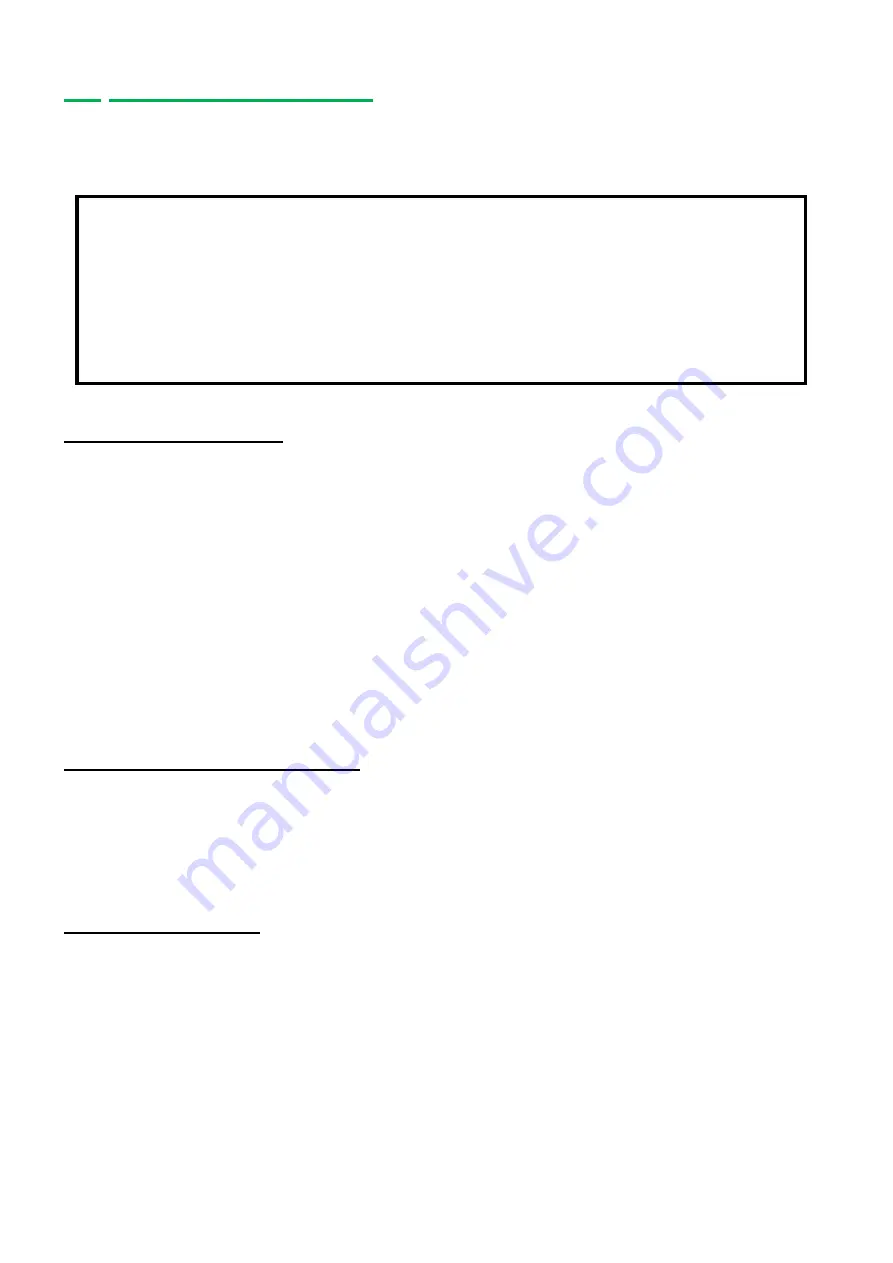
4
1.0 SAFETY WARNINGS
Please read and observe all warnings contained in this operations manual before making any
attempt to operate the equipment.
Misuse of equipment
Misuse of equipment can cause serious bodily injury. Use the equipment only for its intended
purpose and do not attempt to modify it in any way. Care should be taken to prevent over
pressurization of the pump, hose lines and accessories connected to it. Use only IPM designated
parts for re-building or repairing this equipment. Use the pump only with compatible fluids.
Improper use of this equipment could result in fluid being sprayed on the skin or in the eyes of
user, serious bodily injury, property damage, fire or explosion.
D
aily maintenance inspection should be made on pumps and equipment and all worn or
damaged parts should be re-placed immediately. Do not use pumps, components or hose lines
as leverage to move equipment to avoid damage and injury. Do not alter this equipment as doing
so could cause it to function incorrectly and/or cause serious injury. Altering this equipment in
any way will also void any and all warranty guarantees from the manufacturer.
Material & fluid compatibility
Always ensure the chemical compatibility of the fluids and solvents used in the fluid section of
these pumps, hoses other components. Check the chemical manufacturer’s data sheets and
specification charts before using fluids or solvents in this pump to ensure compatibility with
pumps, inner hose lining and outer hose covering.
Pressurized hoses
Because the hoses are pressurized they can present a danger should the fluid escape due to
damage, worn parts or general miss-use. Escaping fluid can splash or spray operator, causing
serious bodily injury and/or damage to equipment and property. Ensure that the hoses do not
leak or rupture due to wear, misuse or damage.
Before each use, ensure that the fluid couplings are tight and all clips/pins/plugs are secured.
Inspect the entire length of hose for wear, cuts, abrasions, bulging cover and/or loose
connections. These conditions may cause the hose to fail and result in splashing or spraying of
chemicals on the skin or in the eyes of operator and cause serious injury and/or property
damage.
Warning
To reduce the risk of static sparking or splashing fluid in the eyes or on the skin, follow
the
Pressure Relief Procedure
before flushing.
For your safety, read the
Fire or Explosion Hazard
before flushing and follow all the
listed recommendations.
Summary of Contents for OP 820301
Page 15: ...15 3 2 Parts list for 820301 820302 820303 Air motor section...
Page 16: ...16 3 3 Parts list for 820301 Fluid section...
Page 17: ...17 3 4 Parts list for 820302 Fluid section...
Page 18: ...18 3 5 Parts list for 820303 Fluid section...
Page 22: ...22 7 0 PERFORMANCE...
Page 23: ...23...