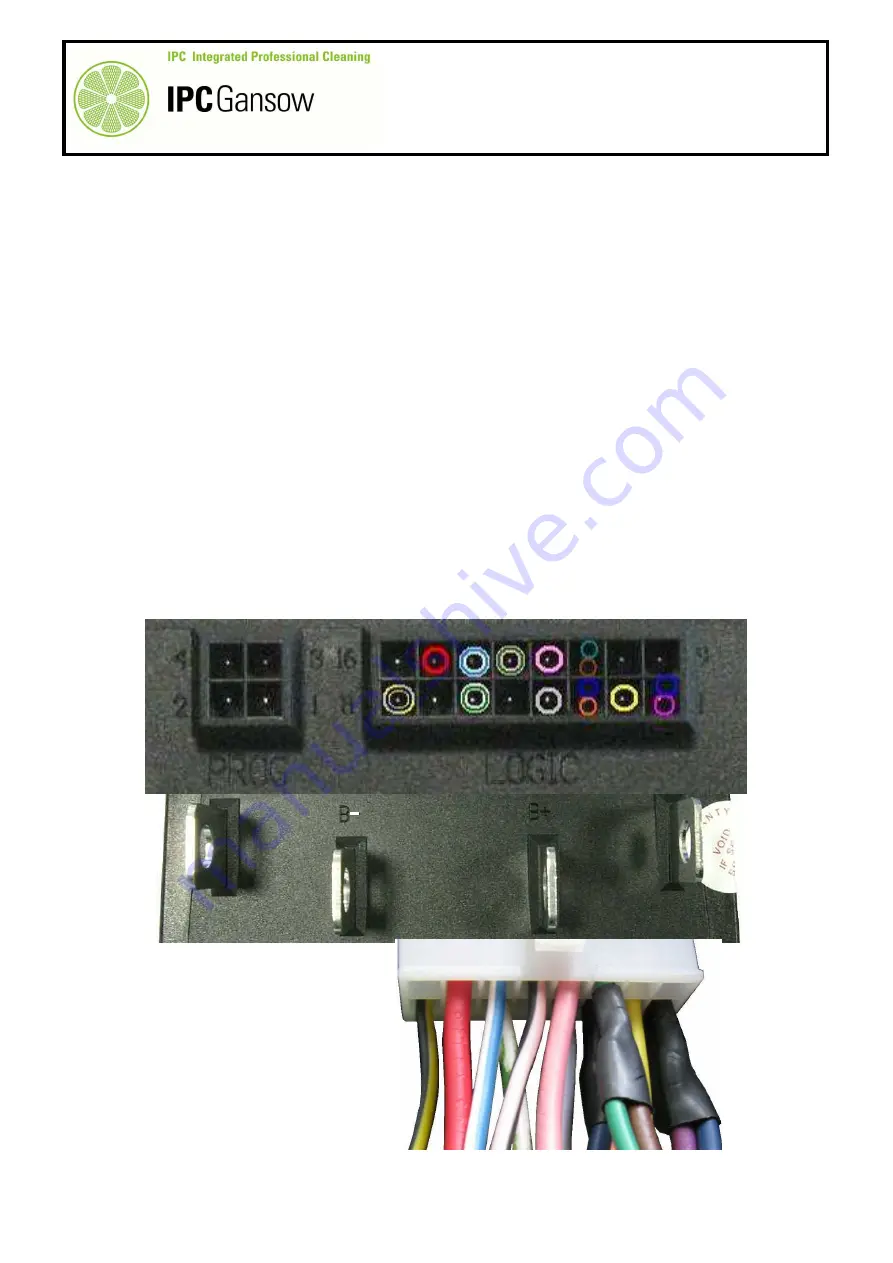
PLDC01938
REVISION 00
01/06/2011
TECHNICAL DEPT
Stavale
- date 05/09/2011
140/195
11
Place the front wheel in the straight position (to activate the steering sensor), sensor LED on, and proceed to
measure the input voltage on the board between the BROWN wire, pin 11, (connected together with the
green wire, corresponding to the Curtis interface board, it indicates the reduction in speed to the control
panel board) and the negative power contact B-. If everything is OK, the voltage will be +36 V.
11a
If there is no voltage, check the continuity of the wires and/or correct functioning of the steering sensor. If
necessary adjust or replace it (see paragraph C5).
12
Read the output voltage between the YELLOW-BLACK wire, pin 8, and the positive power contact B+.
There must be a voltage of -36 V. This voltage powers the drive contactor and is available only if point 13 is
respected.
13
Bridge the “operator present” sensor (under the seat), make sure the parking brake is off, press the
accelerator pedal lightly until you hear the “click” of the micro switch and proceed to read the input voltage
between the WHITE-GREEN wire, pin 6, (INHIBIT) and the positive power contact B+. There must be a
voltage of -36 V.
Through the WHITE-GREEN wire, the control panel board supplies the drive board with a
voltage of -36 V only if the conditions of operator present, parking brake off and accelerator
pedal pressed are respected.
If the control panel board malfunctions, the drive board does not function, as there is
no INHIBIT input signal as described in point 13.
B
16
8
9
1
LOGIC
B+
PHOTO 296
A2
M-
B-
B+