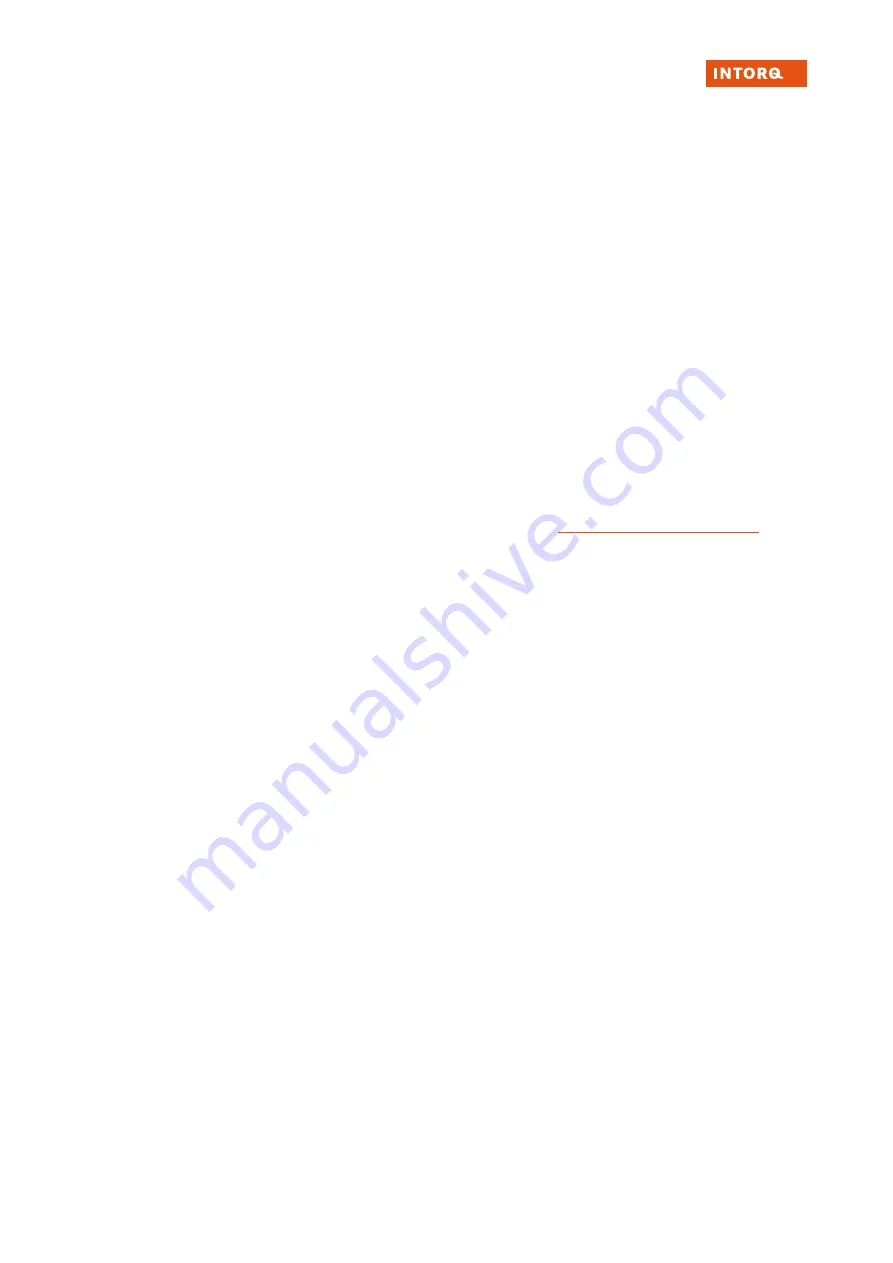
Project planning notes
INTORQ | BA 14.0217 | 09/2019
20
4
Project planning notes
¾
When designing a brake for specific applications, torque tolerances, the limiting speeds of the rotors,
the thermal resistance of the brake, and the effect of environmental influences must all be taken into
account.
¾
The brakes are dimensioned in such a way that the specified rated torques are reached safely after a
short run-in process.
¾
However, as the organic friction linings used do not all have identical properties and because environ-
mental conditions can vary, deviations from the specified braking torques are possible. These must be
taken into account in the form of appropriate dimensioning tolerances. Increased breakaway torque is
common in particular after long downtimes in humid environments where temperatures vary.
¾
If the brake is used as a pure holding brake without dynamic load, the friction lining must be reactiv-
ated regularly.
¾
You must comply with all technical specifications in order to ensure trouble-free operations of the
ATEX brake. In particular, the user-specific dimensioning of the brake must be checked according to
the specified limits of the friction performance charts (refer to Technical specifications, Page 21 ). If
the limit values from the friction performance charts are not adhered to, the brake and the friction sur-
face may overheat, which would lead to a risk of ignition. In such as case, the brake is no longer com-
pliant with the ATEX standards.
¾
The permissible operating frequency (number of switching operations) corresponding to the required
friction work is determined from the friction performance charts. The number of switching operations
must be evenly distributed over the course of one hour.
¾
The correct relation between the brake, motor, control and loads must be taken into account when di-
mensioning the brake.
¾
If the switching times of the brake in conjunction with the control of the drive is not properly taken into
consideration, the rotational speed could increase when the motor is switched off. As a result, the brak-
ing procedure would be carried out at a much higher speed and higher friction work than assumed in
the preliminary design. This would result in higher temperatures, which would then pose a risk of igni-
tion.
¾
Use only original INTORQ friction parts (flange and armature plate) and standard friction linings (ST)
for the ATEX brake.
¾
The brake is designed with one free cable end. This cable must be inserted into a suitable terminal box
(through a cable gland) in accordance with the ATEX directives.
¾
INTORQ's half-wave and bridge rectifiers and spark suppressors have not been designed for use in
potentially explosive atmospheres. If the use of these electrical components is necessary, they must
be installed within a control cabinet that is outside the explosive atmosphere.
¾
To temporarily release the brake when there is no electricity available, a hand-release function is avail-
able as an option. The hand-release function can be retrofitted; for this, the hand-release holes in the
magnetic housing of the brake must be closed.
¾
The use of a micro-switch for monitoring ventilation, wear and manual release is not permitted for
brakes that are used in an explosive atmosphere.