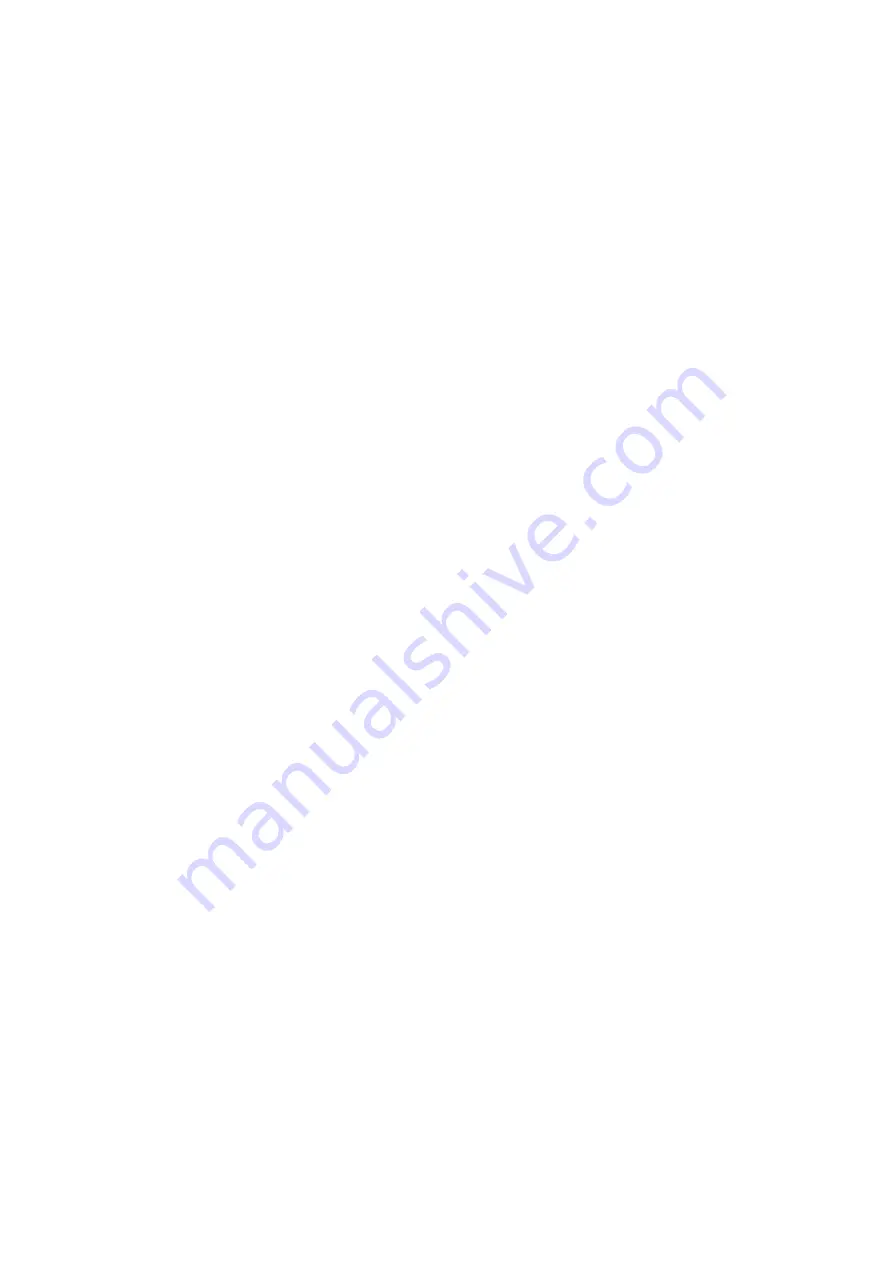
7
Shut-off Valve Disassembly
(Ref. Dwg.D6170004)
1.
Remove the screw (202).
2.
Remove the cover (201) with the spring (203).
3.
Remove the ‘O’ ring (204) from the cover (201).
4.
Remove the cover (213) and the ‘O’ ring (215).
5.
Remove the diaphragm (211).
6.
Immobilise the valve cone (214) by its hole with a rod
in one of two orifices of the body (209) and remove
the screw (208).
7.
Remove the valve cone (205,214) with joints (206)
and distance ring (210) with the washer (207).
Emergency Stop Valve Disassembly
(Ref. Dwg.D6170003)
Refer to air control valve disassembly to begin disassembly
8.
Remove emergency stop button (179).
9.
Remove the setscrews (175).
10.
Remove the spools (178).
11.
