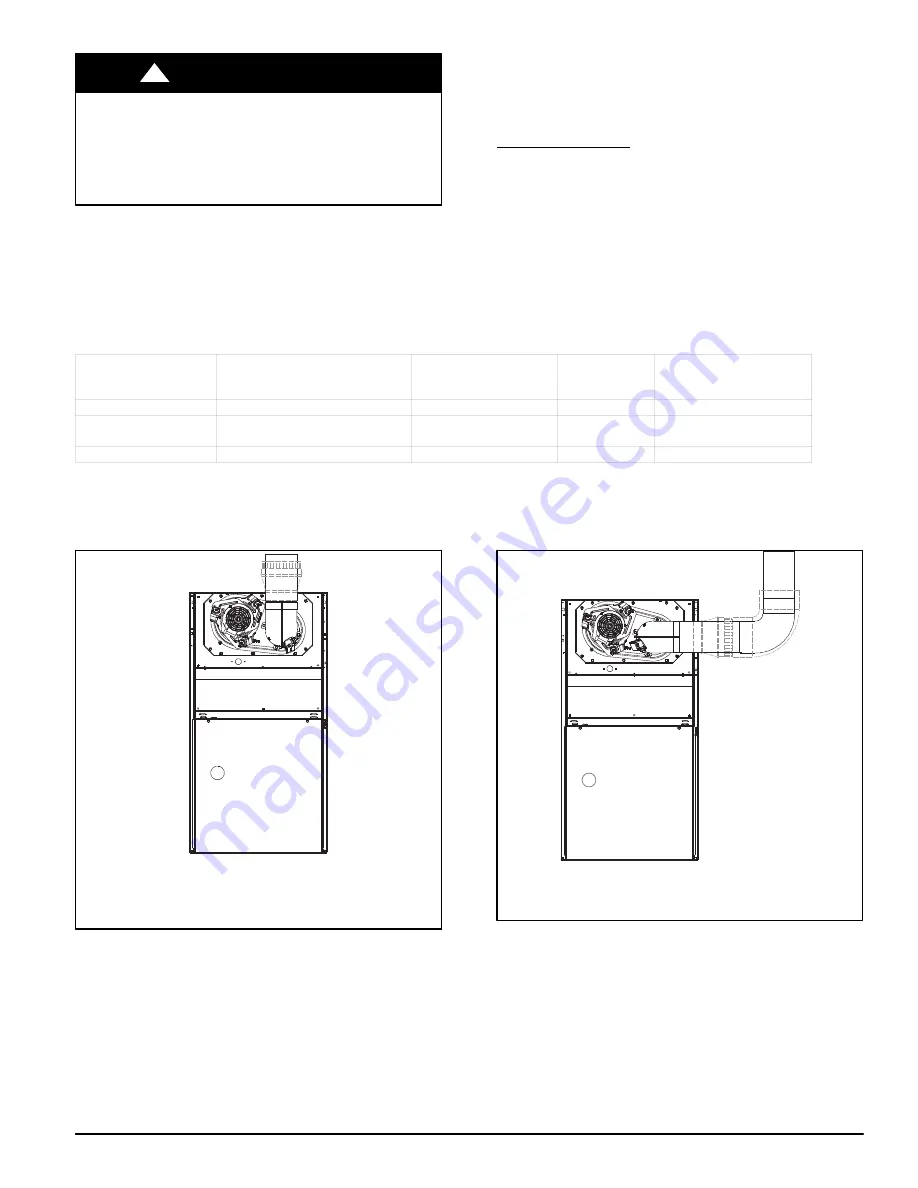
28
441 01 1411 04
Specifications are subject to change without notice.
BURN HAZARD
Failure to follow this caution may cause personal
injury.
Hot vent pipe is within reach of small children when
installed in downflow position. See the following
instruction.
CAUTION
!
An accessory Vent Guard Kit is REQUIRED for downflow
applications where the vent exits through the lower portion of
the furnace casing. See Figure 39. Refer to the Vent Guard
Kit Instructions for complete details.
The horizontal portion of the venting system shall slope
upwards not less than 1/4
−
in. per linear ft. (21 mm/M) from
the furnace to the vent and shall be rigidly supported every 5
ft. (2 M) or less with metal hangers or straps to ensure there
is no movement after installation.
SIDEWALL VENTING
This furnace is not approved for direct sidewall horizontal
venting.
Per section 12.4.3 of the NFPA54/ANSI Z223.1
−
2012, any
listed mechanical venter may be used, when approved by the
authority having jurisdiction.
Select the listed mechanical venter to match the Btuh input of
the furnace being vented. Follow all manufacturer’s
installation requirements for venting and termination included
with the listed mechanical venter.
Caution!! For the following applications, use the minimum vertical vent heights as specified below. For all other
applications, follow exclusively the National Fuel Gas Code.
FURNACE
ORIENTATION
VENT ORIENTATION
FURNACE INPUT
(BTUH/HR)
MIN. VENT
DIAMETER
IN (MM)*
MIN. VERTICAL VENT
HEIGHT
FT. (M)**
Downflow
Vent elbow left, then up Figure 39
132,000
5 (127 )
12 (4)
Horizontal Left
Vent elbow right, then up
Figure 42
132,000
5 (127 )
7 (2)
Horizontal Left
Vent elbow right Figure 43
132,000
5 (127 )
7 (2)
NOTE: All vent configurations must also meet National Fuel Gas Code venting requirements NFGC
*4 in. (102 mm) inside casing or vent guard
**Including 4 in. (102 mm) vent section(s)
Figure 35
−
Upflow Application
−
Vent Elbow Up
SEE NOTES: 1,2,4,7,8,9
on the page following
these figures
A03208
Figure 36
−
Upflow Application
−
Vent Elbow Right
SEE NOTES: 1,2,3,4,7,8,9
on the pages following
these figures
A03209