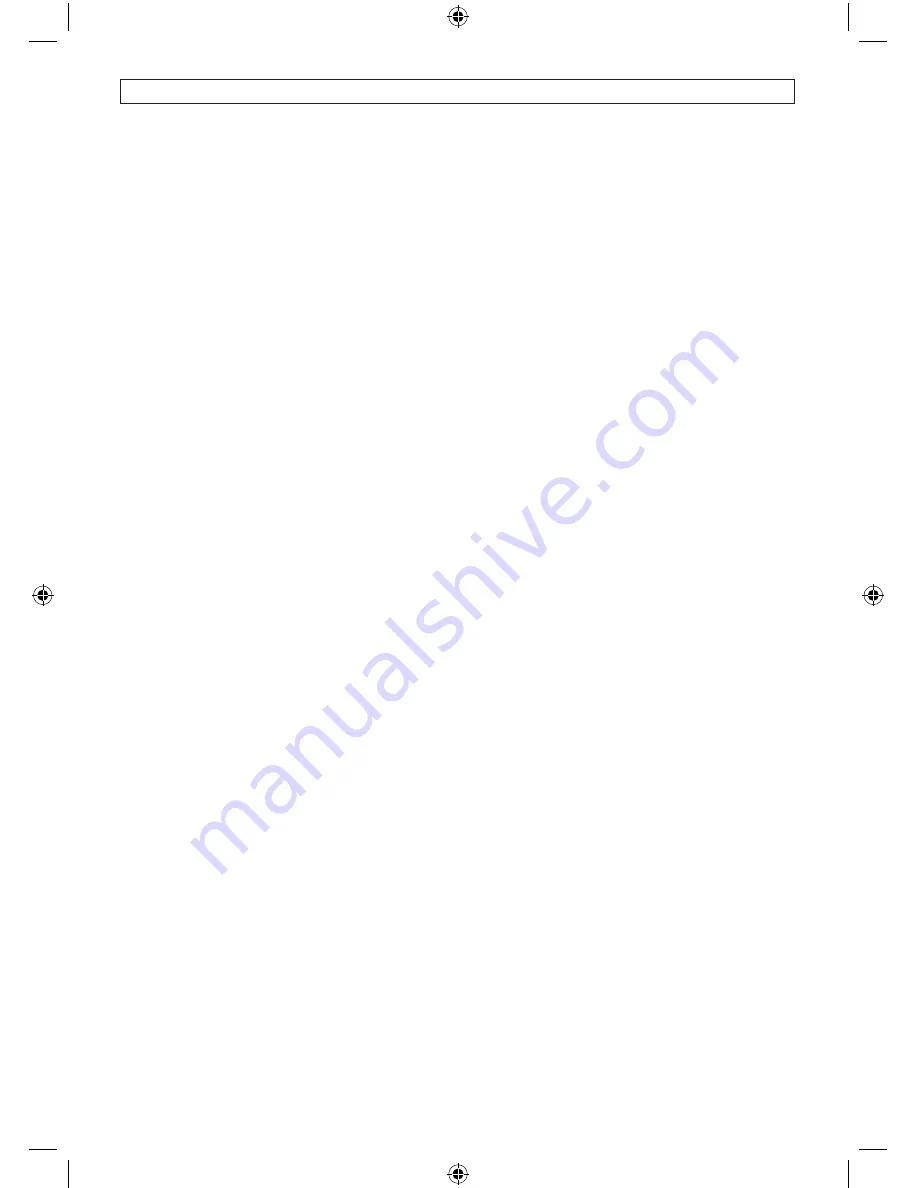
TIG WELDING FUNCTION & OPERATION
5.
LIFT TIG WELDING SET UP (Panel Control)
(1)
To use the machine for LIFT TIG applications follow the instruction as described and
detailed for' HF TIG Welding Set Up' in paragraphs (1) through to (8)
(2)
Rotate the control knob (F8) clockwise until the text 'HF START is displayed in window
(F9). Rotate control knob (F1) anticlockwise to switch the HF start off. When the HF start is
switched off the LED 4 will not be illuminated. The machine will now operate in a Lift TIG
mode and no HF will be present at the start of the welding sequence.
(3)
Continue to complete the program sequence set up as described for 'HF TIG Welding Set
Up' In section 4 paragraphs (10) through to (21)
(4)
Using the correct safety equipment to protect the body and the eyes, rest the torch gas
shroud on the work piece at an angle of 45 degrees to the work piece. Depress the torch
switch, this will start the shielding gas to flow, still resting the torch gas shield on the work
piece, rotate the torch forward until the tungsten electrode touches the work piece, then lift
gently away approximately 4mm. This will cause the arc to establish and the welding
application can be commenced. The method of starting the arc in the Lift TIG mode
requires that the electrode is made to momentary make contact with the work piece,
practice will provide the individual operator with the best method of completing this task.
(5)
Complete the welding application and set up procedure as detailed in 'HF TIG Welding Set
Up' in paragraphs (23) through to (26).
6.
TIG WELDING SET UP (Remote Current Control)
(1)
Connect the remote current control device to be used into the receptacle (F12/F13) and
complete the set up and operational instructions as detailed for HF TIG Welding Set-Up in
paragraphs (1) through to (18).
(2)
Rotate control knob (F8) clockwise until the text 'REMOTE CURRENT' is displayed in the
window (F9). Rotate control knob (F1) in either direction so that the text in window (F9)
reads 'FOOT CONTROL' or TORCH CONTROL'
(3)
Complete the welding application and set up procedure as detailed in 'HF TIG Welding Set
Up' in paragraphs (20) through to (26).
(4)
If 'FOOT CONTROL' is selected the machine will switch on and off when the foot switch is
depressed and released. The welding output current will increase and decrease as the
footswitch regulation is varied. Full depression of the footswitch will allow up to 99% of the
welding current value as selected on the (F2) display meter. If the 'FOOT CONTROL'
option is selected then Start Current, Up-Slope Time, Down-Slope Time and Crater Current
settings in the LCD window menu are disabled. The operator will have full control of all the
functions via the remote control foot pedal device.
(5)
If TORCH CONTROL' is selected this will allow the main welding output current to be
controlled from a remote current adjustment control device. The welding output current will
increase and decrease as the remote regulation is varied and will allow variation of the
welding output current value as selected on the (F2) display meter. The machine welding
sequence will be switched On & Off as detailed in HF TIG Welding Set Up paragraph (18).
When a remote current device is adjusted, the output current as selected will be displayed
in the (F2) meter. All other available LCD menu options will be fully functional.
7
7
24pp A5 Instruction Manual.indd 10
28/9/06 3:33:12 pm