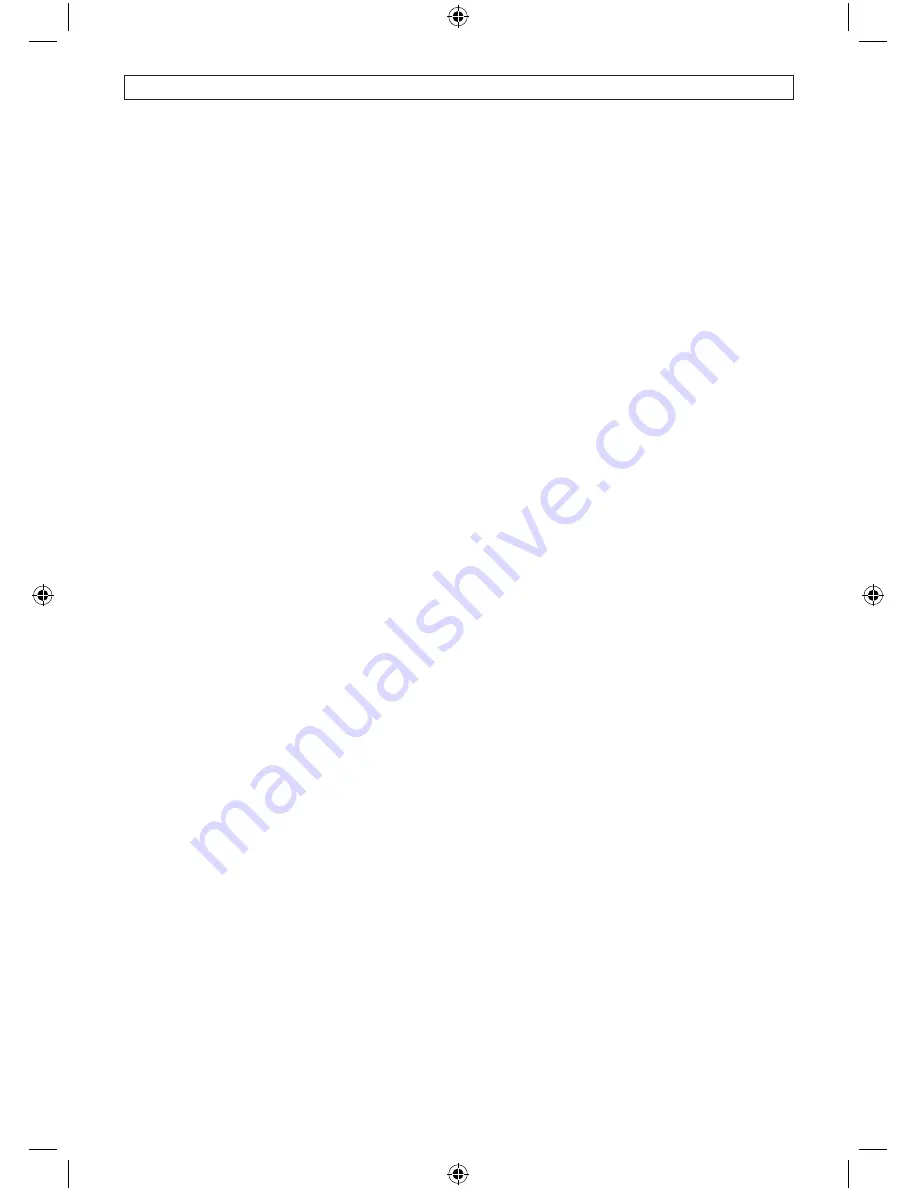
TIG WELDING FUNCTION & OPERATION
(13) Rotate the control knob (F8) clockwise until the text 'PULSE TIME' is displayed in window (F9).
Rotate control knob (F1) to select the required high pulse time.
(14) Rotate the control knob (F8) clockwise until the text 'DOWN SLOPE TIME' is displayed in window
(F9). Rotate control knob (F1) to select the required slope down time.
(15) Rotate the control knob (F8) clockwise until the text 'CRATER CURRENT is displayed in
window (F9). Rotate control knob (F1) to select the required crater amps level.
(16) Rotate the control knob (F8) clockwise until the text 'CRATER TIME' is displayed in window
(F9). Rotate control knob (F1) to select the required crater current time.
(17) Rotate the control knob (F8) clockwise until the text 'POST GAS' is displayed in window (F9).
Rotate control knob (F1) to select the required post gas time.
(18) Rotate the control knob (F8) clockwise until the text 'TIG SWITCH' is displayed in window (F9).
Rotate control knob (F1) to select either 2T or 4T touch operation. In 2T operation the weld
sequence will start and stop as selected when the torch switch is depressed and released. In 4T
operation when the torch switch is depressed the arc will strike in and hold at the start current
level, when the switch is released the arc will upslope to the main welding current level. When
the switch is again depressed the arc will down-slope and hold at the crater current level, when the
switch is released the arc will switch off. If the torch switch is released during the down slope time
the weld will switch of at that point.
(19) Rotate control knob (F8) clockwise until the text 'REMOTE CURRENT' is displayed in the window
(F9). Rotate control knob (F1) in an anticlockwise direction so that the text in window (F9)
reads 'PANEL CONTROL'
(20) It is not necessary to adjust the welding sequence menu parameters in the order as described.
Any parameter can be individually adjusted by rotating the control knob (F8) in either direction until
the required area of the program is displayed in the window (F9) and the adjustment made as
required using control knob (F1)
(21) When all required parameters have been set in the sequence menu program, the unit will store
the data until any further adjustment is made. The data will also be stored ready for future use
even when the mains power is switched off.
(22) Using the correct safety equipment to protect both the body and the eyes, hold the torch at an
angle of 45 degrees so that the tungsten electrode is approximately 2-3 mm away from the work
piece. Depress the torch switch, the gas will start to flow and a HF spark will jump from the
tungsten to initiate the welding arc.
(23) Once the welding arc is established the unit will operate as programmed. At any time in the 2T
switch mode the welding arc can be stopped by releasing the torch switch. In the 4T switch mode
the arc is stopped by pressing and releasing the torch switch.
(24) Complete the welding application as required making output and control parameter adjustments
as necessary.
(25) If at any time the welding arc is broken prior to signalling the machine to switch off, the dead man
device installed in the machine will be activated and it will not be possible to re-strike the arc until
the post flow gas time has completed.
(26) When the welding application is completed, turn the power switch (F6) to the off position and
disconnect the unit from the mains power supply.
6
6
24pp A5 Instruction Manual.indd 9
28/9/06 3:33:11 pm