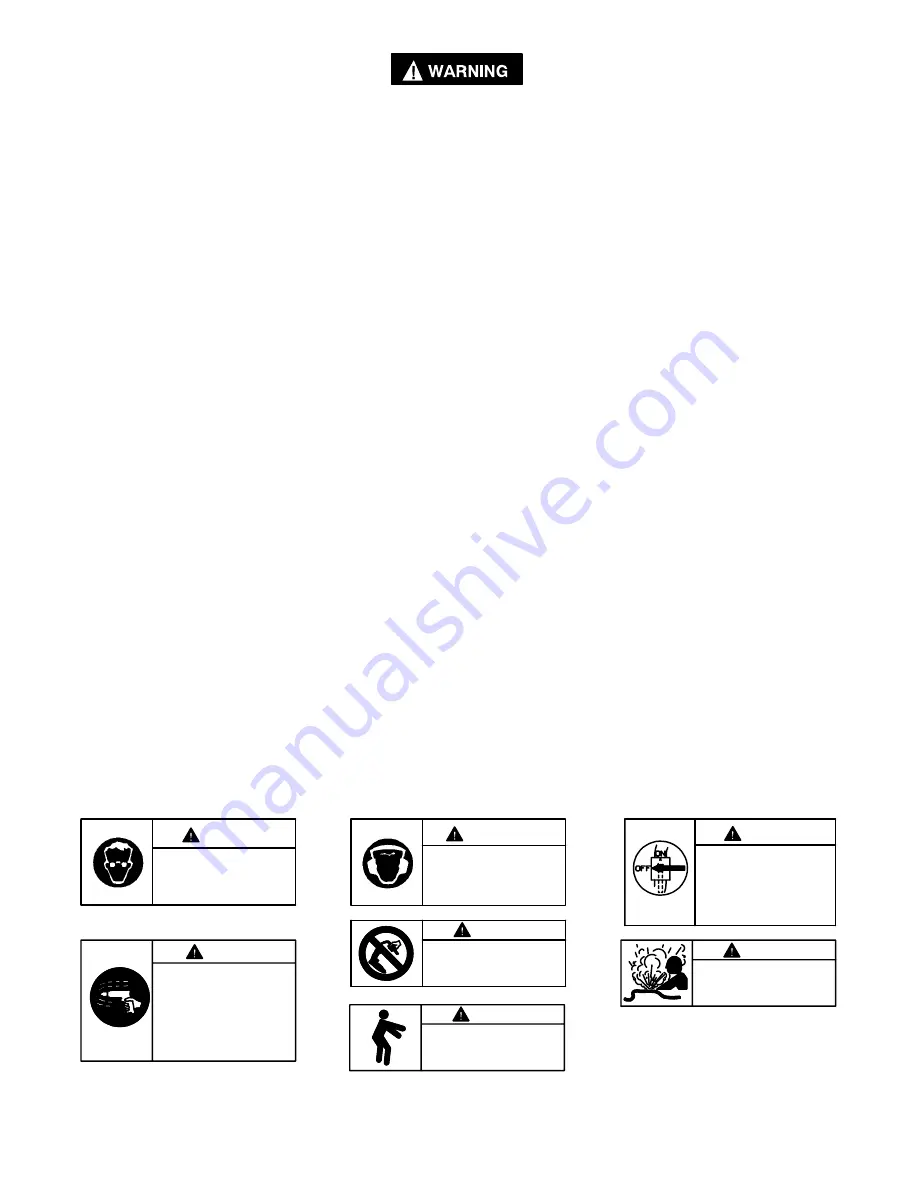
2
FAILURE TO OBSERVE THE FOLLOWING WARNINGS COULD RESULT IN INJURY.
USING THE TOOL
(Continued)
•
Secure work. Use clamps or a vise to hold work.
Operators often need both hands to perform job
functions.
•
Don’t overreach. Keep proper footing, balance, and a
firm grip on the tool at all times.
•
Maintain tools with care. Keep tools clean for better
and safer performance. Follow instructions for
lubricating and changing accessories. Inspect tool
cords periodically and if damaged, have them repaired
by an authorized service facility. Inspect extension
cords periodically and replace if damaged. Keep
handles dry, clean, and free from oil and grease.
•
Remove adjusting keys and wrenches. Form habit of
checking to see that keys and adjusting wrenches are
removed from tool before turning it on.
•
Avoid unintentional starting. Don’t carry tool with
finger on switch.
•
Do not drop or abuse the tool.
•
Whenever a tool is not being used, position the
Power Switch to the “OFF” position and unplug the
power cord.
•
Stay alert. Watch what you are doing. Use common
sense. Do not operate tool when you are tired.
•
Check damaged parts. Before further use of the tool,
a guard or other part that is damaged should be
carefully checked to determine that it will operate
properly and perform its intended function. Check for
alignment of moving parts, binding of moving parts,
breakage of parts, mounting, and any other conditions
that may affect its operation. A guard or other part that
is damaged should be properly repaired or replaced by
an authorized service center unless otherwise indicated
elsewhere in this operation manual.
•
Have defective switches replaced by an authorized
service center.
•
Do not use the tool if the switch does not turn it on
and off.
•
Do not drop or abuse the screwdriver.
•
Whenever changing a bit, make certain the
Forward/Reverse Switch is in the “OFF” position
and the tool is unplugged.
•
Do not allow chemicals such as acetone, benzene,
thinner, ketone, trichloroethylene or other similar
chemicals to come in contact with the screwdriver
housing as damage will result.
•
Do not adjust the torque setting higher than 5 on
the Torque Scale.
Duty cycle:
MAX 0.8 sec. “ON”
MIN 3.2 sec. “OFF”
•
Do not tighten more than 900 tapping screws
(size: 2 mm, length: 4 mm) per hour.
•
Do not operate the Forward/Reverse Switch when
the motor is running.
•
Whenever a tool is not being used, move the
Forward/Reverse Switch to the “OFF” position and
unplug the screwdriver.
•
The use of any accessory or attachment other than
recommended in this manual can present a risk of
personal injury.
WARNING LABEL IDENTIFICATION
Always wear eye protection
when operating or perform-
ing maintenance on this
tool.
WARNING
WARNING
Always wear hearing
protection when operating
this tool.
Always turn off the electrical
supply and disconnect the
power cord before installing,
removing or adjusting any
accessory on this tool, or
before performing any
maintenance on this tool.
WARNING
Powered tools can vibrate in
use. Vibration, repetitive mo-
tions or uncomfortable posi-
tions may be harmful to your
hands and arms. Stop using
any tool if discomfort, tingling
feeling or pain occurs. Seek
medical advice before resum-
ing use.
WARNING
Do not carry the tool by
the cord.
WARNING
WARNING
Do not use damaged, frayed
or deteriorated power cords.
WARNING
Keep body stance balanced
and firm. Do not overreach
when operating this tool.