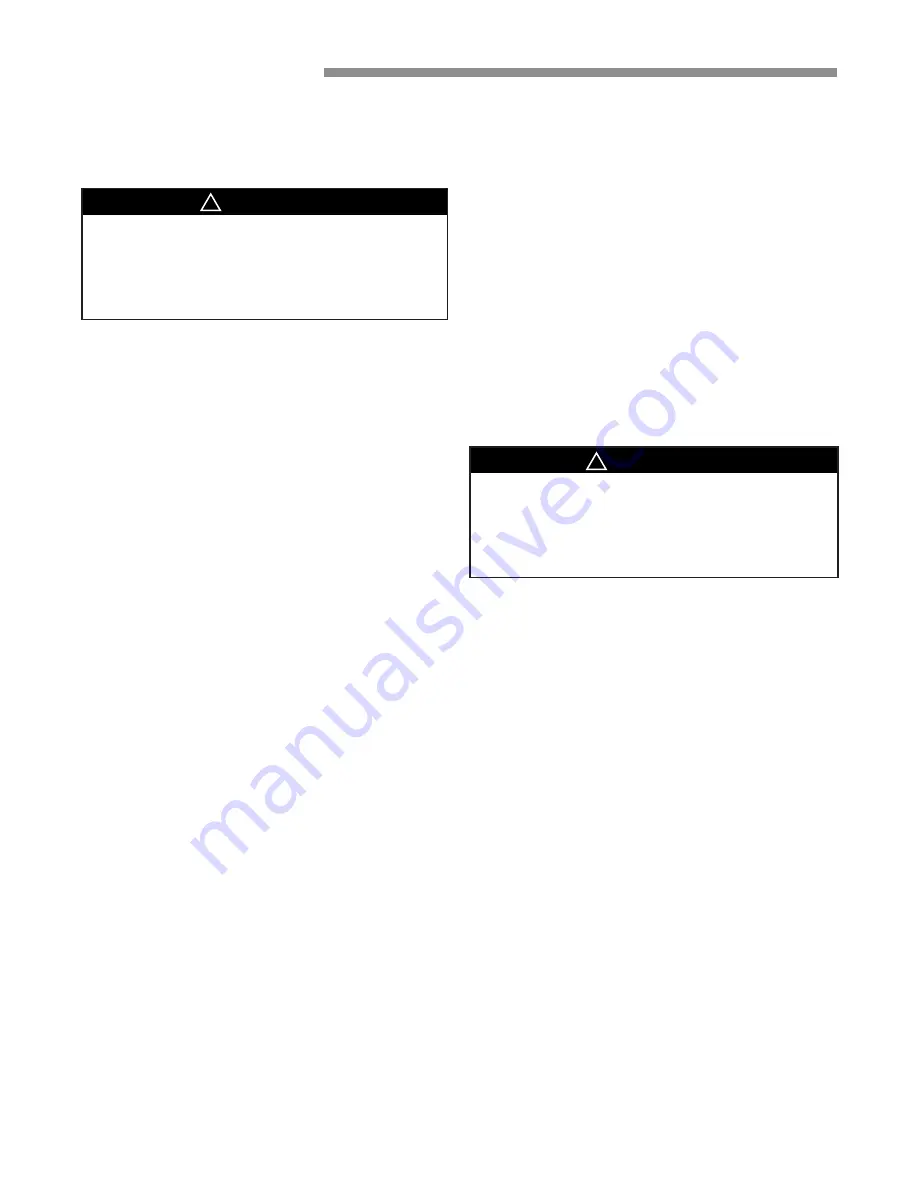
34 18-CD35D1-1
INSTALLER’S GUIDE
When the furnace reaches the maximum outlet temperature as
shown on the rating plate, the burners must shut off. If they do
not shut off after a reasonable time and overheating is evident,
a faulty limit switch is probable and the limit switch must be
replaced. After checking the operation of the limit control, be
sure to remove the paper or cardboard from the return air inlet.
Refer to Service Facts for additional instructions.
NOTE TO INSTALLER
Review the following warnings with the owner. Review contents
of USER’S INFORMATION MANUAL with the owner.
AIRFLOW ADJUSTMENT
Check inlet and outlet air temperatures to make sure they are
within the ranges specified on the furnace rating nameplate. If
the airflow needs to be increased or decreased, see the wiring
diagram for information on changing the speed of the blower
motor.
▲
WARNING
!
ELECTRICAL SHOCK HAZARD
Disconnect power to the unit before removing the
blower door. Failure to follow this warning could
result in property damage, personal injury or
death.
This unit is equipped with a blower door switch which cuts power
to the blower and gas valve causing shutdown when the door is
removed. Operation with the door removed or ajar can permit the
escape of dangerous fumes. All panels must be securely closed at
all times for safe operation of the furnace.
INDOOR BLOWER TIMING
Heating
: The integrated furnace control module controls the
indoor blower. The blower start is fixed at 45 seconds after
ignition (10 seconds for downflow models). The FAN-OFF
period is field selectable by dip switches at 60, 100, 140, or 180
seconds. The factory setting is 100 seconds (See wiring diagram).
Cooling
: The fan delay off period is factory set at 0 seconds.
The option for 80 second delay off is field selectable (See wiring
diagram).
ROOM AIR THERMOSTAT
HEAT ANTICIPATOR ADJUSTMENT
Set the thermostat heat anticipator according to the current flow
measured, or the settings found in the notes on the furnace wiring
diagram (found in the SERVICE FACTS or inside the furnace
casing).
To shut off.
For complete shut-down: Flip the switch on the main gas valve
to the “OFF” position, (See Figure 57 and 58). Disconnect the
electrical supply to the unit.
▲
CAUTION
!
If this is done during the cold weather months,
provisions must be taken to prevent freeze-up
of all water pipes and water receptacles. Failure
to follow this warning could result in property
damage.
Whenever your house is to be vacant, arrange to have
someone inspect your house for proper temperature. This
is very important during freezing weather. If for any reason
your furnace should fail to operate damage could result, such
as frozen water pipes.
SEQUENCE OF OPERATION
Thermostat call for heat
R and W thermostat contacts close signaling the control module
to run its self-check routine. After the control module has verified
that the pressure switch contacts are open and the limit switch(es)
contacts are closed, the draft blower will be energized.
As the induced draft blower comes up to speed, the pressure
switch contacts will close and the ignitor warm up period will
begin. The ignitor will heat for approximately 20 seconds, then
the gas valve is energized to permit gas flow to the burners. The
flame sensor confirms that ignition has been achieved.
After the flame sensor confirms within a 4 second trial period that
ignition has been achieved, the delay to fan ON period begins
timing. After approximately 45 seconds the indoor blower motor
will be energized and continue to run during the heating cycle
(downflow models have a 10 second blower ON delay).
When the thermostat is satisfied, R and W thermostat contacts
open, the gas valve will close, the flames will extinguish, and the
induced draft blower will be de-energized. The indoor blower
motor will continue to run for the fan off period (Field selectable
at 60, 100, 140 or 180 seconds), then be de-energized by the
control module.
CONTROL AND SAFETY SWITCH
ADJUSTMENTS
LIMIT SWITCH CHECK OUT
The limit switch is a safety device designed to close the gas valve
should the furnace become overheated. Since proper operation
of this switch is important to the safety of the unit, it
must be
checked out on initial start up by the installer.
To check for proper operation of the limit switches, set the
thermostat to a temperature higher than the indicated temperature
to bring on the gas valve. Restrict airflow by blocking the return
air (disconnecting the indoor blower may trip the inducer limit).