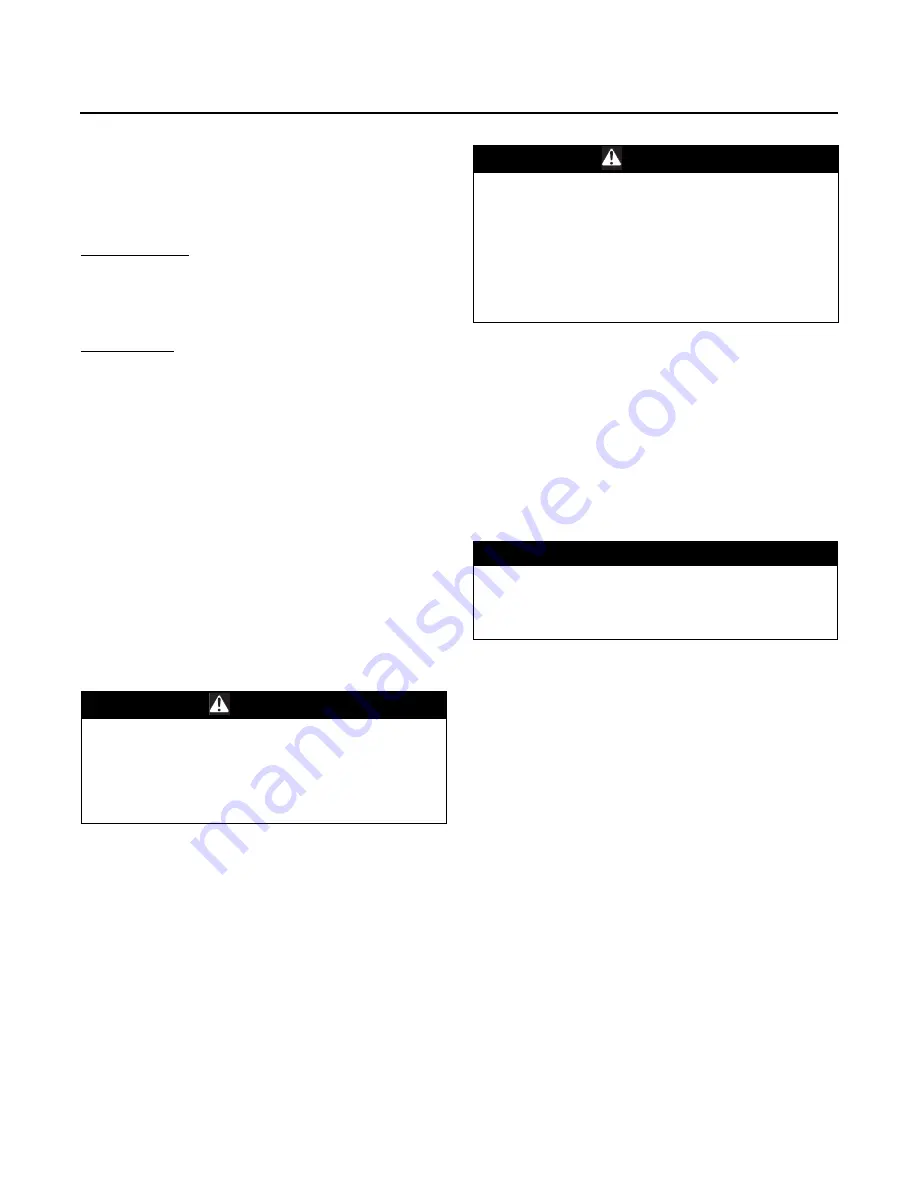
Installation
RT-SVX058B-EN
21
•
V1, V2, V3 = Line Voltage Readings
•
VD = Line Voltage reading that deviates the farthest
from the average voltage.
Example: If the voltage readings of the supply power
measured 221, 230, and 227, the average volts would be:
•
VD (reading farthest from average) = 221
•
The percentage of Imbalance equals:
The 2.2 percent imbalance in this example exceeds the
maximum allowable imbalance of 2.0 percent. This much
imbalance between phases can equal as much as a
20 percent current imbalance with a resulting increase in
motor winding temperatures that will decrease motor life.
If the voltage imbalance is over 2 percent, notify the proper
agencies to correct the voltage problem before operating
this equipment.
Electrical Phasing (Three Phase Motors)
The compressor motor(s) and the supply fan motor are
internally connected for the proper rotation when the
incoming power supply is phased as A, B, C.
Proper electrical supply phasing can be quickly
determined and corrected before starting the unit by using
an instrument such as an Associated Research Model 45
Phase Sequence Indicator and following the steps below:
•
Turn the field supplied disconnect switch that provides
power to the main power terminal block or to the
“Line” side of the optional factory mounted disconnect
switch to the “Off” position.
•
Connect the phase sequence indicator leads to the
terminal block or to the “Line” side of the optional
factory mounted disconnect switch as follows;
Black (phase A) to L1
Red (phase B) to L2
Yellow (phase C) to L3
•
Close the field supplied main power disconnect switch
or circuit protector switch that provides the supply
power to the unit.
•
Observe the ABC and CBA phase indicator lights on the
face of the sequencer. The ABC indicator light will glow
if the phase is ABC. If the CBA indicator light glows,
open the disconnect switch or circuit protection switch
and reverse any two power wires.
•
Restore the main electrical power and recheck the
phasing. If the phasing is correct, open the disconnect
switch or circuit protection switch and remove the
phase sequence indicator.
Compressor Crankcase Heaters
Each compressor can be equipped with a crankcase
heater. The proper operation of the crankcase heater is
important to maintain an elevated compressor oil
temperature during the “Off” cycle to reduce oil foaming
during compressor starts. Oil foaming occurs when
refrigerant condenses in the compressor and mixes with
the oil. In lower ambient conditions, refrigerant migration
to the compressor could increase.
When the compressor starts, the sudden reduction in
crankcase pressure causes the liquid refrigerant to boil
rapidly causing the oil to foam. This condition could
damage compressor bearings due to reduced lubrication
and could cause compressor mechanical failures.
Before starting the unit in the “Cooling” mode, set the
system switch to the “Off” position and turn the main
power disconnect to the “On” position and allow the
crankcase heater to operate a minimum of 8 hours.
Before closing the main power disconnect switch, insure
that the “System”selection switch is in the “Off” position
and the “Fan” selection switch is in the “Auto” position.
Close the main power disconnect switch and the unit
mounted disconnect switch, if applicable.
221 + 230 + 227
= 226 Avg.
3
100 X 226 - 221
= 2.2%
226
WARNING
Hazardous Voltage!
Disconnect all electric power, including remote
disconnects before servicing. Follow proper lockout/
tagout procedures to ensure the power can not be
inadvertently energized. Failure to disconnect power
before servicing could result in death or serious injury.
WARNING
Live Electrical Components!
During installation, testing, servicing and
troubleshooting of this product, it may be necessary to
work with live electrical components. Have a qualified
licensed electrician or other individual who has been
properly trained in handling live electrical components
perform these tasks. Failure to follow all electrical
safety precautions when exposed to live electrical
components could result in death or serious injury.
NOTICE:
Compressors Failure!
Unit must be powered and crankcase heaters energized
at least 8 hours BEFORE compressors are started. This
will protect the compressors from premature failure.