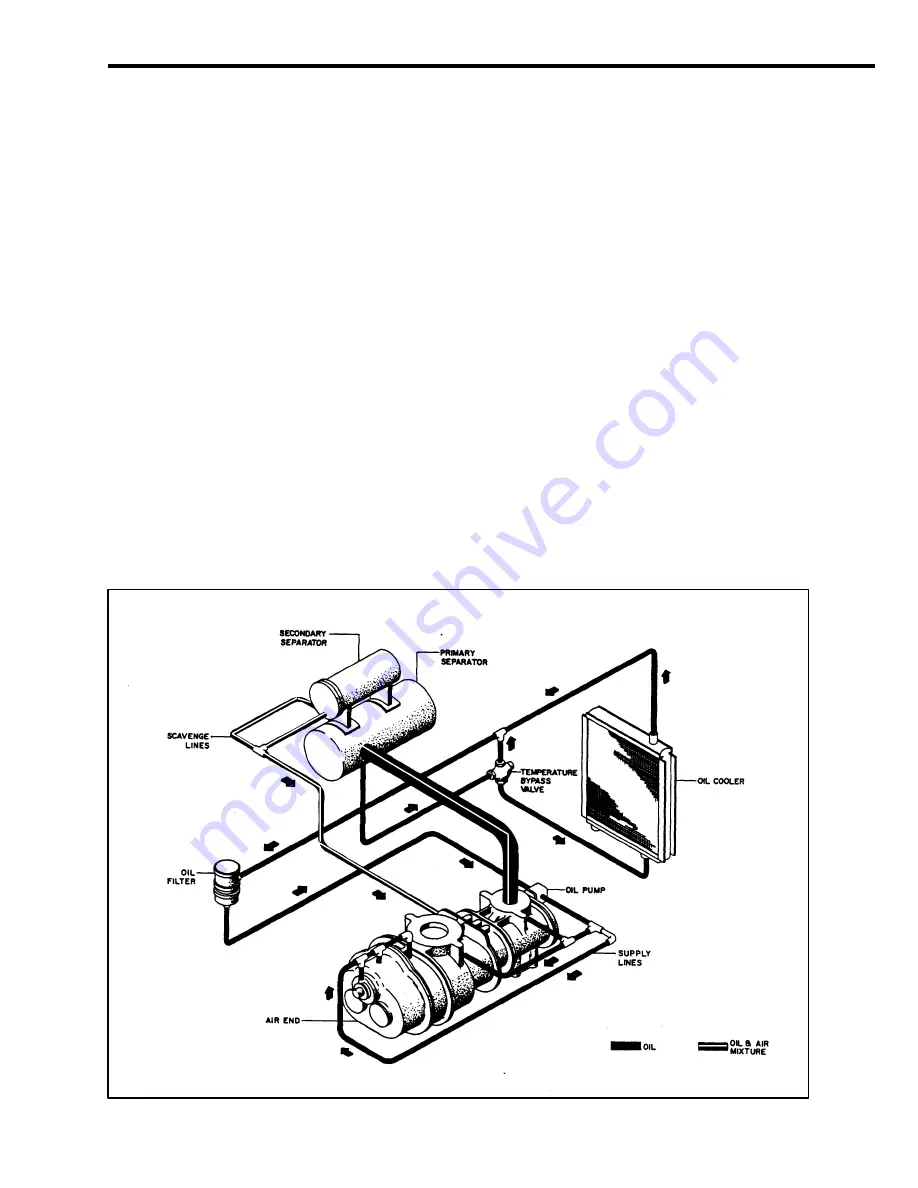
Manual - vhp300cm
- 34
06/20/00
LUBRICATION
Both compressor lubrication and cooling are
accomplished by the compressor lubricating oil.
The oil is forced from the oil storage reservoir,
under system pressure, through an oil cooler and
an oil filter directly to the compressor. When the
compressor is operating at low capacity, some of
the oil may bypass the cooler through a
thermostatically controlled bypass valve. This
valve bypasses varying amounts of oil,
depending upon the temperature, until the oil
being circulated reaches a temperature of 185
°
F
(85
°
C) thus maintaining a higher average oil
temperature thereby reducing the possibility of
water vapor condensation in the oil.
Typical Lubricating and Cooling Oil System
Relatively cool lubricating oil is admitted under
pressure to the compressor bearings and is also
injected in metered amounts, directly to the rotor
chamber. All of the oil thus introduced mixes
with, and passes on with the air being
compressed, thus removing the heat of
compression to a large degree. On its way to the
final discharge connection, the air passes through
a receiver/separator. A scavenger line returns
any remaining separated oil back to the inlet of
the compressor.
Fill the oil storage reservoir in the
receiver/separator with new oil before operating
the unit. Recharge the compressor by first
removing the air filter and pouring about two
gallons (7.57 liters) of oil into the compressor
inlet.
NOTE
Recharging of the compressor with oil is
absolutely necessary on units that have been
placed in extended storage (6 months or more).
Summary of Contents for VHP300CM
Page 9: ...Manual vhp300cm 9 06 20 00 SAFETY CARD...
Page 15: ...Manual vhp300cm 15 06 20 00 fold...
Page 46: ...Manual vhp300cm 46 06 20 2000...
Page 57: ...Manual vhp300cm 56 06 20 2000 SECTION 11 COMMON FASTENERS...
Page 58: ...Manual vhp300cm 57 06 20 2000...
Page 59: ...Manual vhp300cm 58 06 20 2000...
Page 60: ...Manual vhp300cm 59 11 17 99 37...