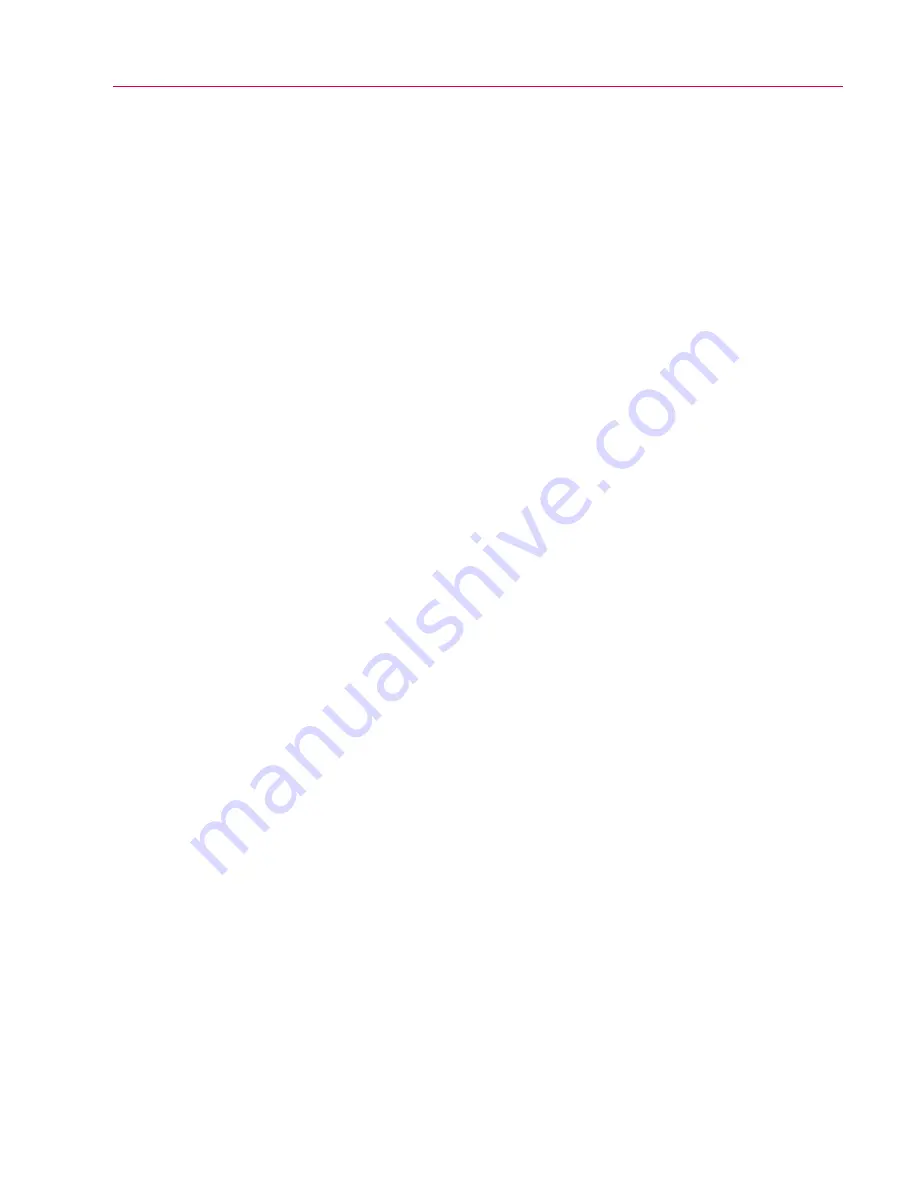
23
Frame
Product Support:
1. J1 = Manually adjustable crosshead with manual crosshead locks
J3 = Hydraulically adjustable crosshead with hydraulic crosshead locks
J4 = Fixed crosshead
A = Basic test opening
B = Increase vertical test space by 305 mm (12 in)
C = Increase vertical test space by 610 mm (24 in)
D = Increase vertical test space by 915 mm (36 in)
2. Long term static tests should be limited to 30 minutes or less when the test is performed at or near maximum capacity. Time
varies inversely with test load. 50% maximum capacity tests should be limited to 60 minutes or less. An oil temperature
switch limits test duration based on safe reservoir temperature. Assumes ambient temperature of 25 deg C (77 deg F).
3. The design capacity is the peak load at which the frame should be used for no more than 80% of the time. In other words, at
least 80% of specimen testing should be conducted at peak loads that are at or below the design capacity. The frame should
only be used at loads between the design capacity and the maximum capacity less than 20% of the time.
4. The minimum and maximum test opening is provided for each lift cylinder range. Minimum opening is with the hydraulic
cylinder fully extended. Maximum opening is with the hydraulic cylinder fully retracted. Values do not include specimen
fixtures.
5. Measured from floor to top of columns.
6. The General Assembly drawing is located in the separately supplied “Reference Manual-Equipment”. General Assembly
drawings are model specific; please be sure to refer to the appropriate drawing for your model and its configuration.
7. Weight does not include grips, fixtures, HPS, or control equipment.
8. C3 = Hydraulic cylinder position/Speed measurement (high resolution)
C4 = Hydraulic cylinder position/Speed measurement (ultra high resolution)
9. Under no load conditions. Accuracy is affected under load. The encoder cannot compensate for frame deflection (axial
stiffness) or the load cell and load string deflections. Over short travels and higher loads, the error could be over 100%.
Conversely, over longer travels and lower loads, the error may be insignificant. The axial frame stiffness and load cell stiffness
values published may be used to assess this affect. The load string also needs to be considered. In general, the extension
(position) readout should not be used as the primary strain measuring device where an extensometer on the specimen is
clearly warranted. Frame compliance can be accounted for, to some extent, by Instron software.
10.At speeds below approximately 0.1 mm/min (0.004 in/min) the hydraulic cylinder moves in increments approximately equal to
these values and can be seen as load steps depending on the specimen stiffness and load range.
11.For all frames: Parallelism and alignment are checked with the crosshead in the lowest possible position.
For frames with a J4-style crosshead: The fixed position of the crosshead places the hydraulic cylinder at a relatively large
distance from the base. This makes parallelism and alignment difficult to verify. Therefore, the value listed should be
considered theoretical.
12.Between frame base and face of load cell or bottom of actuator and face of load cell, depending on frame model (mounting
arrangement of load cell).