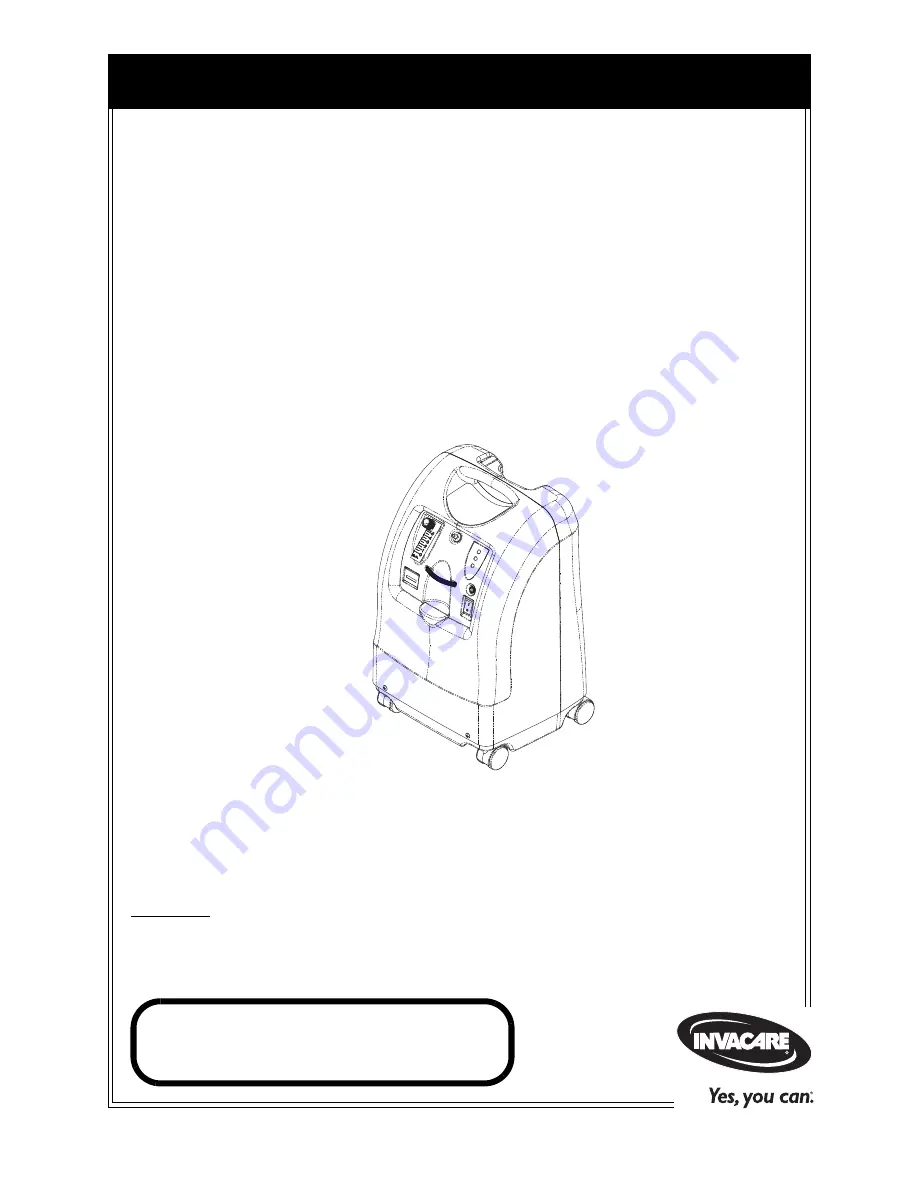
Service Manual
DEALER: Keep this manual. The procedures in this manual MUST be
performed by a qualified technician.
For more information regarding
Invacare products, parts, and services,
please visit www.invacare.com
Perfecto
2
™
V
Oxygen Concentrator
(HomeFill
®
Compatible)
Model IRC5PO2V (Sensored)