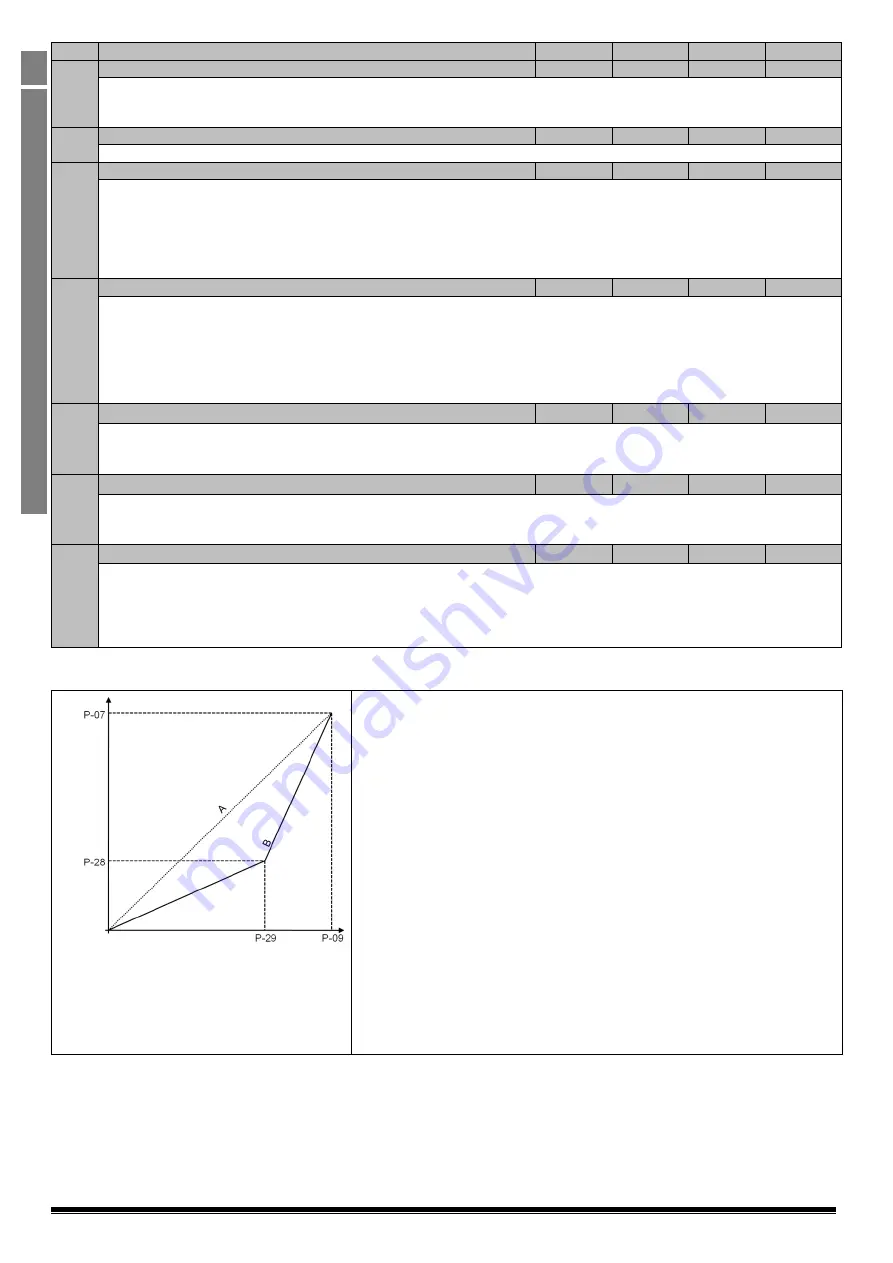
Optidrive ODE-2 User Guide Revision 3.20
20
www.invertekdrives.com
6
Pa
ra
m
eter
s
Par.
