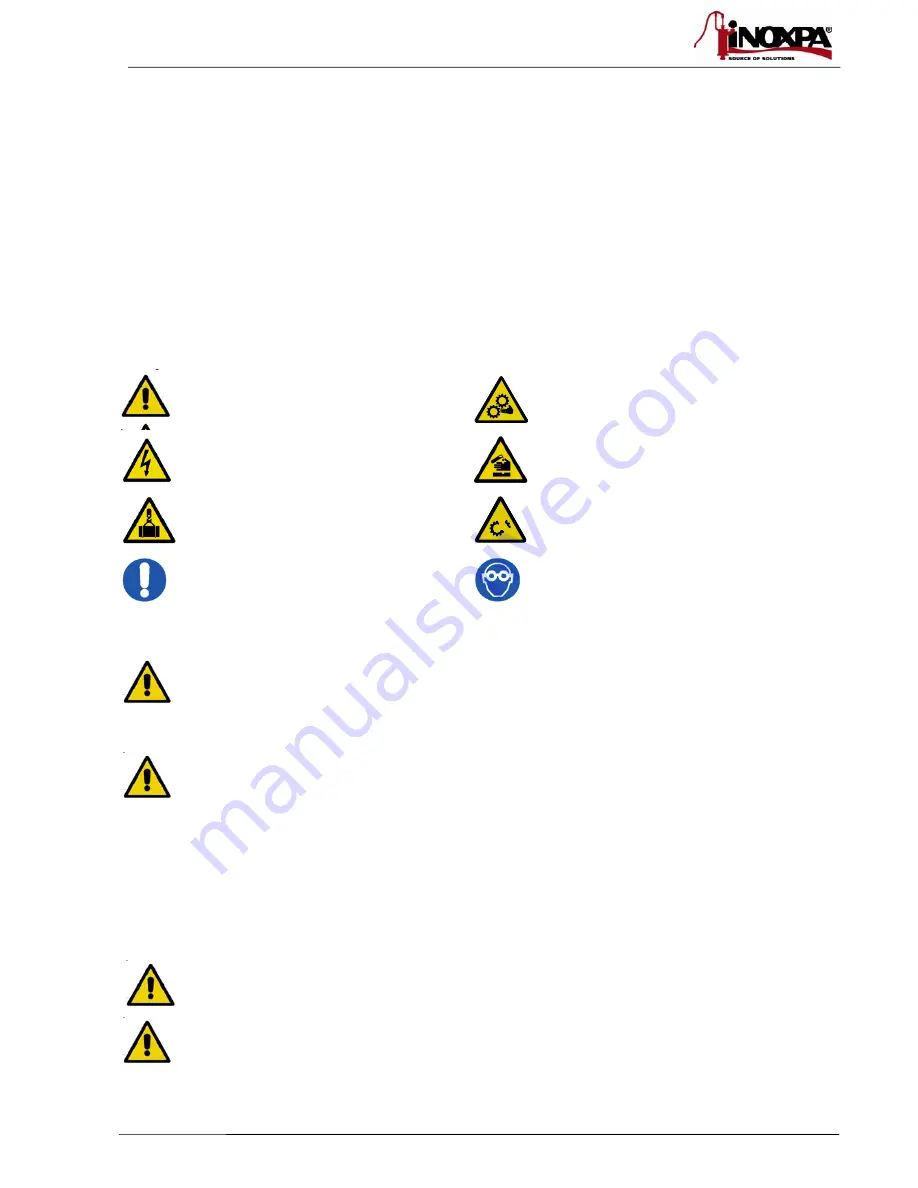
ED. 2009/09 /
3
1.
Safety
1.1.
INSTRUCTION MANUAL
This manual contains basic instructions which should be fulfilled during the installation, starting and maintenance.
The contents published in the instruction manual is based on updated information.
INOXPA reserves the right to modify this instruction manual without prior notice.
1.2.
START-UP INSTRUCTIONS
This instruction manual contains vital and useful information to correctly handle and maintain your valve.
Not only should the safety instructions indicated in this chapter be observed and fulfilled, but so should the special measures
and recommendations included in the other chapters of this manual. These instructions should be kept in a safe location near
the installation.
1.3.
SAFETY
1.3.1.
Warning symbols.
Danger for persons in general
Danger of injury caused by rotating
equipment parts.
Electrical danger
Danger! Caustic or corrosive agents.
Danger! Suspended loads
Danger to the correct operation of the
equipment.
Commitment to safety at the workplace.
Protective goggles requirement.
1.4.
GENERAL SAFETY INSTRUCTIONS
Read the instruction manual carefully before installing and starting up the valve. Contact INOXPA in
case of doubt.
1.4.1.
During the installation.
The
Technical Specifications
of Chapter 8 should always be observed.
The installation and use of the valve should always be carried out in accordance with applicable
regulations regarding health and safety.
Before starting up the valve, confirm that the assembly is correct and that the shaft is perfectly
aligned. Incorrect alignment and/or excessive force in securing the valve may cause serious
mechanical problems in the valve. Check that the diaphragm has been correctly assembled, as
incorrect assembly may cause serious damage to the valve.
1.4.2.
During operation.
The
Technical Specifications
of Chapter 8 should always be observed. Never exceed the specified limits.
NEVER touch the valve and/or pipes that are in contact with the liquid during operation. If working
with hot fluids, there is a risk of burns.
Summary of Contents for PHARMAVALVE
Page 18: ...18 ED 2009 09 8 1 VALVE DIMENSIONS 10 310 32 0010...
Page 22: ...NOTES...
Page 23: ...NOT TES...