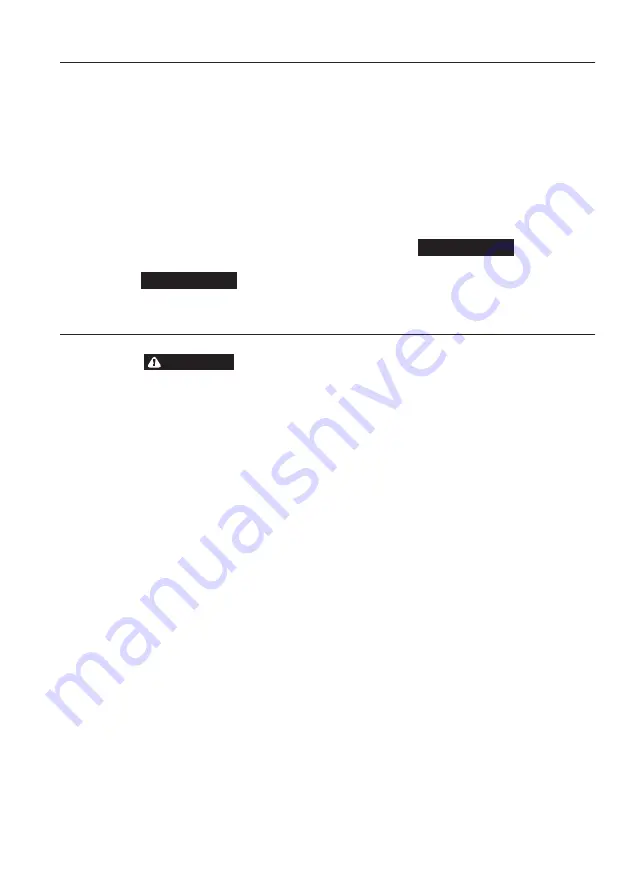
45586039_ed1
5
Maintenance
Gas Operation Test Procedure
Ingersoll Rand
carefully assembled this motor with specially
selected sealing materials to prevent gas leakage, and tested this
motor to detect leaks.
When reassembling a motor, follow the procedures to properly test
the motor for leaks:
1. Plug one inlet (either forward or reverse).
2. Connect non-pressurized air line to the inlet that is not plugged.
3. Pressurize motor with air to 40 psi.
4. Fully submerge motor in water.
5. Monitor for a minimum of 2 minutes for bubbles in water.
6A. If the motor DOES NOT release bubbles during the two minute
test, the motor is ready for gas operation.
6B. If the motor releases ANY bubbles during testing, the motor must
be reworked and retested.
NOTICE
If the motor operates sluggishly, flush it with a clean,non-toxic,
nonflammable commercial solvent in a well ventilated area.
To flush the motor:
1. Disconnect the air line and muffler.
2. Pour 6 to 8 cc of solvent into each inlet.
3. Rotate the rotor shaft by hand in both directions several times to
ensure all internal parts of motor are thoroughly cleaned.
4. Apply air pressure to the inlet and slowly increase the air flow
until there is no trace of the solvent in the exhaust.
5. After flushing, shut off the air supply and disconnect air supply
line.
6. Pour 6 to 8 cc of a high detergent SAE 10 motor oil into the air
inlet.
7. Reconnect the air supply line, slowly increase the air pressure to
ensure all internal parts of motor will be covered with a film of oil.
8. If the motor is still low in power, check for damaged vanes or
foreign material in the vane slots in the Rotor.
NOTICE
Periodically, check the Vanes for wear. Always replace Vanes in
sets, never replace an individual Vane.
Assembly / Disassembly Instructions
WARNING
Always wear eye protection when operating or performing
maintenance on this motor.
Always turn off air / gas supply and disconnect supply hose
before installing, removing or adjusting any accessory on this
motor, or before performing any maintenance on this motor.
Disassembly
General Instructions
1. Always disconnect the air / gas line at the motor before
attempting any disassembly.
2. Do not disassemble the motor any further than necessary to
replace or repair damaged parts.
3. When grasping a pan in a vise, always use leather-covered or
copper-covered vise jaws to protect the surface of the part and
help prevent distortion. This is particularly true of threaded
members and housings.
4. Do not remove any part which is a press fit in or on a
subassembly unless the removal of that part is necessary for
repairs or replacement.
5. If it necessary to disassemble a motor, always have new seals on
hand. Do not use old seals.
Assmbly
General Instructions
1. Always wipe all parts with a thin film of oil before installing them
in the motor.
2. Always press on the inner ring of a ball-type bearing when
installing the bearing on a shaft.
3. Always press on the outer ring of a ball-type bearing when
pressing the bearing into a bearing recess.
4. Whenever grasping a part in a vise, always use leather-covered
or copper-covered vise jaws to protect the surface of the part
and help prevent distortion. This is particularly true of threaded
members and housings.
5. Lubricate the Rotor (3) and Vanes (4) with a good quality SAE 10
non-detergent oil. Lubricate the Bearings with Ingersoll-Rand No.
28 Grease. Coat the Rotor Shaft (6) with a good quality SAE 10
non-detergent oil.
6. If using gas to power the motor always test for leaks after
assembly. Refer to the Gas Operartion Test Procedure.
Summary of Contents for MVA017B/VSM-5842
Page 7: ...Notes...