Description
Minimum
Maximum
Default
Units
P-44
PI Reference (Setpoint) Source Select
0
1
0
-
Selects the source for the PID Reference / Setpoint
0 : Digital Preset Setpoint
. P-45 is used
1 : Analog Input 1 Setpoint
P-45
PI Digital Setpoint
0.0
100.0
0.0
%
When P-44 = 0, this parameter sets the preset digital reference (setpoint) used for the PI Controller
P-46
PI Feedback Source Select
0
2
0
-
0 : Analog Input 2
(Terminal 4)
1 : Analog Input 1
(Terminal 6)
2 : Motor Current
3 : DC Bus Voltage
Scaled 0 – 1000 Volts = 0 – 100%
4 : Analog 1 – Analog 2
. The value of Analog Input 2 is subtracted from Analog 1 to give a differential signal. The value is limited to 0.
5 : Largest (Analog 1, Analog 2)
. The largest of the two analog input values is always used for PI feedback
P-47
Analog Input 2 Signal Format
N/A
N/A
N/A
U0-10
= 0 to 10 Volt Signal
= 0 to 20mA Signal
= 4 to 20mA Signal, the Optidrive will trip and show the fault code
if the signal level falls below 3mA
= 4 to 20mA Signal, the Optidrive will ramp to stop if the signal level falls below 3mA
= 20 to 4mA Signal, the Optidrive will trip and show the fault code
if the signal level falls below 3mA
= 20 to 4mA Signal, the Optidrive will ramp to stop if the signal level falls below 3mA
P-48
Standby Mode Timer
0.0
250.0
0.0
s
When standby mode is enabled, the drive will enter standby mode following a period of operating at minimum speed (P-02) for the
time set in P-48. When in Standby Mode, the drive display shows
, and the output to the motor is disabled.
Standby mode can be disabled by setting P-48 = 0.0
P-49
PI Control Wake Up Error Level
0.0
100.0
0.0
%
When the drive is operating in PI Control Mode (P-12 = 5 or 6), and Standby Mode is enabled (P-48 > 0.0), P-49 can be used to define
the PI Error Level (E.g. difference between the setpoint and feedback) for which the drive will remain in Standby Mode. This allows
the drive to ignore small feedback errors and remain in Standby mode until the feedback drops sufficiently.
P-50
Thermal Overload Value Retention
0
1
0
-
0 : Disabled.
1 : Enabled
. All Optidrives feature electronic thermal overload protection for the connected motor, designed to protect the motor
against damage. An internal overload accumulator monitors the motor output current over time, and will trip the drive if the usage
exceeds the thermal limit. When P-50 is disabled, removing the power supply from the drive and re-applying will reset the value of
the accumulator. When P-50 is enabled, the value is retained during power off.
6.3.
Adjusting the Voltage / Frequency (V/f) characteristics
Volt
age
The V/f characteristic is defined by several parameters as follows :-
P-07 : Motor Rated Voltage
P-09 : Motor Rated Frequency
The voltage set in parameter P-07 is applied to the motor at the frequency set Under
normal operating conditions, the voltage is linearly reduced at any point below the
motor rated frequency to maintain a constant motor torque output as shown by the
line ‘A’ on the graph.
By using parameters P-28 and P-29, the voltage to be applied at a particular frequency
can be directly set by the user, thereby altering the V/F characteristic.
Reducing the voltage at a particular frequency reduces the current in the motor and
hence the torque and power, hence this function can be used in fan and pump
applications where a variable torque output is desired by setting the parameters as
follows :-
P-28 = P-07 / 4
P-29 = P-09 / 2
This function can also be useful if motor instability is experienced at certain
frequencies, if this is the case increase or decrease the voltage (P-28) at the speed of
instability (P-29).
For applications requiring energy saving, typically HVAC and pumping, the energy
optimiser (P-06) parameter can be enabled. This automatically reduces the applied
motor voltage on light load.
Frequency