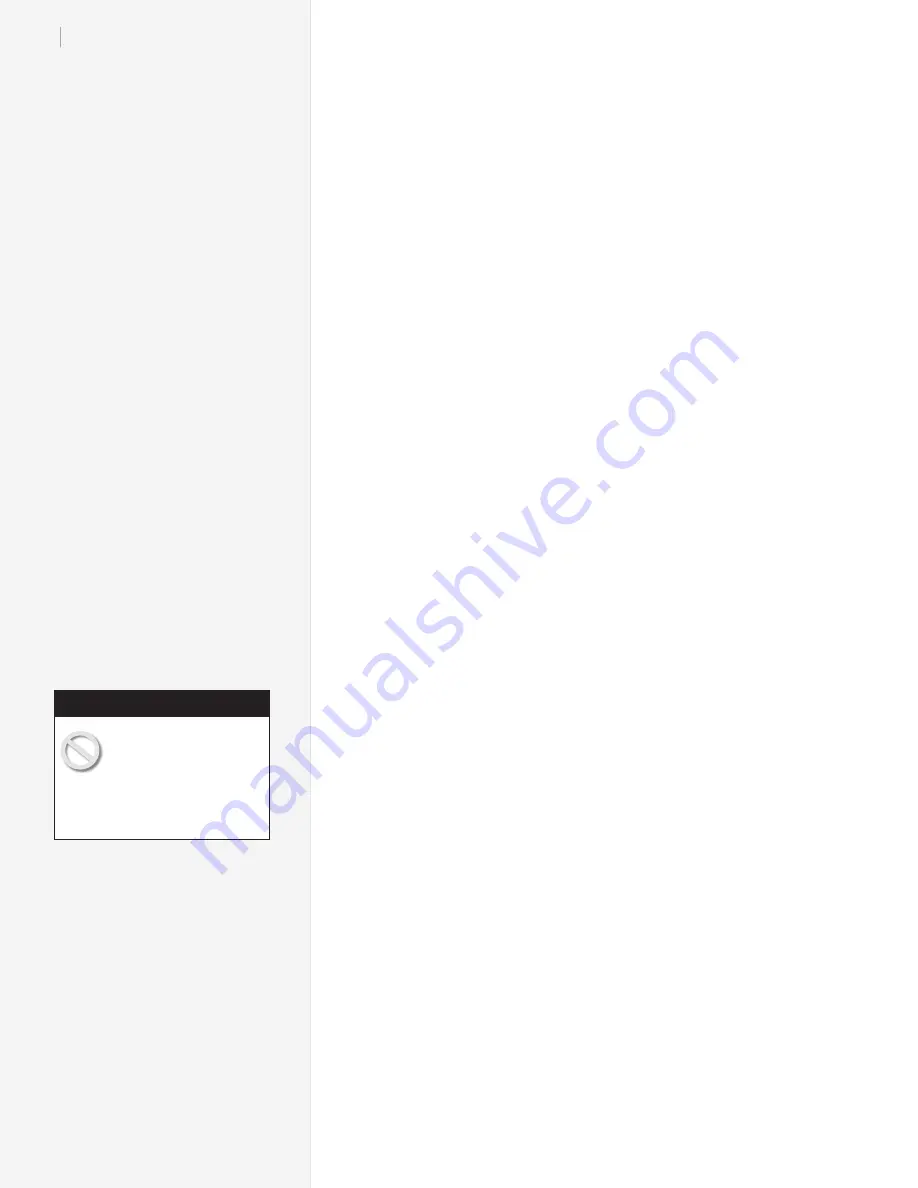
30
Ioline SmarTrac User Guide
Aligning the Material and Pinchwheels
Ioline recommends using the “Typewriter Method” to align the mate-
rial to the platen. The drive shaft is optimized for most common mate-
rial widths as well as scraps. When loading material, use the drive
shaft markers on the traverse to find the drive shaft segments.
1.
Lift the pinchwheels by raising the pinchwheel lever on the
right side of the signcutter. Bring the material up and through
the space under the pinchwheels. Pull down enough material
to reach the media rollers on the stand (I/S 80, SC-40 and larger
models) or about one foot (25-cm) on the table-top cradle-
mounted I/S 60 models.
2.
Roughly align the material so that the edges are overlapping
the wide-right drive shaft segment and one of the smaller seg-
ments. Use the drive shaft markers on the traverse to find the
drive shaft segments when they are covered by material.
3.
Position the outer-pinchwheels on the material about 1-in (2.5-cm)
from the edge. Use the drive shaft markers on the traverse as a
guide to make sure the wheels are over a drive shaft segment.
4.
Slide the inner-idler wheels (when provided) so that they are
as close to evenly spaced between the outer wheels as possible
while remaining over a drive shaft segment. Use the drive shaft
markers on traverse to ensure that the wheels are positioned
correctly.
5.
With both hands, reach under the stand or cradle and clasp
the front edges of the sides of the material hanging from the
front of the machine against the edges of the material hanging
from the back of the machine. Pull downward on the material
and square the edges so that they are parallel front and back.
Alternatively, align the edge of the material with the edge of
the material roll.
6.
While maintaining the material square and taut, clamp the
pinchwheels to the material by lowering the pinchwheel lever
on the right side of the signcutter.
7.
Check alignment by using the
Arrow
keys to move the material
forward and back. The material edge should run straight.
Adjusting the Pinchwheel Pressure
I/S 80, SC-40 and wider models have pinchwheels with adjustable
spring force*. This allows the user to use maximum force (24 lbs.)
for holding vinyl (which requires more force for better tracking) or
less force (8 lbs.) for lightweight materials like paper and for sand-
blast resists that must be tracked directly on the rubber surface. The
pinchwheels can also be set in a position that keeps them completely
off the surface so that the inner pinchwheels on larger cutters will
not interfere with pen plotting.
Set
Force Adjustment
by turning the screw on the back of the
pinchwheel assembly.
1.
Move the pinchwheel to the access hole on the back of the dust cover.
2.
Insert a flat screwdriver into the slot and turn the adjustment
screw 90 degrees. When the slot is in the vertical position on the
outer wheels, the force is 24-lbs. The horizontal position indi-
While checking alignment
with the
Arrow
keys,
make sure that the mate-
rial between the material roll and
the signcutter is never pulled taut
with the drive shaft.
Caution
* This option is not available on all
SmarTrac models.