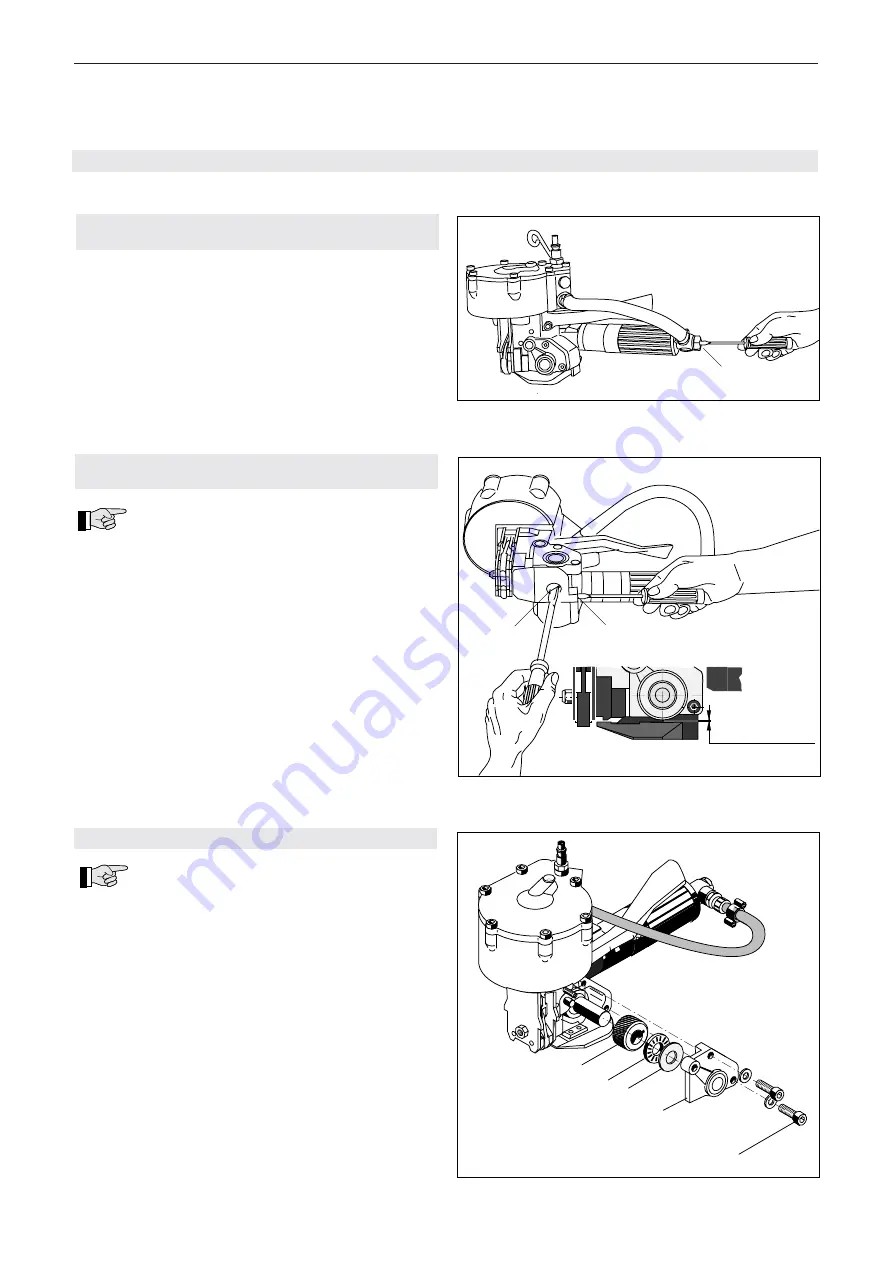
24
01.05/WE
ORGAPACK CR 25 A
7.1 ADJUSTING TENSIONING FORCE/
TENSIONING SPEED
– Set air pressure at pressure reducing valve of
maintenance unit to 4–6 bar.
– With a screwdriver adjust pressure reducing valve
(9/1) of air motor, so that the motor stops when the
required tension is reached. It should be ensured
that the seal is notched properly and that the strap
is cut off.
7.2 SETTING CLEARENCE BETWEEN TENSION
WHEEL AND TENSION PLUG
The tension wheel and the tension plug must
not touch (damage the teeth). If the spacing
is too great, the strap slips through before the final
tension is reached.
– Disconnect tool from air supply.
– Loosen set screw (10/1).
– Set tension plug (10/2) with screwdriver, so that the
clearence between tension wheel and tension plug
is 0.1–0.25 mm (.0039“–.0098“). Turning clockwise
decreases the clearence, turning counterclockwise
increases the clearence.
– Turn tension plug so that a notch of the tension plug
points in the direction of the set screw (10/1).
– Tighten set screw (10/1).
– Check clearence, reset if necessary.
7.3 REPLACING TENSION WHEEL
If the tension wheel spins before the required
strap tension is reached, the tension wheel
must be replaced (precondition: clearence set correctly,
see chapter 7.2).
Removal
– Disconnect tool from air supply.
– Remove two cylinder screws (11/1).
– Carefully remove cover (11/2) from tension shaft.
– Remove counter washer (11/3), thrust bearing (11/4)
and tension wheel (11/5). Replace tension wheel.
Installation
– Install the parts in reverse order.
– The 45°-chamfer of the tension wheel must be out-
side.
– Secure cylinder screws (11/1) with Loctite 243.
– Set clearence between tension wheel and tension
plug (see chapter 7.2).
7
PREVENTIVE AND CORRECTIVE MAINTENANCE
Fig. 11
Fig. 10
Fig. 9
1
1
2
0,1–0,25 mm
1
2
4
5
3