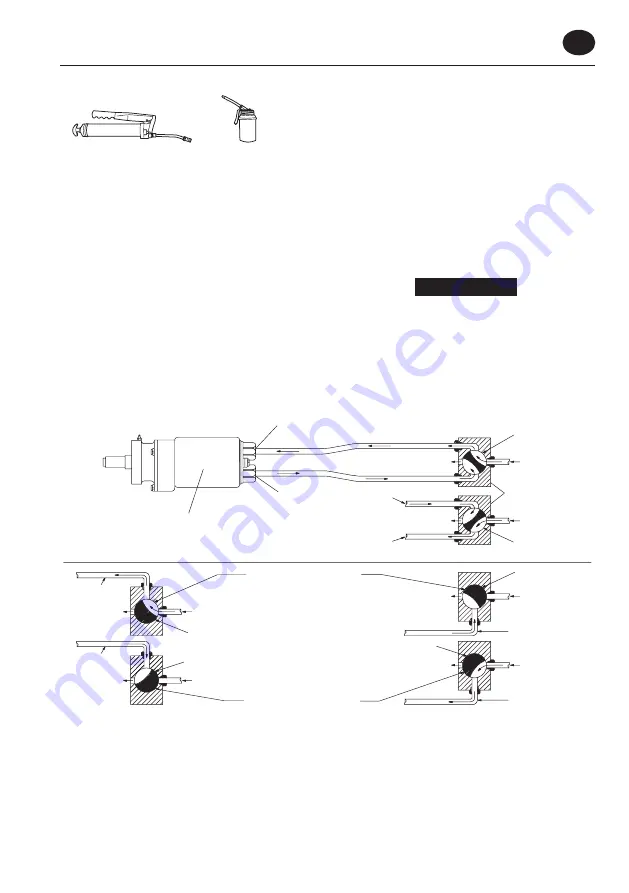
03523479_ed16
3
EN
Placing Tool in Service
Lubrication
Ingersoll Rand No. 28 Ingersoll Rand No. 50
Always use an air line lubricator with this motor.
We recommend the following Filter-Lubricator-Regulator Unit:
No. C28241-800
Where the lubricator cannot be permanently mounted, use
Ingersoll Rand No. 3LUB8 Lubricator.
We recommend the use of an air line lubricator in the air supply
line. Attach the unit as close to the tool as practical. For permanent
installations, we recommend using an Ingersoll Rand
C28241-800 Filter-Lubricator-Regulator Unit. These units have 1/2”
pipe tap inlet and outlet. The 3LUB8 has 1/6 pt (79 ml) capacity; the
C28241-800 has 6 oz (177 ml) capacity. Larger capacity units may be
used, but do not use a unit having less than 1/2” pipe tap inlet and
outlet.
After each 40,000 cycles or one month, whichever occurs first,
inject 1.5 cc of Ingersoll Rand No. 28 Grease into the Grease
Fitting (30).
Direction of Spindle Rotation
Series 3800 Nonreversible Motors can be assembled so that the
Spindle rotates either clockwise or counter-clockwise. To reverse the
direction of the spindle rotation:
1. Remove the motor assembly from the Motor Housing (15).
2. Remove one End Plate and Bearing from the motor.
3. Lift the Cylinder (16) from the Rotor (13), turn it end for end, and
slide it back over the Rotor.
4. Install the End Plate and Bearing assembly on the Rotor Hub and
install the assembled motor in the Housing.
5. Remove the three Backhead Cap Screws (3) and rotate the
Backhead (2) and Backhead Gasket (6) 90° so that the cavity in
the face of the Backhead is in alignment with the alternate set of
holes in the back face of the Motor Housing. When the Backhead
is correctly applied, the cavity will be over the letter “F” for
counterclockwise spindle rotation (when facing the end of the
Spindle), and over the letter “R” for clockwise rotation.
The rotational direction of an assembled Nonreversible Series
3800 Motor can be determined by removing the Air Strainer (1)
and looking through the tapped opening to see whether the
letter “F” or letter “R” is visible. Apply the Backhead on Series
3840 Reversible Motors so that each inlet port aligns with a group
of three holes through the housing rear wall.
NOTICE
A four-way Throttle Valve (whether manually, remotely, or
automatically controlled) must be used in the air supply
line to Series 3840 reversible motors, as one motor inlet is
expelling secondary exhaust air, and therefore must be open to
atmosphere whenever the opposite inlet is admitting live air to
the motor. The use of any throttle valve that closes or restricts
the secondary exhaust line will result in sufficient back pressure
to drastically reduce the speed and power of the motor.
When the application requires a separate Throttle Valve in each
air line, the two three-way valves must be used.
Forward Inlet
Reverse Inlet
Reversible Motor
Exhaust
Exhaust
Air line to
forward inlet
Air line to
reverse inlet
Valve positioned for
forward operation
of Motor
Valve positioned for
reverse operation
of Motor
Valve positioned for
forward operation
of Motor
Valve positioned for reverse
operation of Motor
Valve positioned for
reverse operation
of Motor
Valve positioned for
forward operation
of Motor
Air line to
forward inlet
Air line to
forward inlet
Air line to
reverse inlet
Air line to
reverse inlet
Live Air
Live Air
Live Air
Live Air
Exhaust
Exhaust
Exhaust
Exhaust
Live Air
Live Air
Four-way
Throttle
Valve
Single four-way Valves for controlling forward and reverse operation of Motor
Two three-way Valves for controlling forward and reverse operation of Motor
Relative positions of Valves for
forward operation of Motor
Relative positions of Valves for
reverse operation of Motor
Three-way Throttle
Valve in air line to
reverse inlet
Three-way Throttle
Valve in air line to
forward inlet
(Dwg. TPB176)
Summary of Contents for MULTI-VANE 3800 Series
Page 11: ...Notes...