads (H) greater than 3
m. The maximum flow through
the by-pass is about 300 l/h. If
thermostatic radiator valves are to
be installed, at least one radiator
should be without a thermostatic
valve (usually the bathroom radiator
or the radiator in the room containing
2 INSTALLATION
10
1
2
3
4
KEY
1 Wall mounting bracket
2 Plastic wall plug (2 Off)
3 Woodscrew (2 Off)
4 Washer (2 Off)
Fig. 4
Summary of Contents for COMFORT 30
Page 3: ......
Page 28: ...28 7 EXPLODED VIEWS...
Page 29: ...29...
Page 45: ...NOTES...
Page 46: ...NOTES...
Page 47: ......
Page 48: ...iqe co uk Trade House BA22 8RT Phone 0800 0152252...