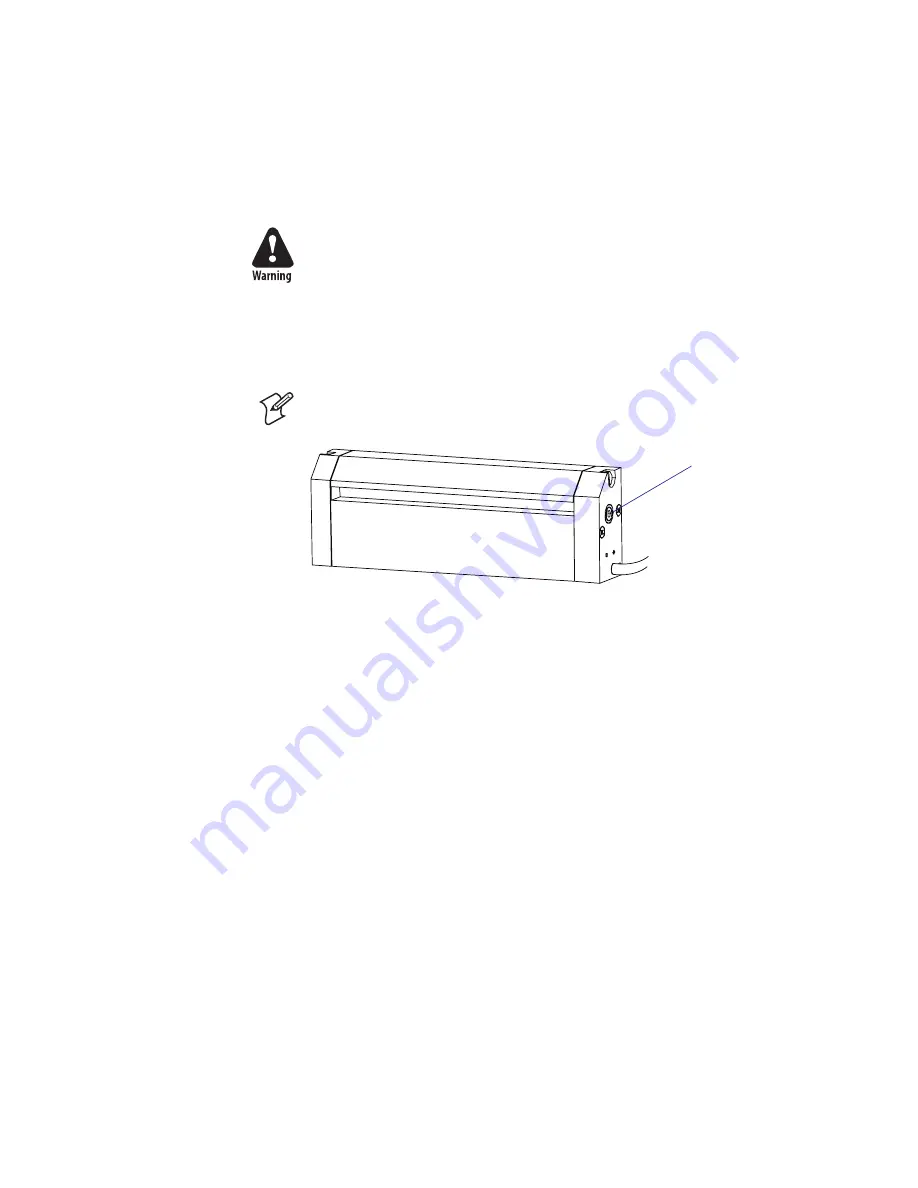
Intermec EasyCoder PD4—Service Manual
61
Chapter 10—Cutter
Clearing Media Jam in Cutter
To clear a media jam inside the cutter mechanism, follow the instructions
below:
1
At media jams and cutter malfunctions, switch off the power to the
printer.
Never insert fi ngers or tools into the printer while the power is still on.
Risk of personal injury or damage to the cutter if the cutter starts to
run by mistake.
2
Insert a 3 mm hexagon screwdriver in the hole on the side of the cutter
(A) and turn the cutter blade clockwise.
3
After the media jam is cleared, switch on the power to the printer, and
the cutter blade will go back to its original position.
Note:
It is recommended to use labels with a length of 35 mm (1.5 in) or
more.
A
Summary of Contents for EasyCoder PD4
Page 1: ...Service Manual EasyCoder PD4 Bar Code Label Printer ...
Page 4: ...iv Intermec EasyCoder PD4 Service Manual ...
Page 24: ...14 Intermec EasyCoder PD4 Service Manual Chapter 2 Front Panels ...
Page 36: ...26 Intermec EasyCoder PD4 Service Manual Chapter 5 Media Supply ...
Page 58: ...48 Intermec EasyCoder PD4 Service Manual Chapter 7 Print Mechanism ...
Page 66: ...56 Intermec EasyCoder PD4 Service Manual Chapter 9 Strip Module ...
Page 72: ...62 Intermec EasyCoder PD4 Service Manual Chapter 10 Cutter ...
Page 94: ...84 Intermec EasyCoder PD4 Service Manual Chapter 12 Main Board ...
Page 110: ...100 Intermec EasyCoder PD4 Service Manual Chapter 14 Troubleshooting ...
Page 113: ......