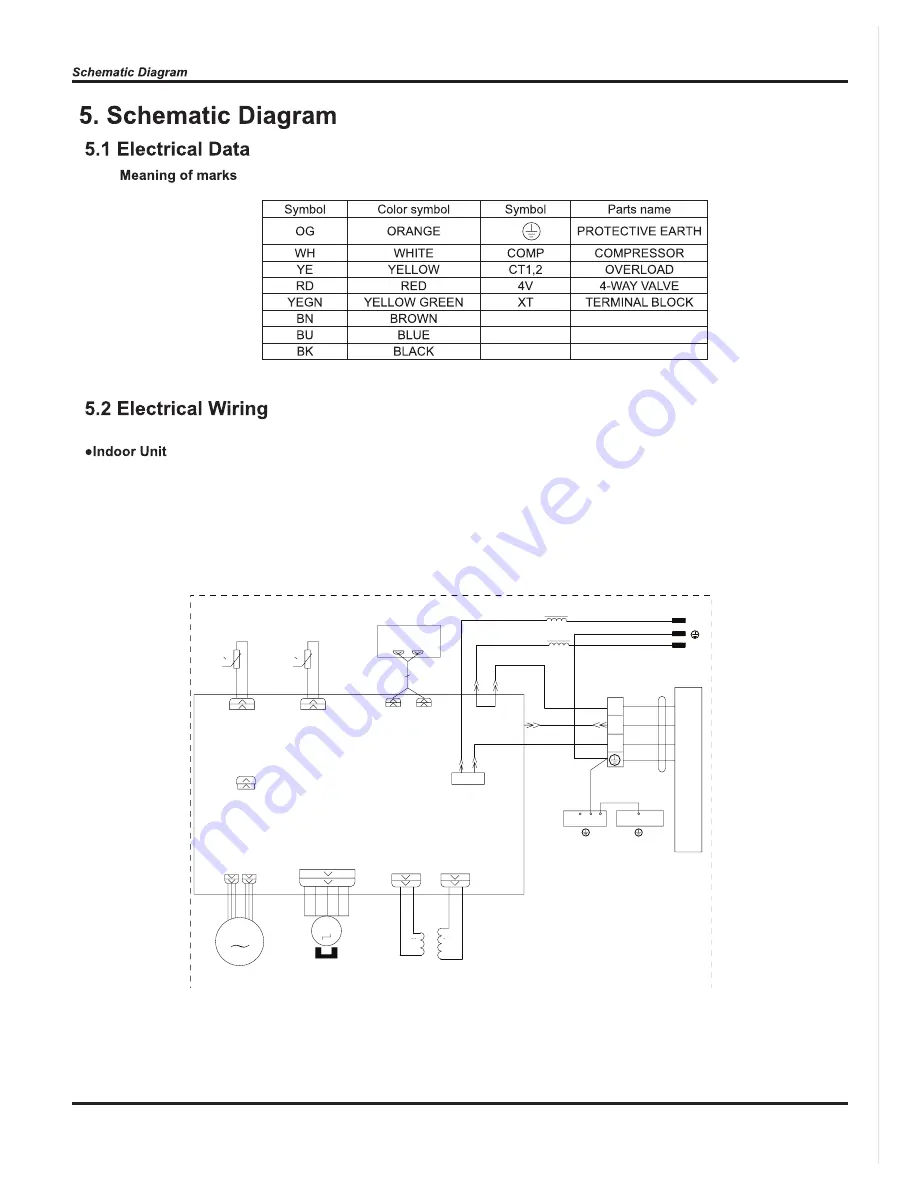
0
0
RT1
RT2
JUMP
CAP
TEM.SENSOR
ROOM
TUBE
TEM.SENSOR
FAN MOTOR
SWING MOTOR(U.D)
AP2
SWING-UD
K4
TUBE
ROOM
AC-L
PG
PGF
TR_OUT TR_IN
TC
TRANSFORMER
13
DISPLAY
AP1
CN1 CN2
DISP2
DISP1
M2
M1
PE
PE
L1
L1
I
II
L-OUT
ELECTRIC BOX
EVAPORATOR
XT1
W4BU
W3BN
N(1)
OUTDOOR UNIT
2
3
COM-OUT
W1YEGN
W2YEGN
N
W5BK
L
N
BU
YEGN
BN
BN
BU
YEGN
BK
POWER
12
Summary of Contents for C1VI-09
Page 1: ...C1VI 09 C1VO 09 C1VI 12 C1VO 12 ...
Page 2: ...a b e 2 3 3 7 7 8 8 9 10 11 12 12 12 14 16 16 19 24 24 26 27 28 ...
Page 3: ...Simply 29 30 31 31 35 39 39 62 59 43 46 44 59 ...
Page 5: ...2 ...
Page 6: ...C1VI 09 C1VO 09 C1VI 09 C1VO 09 C1VI 09 3 ...
Page 7: ...C1VO 09 4 ...
Page 8: ...C1VI 12 C1VO 12 C1VI 12 C1VO 12 C1VI 12 5 ...
Page 9: ...C1VO 12 6 ...
Page 12: ...9 ...
Page 13: ...10 ...
Page 17: ...1 2 3 4 5 6 7 8 9 10 11 12 14 ...
Page 18: ...11 10 9 8 7 6 13 12 14 5 4 3 2 1 15 ...
Page 24: ...21 ...
Page 25: ...A L B C D O 0 O 0 L1 A1 B1 C1 D1 heating angle cooling angle 22 ...
Page 26: ...23 ...
Page 27: ...24 ...
Page 28: ...25 ...
Page 33: ...Fig a filter Air filter Fig b Fig c Healthy 30 ...
Page 35: ...C1VI 09 32 ...
Page 37: ...C1VI 12 34 ...
Page 38: ...1 2 3 4 5 7 8 9 10 11 13 14 15 16 17 18 19 20 21 22 6 12 C1VO 09 35 8 2 Outdoor Unit ...
Page 39: ...C1VO 09 36 ...
Page 40: ...1 2 3 4 5 7 8 9 10 11 12 13 14 15 16 17 18 19 20 21 22 23 24 6 C1VO 12 37 ...
Page 41: ...C1V0 12 38 ...
Page 46: ...43 ...
Page 47: ...44 ...
Page 48: ...45 ...
Page 57: ...54 ...
Page 59: ...56 ...
Page 60: ...57 ...
Page 61: ...58 ...
Page 62: ...59 ...
Page 63: ...60 ...
Page 64: ...61 ...
Page 70: ......