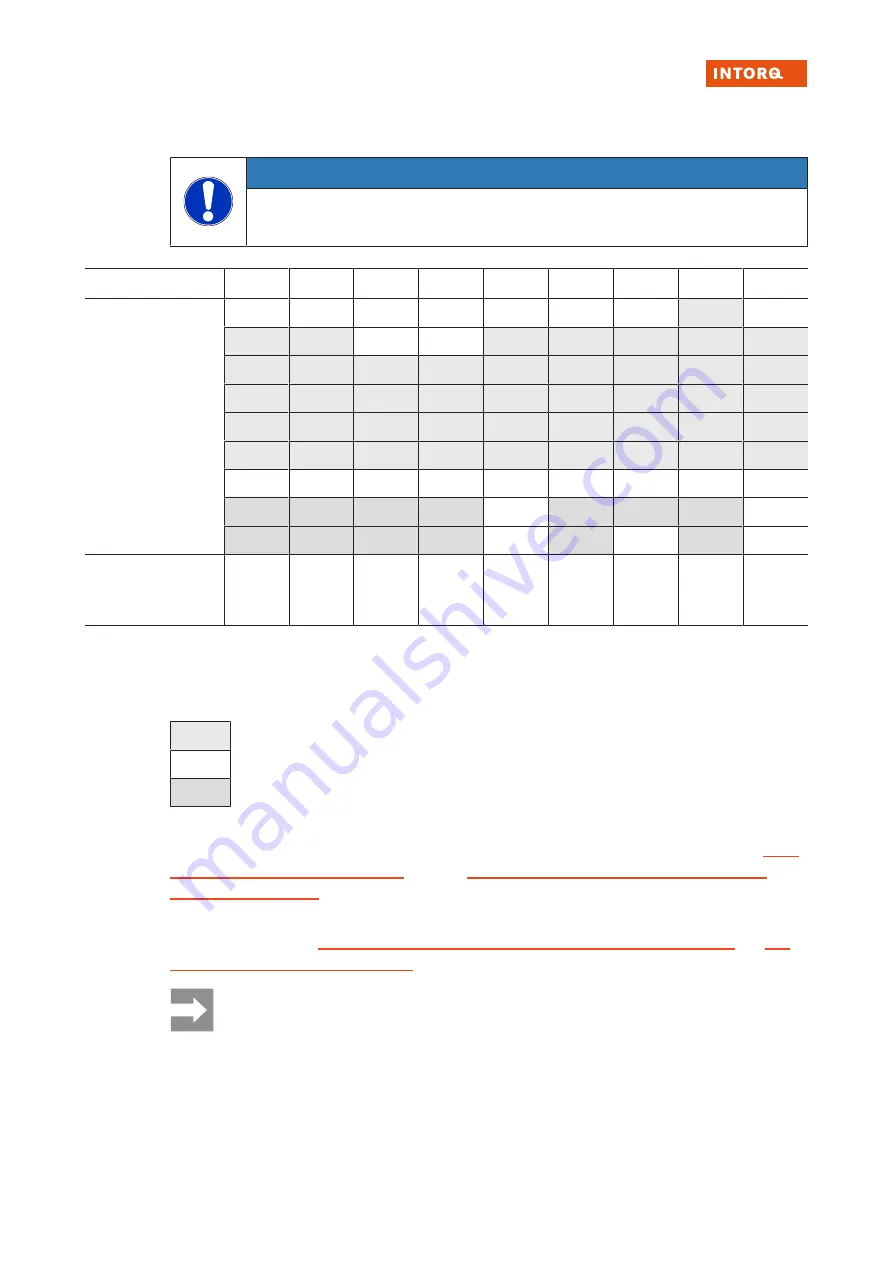
Technical specifications
INTORQ | BA 14.0217 | 09/2019
23
5.3
Brake torques
NOTICE
Please observe that engagement times and disengagement times change depending on
the brake torque.
Size
06
08
10
12
14
16
18
20
25
Rated torque M
K
[Nm]
of the brake, rated
value at a relative
speed of rotation of
100 rpm
Standard lining (ST)
and wear-resistant lin-
ing (WR)
80 E
1.5 E
3.5 N/E/L
25 N/E
35 N/E
65 N/E
115 N/E
175 N/E
2 N/E/L
4 E
7 N/E/L
14 N/E/L
35 N
45 N/E
80 N/E
145 N/E
220 N
2.5 N/E
5 N/E
9 N/E
18 N/E
40 N/E
55 N/E
100 N/E
170 N/E
265 N/E
3 N/E/L
6 N/E/L
11 N/E/L
23 N/E/L
45 N/E
60 N/E
115 N/E
200 N/E
300 N/E
3.5 N/E/L
7 N/E/L
14 N/E/L
27 N/E/L
55 N/E
70 N/E
130 N/E
230 N/E
350 N/E
4 N/E/L
8 N/E/L
16 N/E/L
32 N/E/L
60 N/E
80 N/E
150 N/E
260 N/E
400 N/E
4.5 N/E
9 N/E
18 N/E
36 N/E
90 N/E
165 N/E
290 N/E
5 E
10 E
20 E
40 E
100 N/E
315 N/E
Torque reduction per
detent [Nm], for design
type E
0.2
0.35
0.8
1.3
1.7
1.6
3.6
5.6
6.2
Tab. 2:
Braking torques and possible brake torque reduction: Adjustable for the design types
N Type without brake torque adjustment
E Type with brake torque adjustment
L Type in the long-life version
Operating brake (s
Lmax
approx. 2.5 x s
LN
)
Standard braking torque
Holding brake with emergency stop (s
Lmax.
approx. 1.5 x s
LN
)
For basic module E, the brake torque can be reduced using the torque adjustment ring in the stator. The
adjustment ring may only be unscrewed until the maximum protrusion (overhang) h
Emax
data for air gap specifications, Page 24
table and Brake torque reduction (for the optional adjustable
When using a standard friction lining, the maximum speeds and friction work Q
R
per brake frame size, as
specified in the sections Dust explosive atmosphere (zone 22: non-conductive dusts), Page 31 and Gas
explosive atmosphere (zone 2), Page 33, shall be applicable.
Notice
A version of the double spring-applied brake using HFC (high-friction coefficient) linings is not
permitted.