Pull on the shuttle valve stop (180) with ball ( 176).
12.
Remove the ‘O’ ring (181) from shuttle valve stop
(180) and spool (176).
Cleaning, Inspection and Repair
Use the following procedures to clean, inspect, and repair
the components of the winch.
•
A bearing that appears loose or does not rotate
smoothly must be replaced. Failure to observe this
precaution will result in bearing and/or winch
component damage.
Clean all winch component parts in solvent (except for the
brake friction disc). The use of a stiff bristle brush will
facilitate the removal of accumulated dirt and sediments in
the drum and reduction assembly. If drum bushings have
been removed it may be necessary to carefully scrape old
Loctite® from the drum bushing bore. Dry each part using
low pressure, filtered compressed air. Clean the brake
friction disc using a wire brush or emery cloth. Do not wash
the brake friction disc in liquid. If the brake friction discs
are oil soaked, they must be replaced.
Inspection
All disassembled parts should be inspected to determine
their fitness for continued use. Pay particular attention to
the following:
1.
Inspect all gears for worn, cracked, or broken teeth.
2.
Inspect all bushings for wear, scoring or galling.
3.
Inspect all bearings for play, distorted races, pitting
and roller or ball wear or damage. Inspect bearings
for freedom of freedom
4.
Inspect shafts for ridges caused by wear. If ridges
caused by wear are apparent on shafts, replace the
shaft. Inspect all surfaces on which oil seal lips seat.
These surfaces must be very smooth to prevent
damage to the seal lip.
5.
Inspect all threaded items and replace those having
damaged threads.
6.
Inspect all remaining parts for evidence of damage.
Replace or repair any part which is in questionable
condition. The cost of the part is often minor in
comparison with the cost of redoing the job.
7.
Smooth out all nicks, burrs, or galled spots on shafts,
bores, pins or bushings.Examine all gear teeth
carefully, and remove nicks or burrs.
8.
Polish the edges of all shaft shoulders to remove
small nicks which may have been caused during
handling.
9.
Remove all nicks and burrs caused by lockwashers.
10.
Replace all gaskets, oil seals, and O’rings any time
the winch is disassembled for repair.
11.
Inspect drum bushings (47) for wear, if thickness is
less than 0.039 in. (1 mm), replace drum bushings.
12.
Inspect brake discs (21 and 22) for wear, if thickness
less than 0.354 in. (9 mm), replace them.
Repair
Actual repairs are limited to the removal of small burrs and
other minor surface imperfections from gears and shafts.
Use a fine stone or emery cloth for this work. Do not use
steel wool.
1.
Worn or damaged parts must be replaced. Refer to the
applicable Parts Listing for specific replacement parts
information.
2.
Inspect all remaining parts for evidence of damage.
Replace or repair any part which is in questionable
condition. The cost of the part is often minor in
comparison with the cost of redoing the job.
3.
Smooth out all nicks, burrs, or galled spots on shafts,
bores, pins, or bushings.
4.
Examine all gear teeth carefully, and remove nicks or
burrs.
5.
Polish the edges of all shaft shoulders to remove small
nicks which may have been caused during handling.
6.
Remove all nicks and burrs caused by lockwashers.
7.
Replace all gaskets, oil seals, and 'O' rings removed
during winch disassembly.
Assembly Instructions
Winch Assembly
(Ref. Dwg. D6310041)
1.
Gear box assembly.
1.1.
Assembly of the shaft spindle (18)
−
Install bearing (44) with the retainer ring
(40)
−
Put the shaft spindle (18) in the bearing
(4).Install the gear wheel (43) with the
retainer ring (37)
1.2.
Assembly of the fixed annular gear (19).
−
Install the friction disc (21) and steel disc
(22) in the gear box (45).
−
Install the 'O' ring (20) and the pin (39).
−
Install the 'O' ring (9) in the fixed annular
gear (19) , install this ass'y in the gear box
(45) and secure with the retainer ring (17).
1.3.
Install the needle bearings (14) and the spacer
(16) in the planet (15).
Summary of Contents for LIFTSTAR
Page 11: ...11 NOTES...
Page 12: ...12 WINCH ASSEMBLY DRAWING Dwg D6310041...
Page 14: ...14 AIR GEAR MOTOR ASSEMBLY DRAWING Dwg D6310005...
Page 20: ...20 NOTES...
Page 22: ...22 TWO LEVER PENDANT ASSEMBLY DRAWING Dwg D5790002...
Page 31: ...31 NOTES...
Page 32: ...32 NOTES...
Page 33: ...33 NOTES...