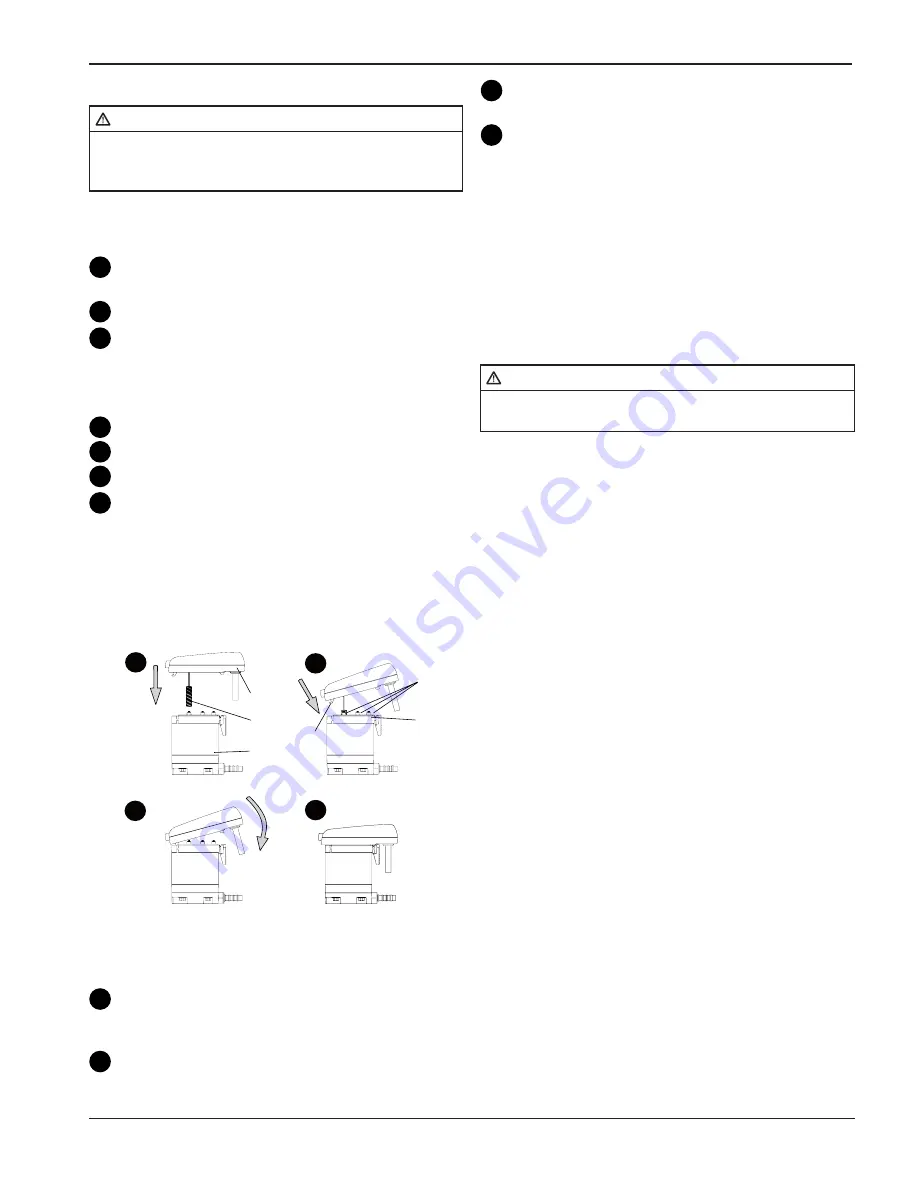
ingersollrandproducts.com
13
9.0 SCHEDULED MaINTENaNCE
9.3.2 NO AIR LOSS DRAIN (OPTIONAL)
WaRNINg
Before drain maintenance work, always close the
drain isolation ball valves and ensure that the
device is pressureless and de-energized.
Maintenance recommendations
Replace service unit (5) annually.
1
Remove control unit (1) by pressing latching
hook (2).
2
Detach Drain from outlet (3).
3
Remove design shell (4) (where applicable) using
a screw driver (10).
Remove service unit (5) from pipe at inlet by
undoing union nut
4
or by undoing screws (6) at elbow connector (7)
5
or
6
by undoing screws (8) at intermediate adapter (9)
7
which is then detached from the service unit by
downward movement.
Check if new service unit (5) matches control unit (1)
- type designation and colour of latching hook (2)
Fit new service unit (5) in reverse order
Open drain isolation ball valve. Press drain test
button to verify proper drain operation.
2
5
4
3
2
1
6
4
3
1
assembly Control unit onto service unit:
Check if service unit (3) matches control unit (1) (type
designation and colour of latching hook)
1
Check if sensor tube plate (5) with contact
springs (4) is clean, dry and free from foreign
matter.
2
Insert sensor (2) into sensor tube plate (5).
•
•
•
3
Fit latching hook (6) of control unit (1) into
sensor tube plate (5).
4
Press control unit (1) against service unit (3) and
snap into place
Open drain isolation ball valve. Press drain test
button to verify proper drain operation.
9.4 PaNEL FILTER ELEMENT
Annual replacement of the panel filter element is
recommended. To replace the panel filter element, remove
the panel filter by pulling up and out of its slots, then fit the
new element in.
9.5 PRE-FILTERS aND POST-FILTERS
WaRNINg
Depressurize the system before disassembling
filters. Failure to do so may result in injury or death.
Filter elements should be changed as indicated on the
pressure differential gauge. Change carbon elements when
hydrocarbons are first detected downstream or every six
months, whichever comes first.
Certain filters contain multiple elements. When replacing
filter elements, all elements should be replaced
simultaneously. Mixing new and old elements can result in
reduced air quality.
•