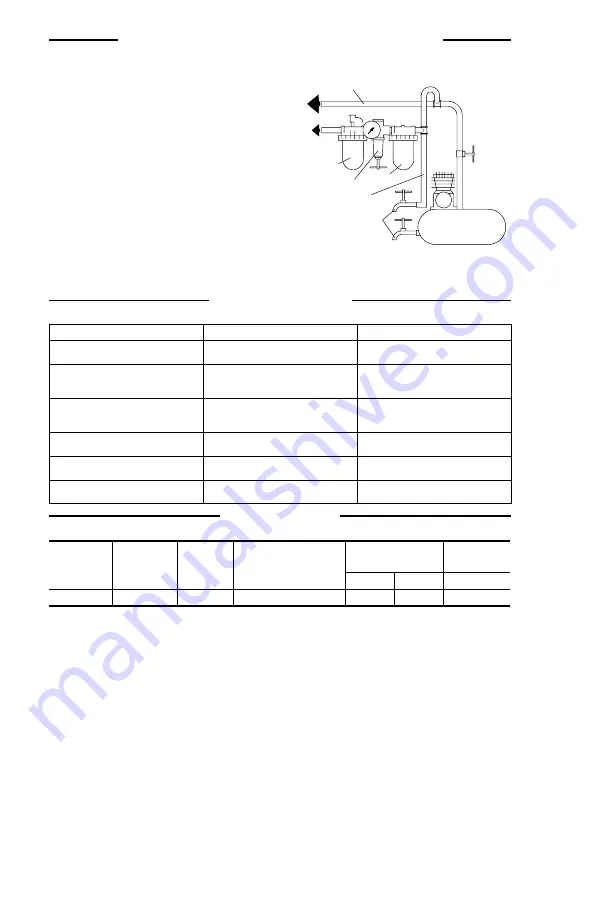
3
OPERATIONS AND MAINTENANCE INSTRUCTIONS
•
90psig maximum at tool inlet.
•
Lubrication -- Inject approximately 0.5 cc of
Powerforce No. 50Oil into the air inlet before
starting the tool and after each two or three hours
of operation, unless the air line lubricator is used.
Lubricate with 0.5 cc of Powerforce No. 50 Oil
before storage.
•
Speed Adjustment -- Rotate regulator (5) to adjust
from no rotaion to maximum speed.
•
To mount stones and other accessories, use the
wrenches supplied with the tool. Always disconnect
air supply before changing any accessories. Hold
collet (13) with one wrench (15), while using the
other wrench (15) to turn collet nut (14). Fully
insert mandrel into chuck and tighten until secured
in collet.
•
Wear gloves and protective clothing while
operating this tool.
•
Daily, before use, without accessories, check
spindle speed. Tighten spindle attachments
securely.
MAIN LINES 3 TIMES
AIR TOOL INLET SIZE
TO
AIR
SYSTEM
TO
AIR
TOOL
LUBRICATOR
REGULATOR FILTER
BRANCH LINE 2 TIMES
AIR TOOL INLET SIZE
DRAIN REGULARLY
COMPRESSOR
(Dwg. TPD905--1)
TROUBLESHOOTING
Problem
Possible Cause
Action
Low speed or tool will not function Lack of lubrication
Add 0.5 cc of Powerforce oil #50 to
the tool
Low speed or tool will not function Low pressure
Ensure system regulators are set
properly to have 90 psi (6.2 bar/
620 kPa) at the tool inlet.
Low speed or tool will not function Low pressure
Ensure proper hose size. Long
hose lengths may require a hose
with a 1/2” ID or larger
Low speed or tool will not function System leakage
Ensure connections are tight and
hoses are not damaged
Low speed or tool will not function Debris build up in tool
Flush tool with 0.5 cc of
Powerforce oil #50
Low speed or tool will not function Regulator (5) in wrong position
Ensure that the regulator is in the
proper position
SPECIFICATIONS
Model
Type of
Handle
Collet
Size
Free Spreed
rpm
H Sound Level
dB (A)
z
Vibrations
Level
Model
Handle
Size
rpm
Pressure
Power
m/s
2
PF400
Lever
1/4”
27000
86
99
4.9
H Tested in accordance with PNEUROP PN8NTC1.2
z Tested to ISO8662