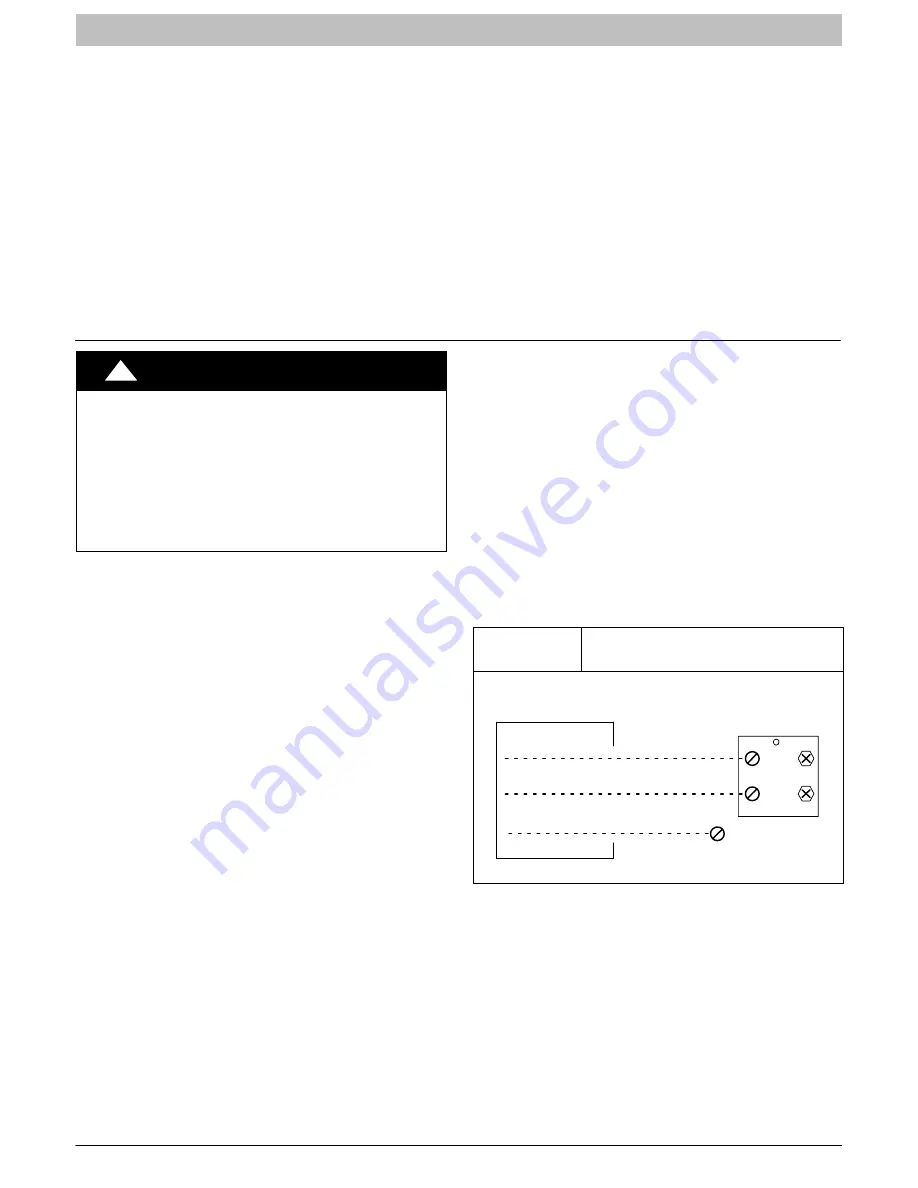
INSTALLATION INSTRUCTIONS
R-22 Split System Heat Pump
428 01 5001 00
9
J. OPENING SERVICE VALVES
Outdoor units are shipped with a refrigerant charge
sealed in the unit. Opening the service valves releases
this charge into the system.
NOTE:
Open the Suction service valve first. If the Liquid
service valve is opened first, oil from the compressor may
be drawn into the indoor coil TXV, restricting refrigerant
flow and affecting operation of the system.
Remove Suction service valve cap and insert a hex
wrench into the valve stem. Hold the valve body steady
with an end-wrench and back out the stem by turning the
hex wrench counterclockwise. Turn the stem until it just
contacts the rolled lip of the valve body.
After the refrigerant charge has bled into the system,
open the Liquid service valve.
NOTE:
These are not back-seating valves. It is not
necessary to force the stem tightly against the rolled lip.
The service valve cap is a primary seal for the valve and
must be properly tightened to prevent leaks. Make sure
cap is clean and apply refrigerant oil to threads and
sealing surface on inside of cap.
Tighten cap finger tight and then tighten additional
of a
turn (1 wrench flat) to properly seat the sealing surfaces.
K. GAUGE PORTS
Check for leaks at the schrader ports and tighten valve
cores if necessary. Install plastic caps finger tight.
ELECTRICAL WIRING
!
WARNING
ELECTRICAL SHOCK HAZARD
Failure to turn off the main (remote) electrical dis‐
connect device could result in personal injury or
death.
Before installing, modifying or servicing system,
turn OFF the main (remote) electrical disconnect
device. There may be more than one disconnect
device.
Supply voltage must be 208/230 volts (197 volt minimum
to 253 volts maximum) 60 Hz single phase.
Outdoor units are approved for use with copper
conductors only. Do not use aluminum wire.
Refer to unit rating plate for minimum circuit ampacity and
circuit protection requirements.
Grounding
Permanently ground unit in accordance with the National
Electrical Code and local codes or ordinances. Use a
copper conductor of the correct size from the grounding
lug in control box to a grounded connection in the service
panel or a properly driven and electrically grounded
ground rod.
Wiring Connections
Make all outdoor electrical supply (Line Voltage)
connections with raintight conduit and fittings. Most
codes require a disconnect switch outdoors within sight of
the unit. Consult local codes for special requirements.
Route electrical supply (Line Voltage) wiring through
knockout hole in bottom of Control Box. Connect wires to
Contactor and Ground Lug according to Wiring Diagram
on unit. Also refer to Figure 9.
Route thermostat wiring through rubber grommet in
bottom of Control Box. Low voltage lead wires are
provided in the control box for connection to thermostat
wires (use wire nuts). Refer to Wiring Diagram on unit and
Figure 10 for low voltage wiring examples.
NOTE:
Use No. 18 AWG (American Wire Gage)
color-coded, insulated (35
°
C minimum) wire. If
thermostat is located more than 100 feet (30.5 m) from
unit as measured along the control voltage wires, use No.
16 AWG color-coded wires to avoid excessive voltage
drop.
Figure 9
Electrical Supply (Line Voltage)
Connections
DISCONNECT
PER NEC AND/OR
LOCAL CODES
CONTACTOR
GROUND
LUG
FIELD GROUND
WIRING
FIELD POWER
WIRING
11
23 or 13
L1
L2