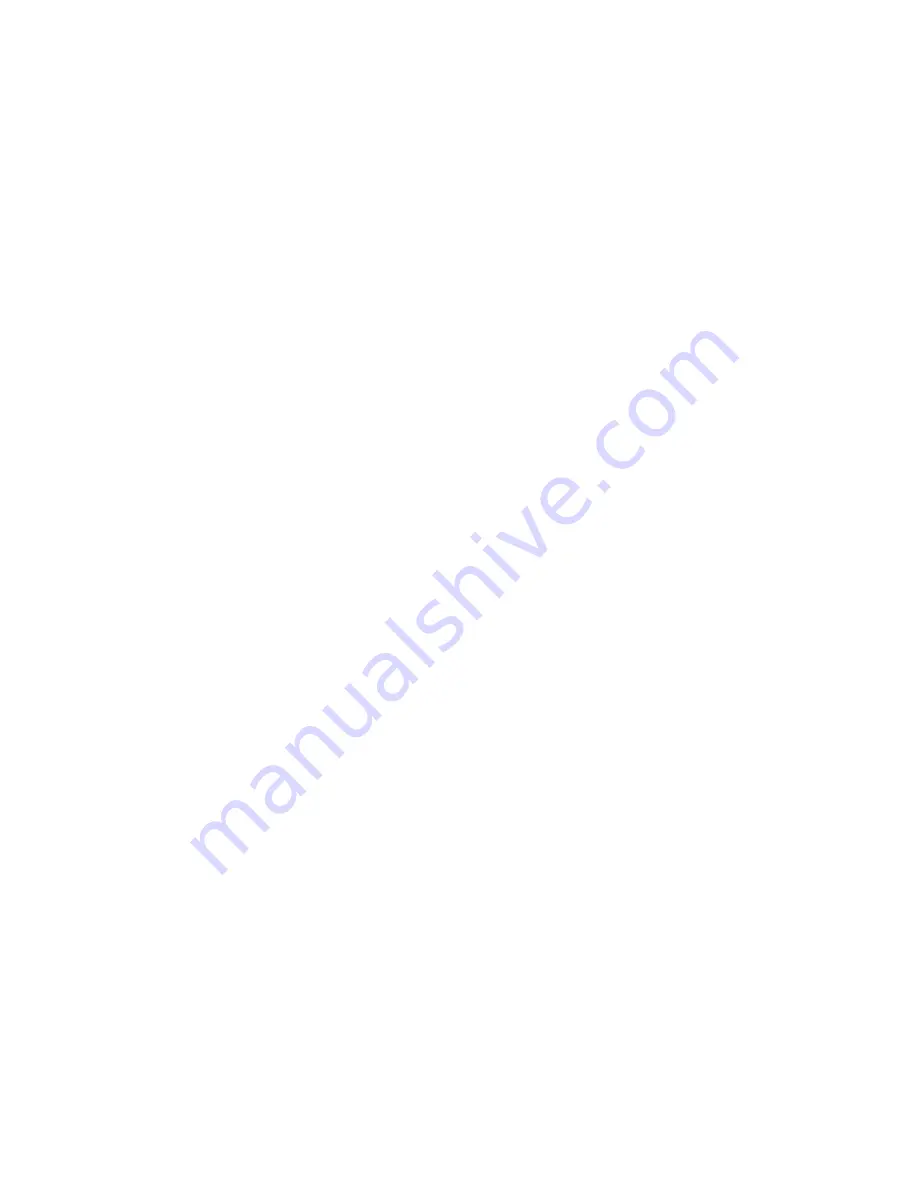
- 5 -
I:\OFFICE\Web Site\distiller pdf\100CSCE.wpd
2.
Insertion Probes —
Straight run is not critical, but if trying to hold a precise set point, some straight run is useful,
such as 10 to 20 pipe diameters on the inlet and at least 6 diameters on the outlet.
The various probe transducers are mounted through a threaded collar (NPT/2I) or flanged tee
(BF/2I). Other fittings and sensor designs are also available and are discussed on the Custom
Information page. Generally the probes are sized so the tips extend ½ to 1 inch beyond the pipe
center line when properly installed. However, for larger pipes, the probes may extend to within
1
/
8
of a diameter from the inside pipe wall.
Proper alignment of the sensor with flow is important; the flow direction is indicated on the
transducer tag and/or etched into the transducer. All dual probe transducers are installed so that
the two probes are side-by-side across the fluid stream. Never rotate the electronics box. If this
occurs the flow switch could be damaged and/or installed misaligned with the flow direction.
For high temperature applications, the sensor and surrounding line should be well insulated. Leave
a portion of the transducer neck un-insulated to allow heat dissipation before reaching the junction
box.
2.2 ELECTRICAL CONNECTIONS (See Figure 1)
!! CAUTION:
Prior to opening the electrical enclosure, service personnel
shall be properly grounded with an anti-static device to prevent damage to
components within the electrical enclosure.
The input power requirement is listed on the tag on the electronics enclosure; make sure the input power
source is compatible. The power requirement is 24 Vdc. The DC power supply must be well filtered and
grounded and comply with all applicable E.U. standards (i.e. EN61000-4 EMC).
The input power and relay connections are made as shown in Figure 1. Note the connector is removable for
easier insertion of the wires. Once all connections are made, firmly push the connector back onto its base.
Be sure the wires are stress relieved sufficiently to prevent an inadvertent disconnect.
!! IMPORTANT: In order to preserve the electromagnetic immunity levels
necessary for CE compliance the following must be strictly observed:
1.
Power must be supplied via no smaller than 24 AWG (0.25 mm
2
) twisted, shielded copper wire.
2.
Relay contacts must be connected to their load via a twisted, shielded cable of appropriate wire
gauge for the load. A minimum of 20 AWG copper wire (0.7 mm
2
) is recommended.
3.
Both shields (power and relay wires) shall be terminated on the ground terminal of the flow switch
while leaving the opposite ends un-terminated.
4.
Maximum rated load for the relay contacts is 5 amps resistive at no more than 30 Vdc.
5.
Wiring shall be enclosed in a properly grounded, armored metallic sheath.
6.
Additionally, for TU style instruments, earth ground the flow tube, using the tube ground
connection. Grounding is important for EMC immunity.