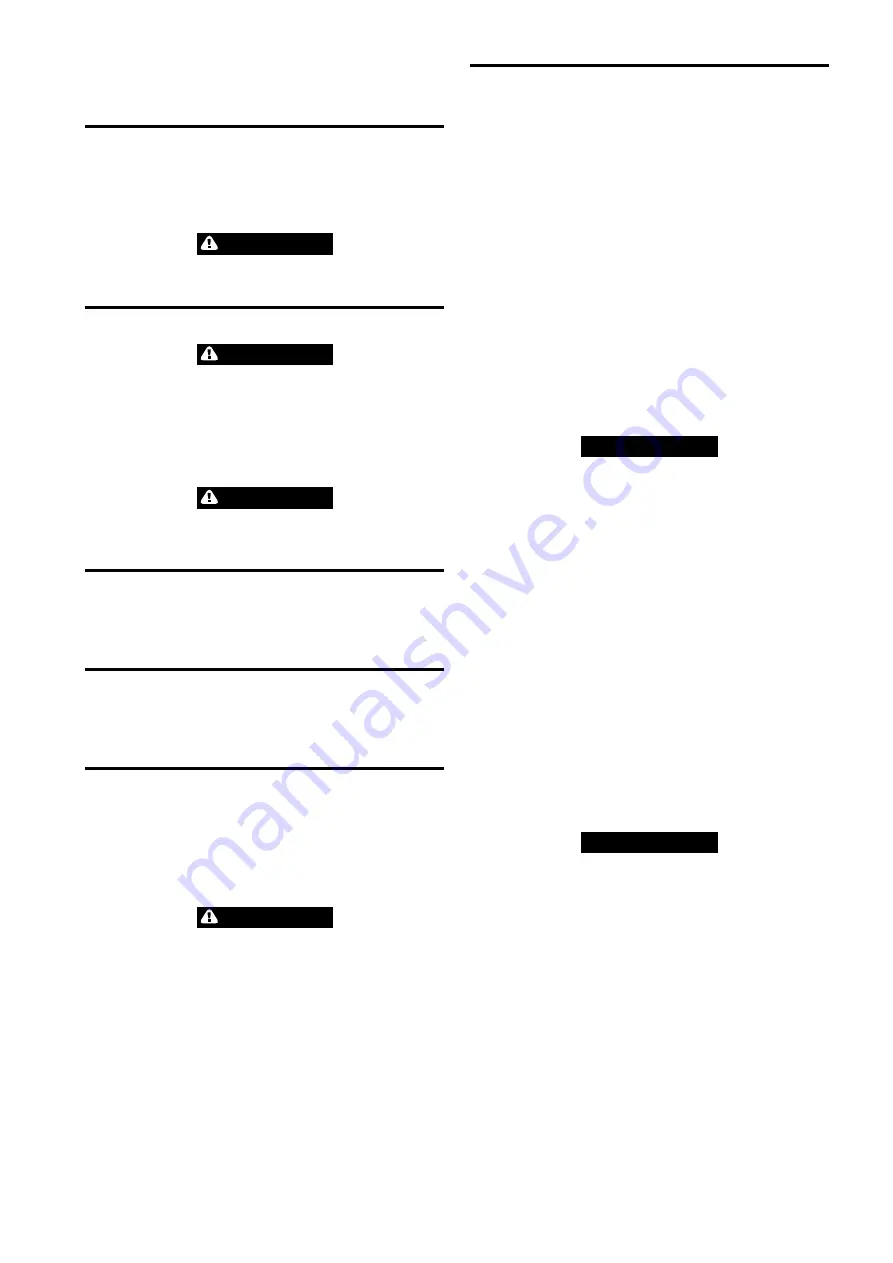
Adjustments to cylinder clevis can be made to compensate for normal brake lining
wear. The drum brake must be kept properly adjusted to hold the required load. Refer
to ‘Adjustments’ in the “MAINTENANCE” section of Product Maintenance Information
Manual. If brake band cannot be adjusted to hold rated load, the brake must be
disassembled, inspected and repaired.
n
Winch Motor
During normal operation moisture can collect in the motor housing. This accumulation
should be drained regularly. To drain, locate and remove oil level, pipe plug (121) in
bottom of motor housing (118). Any fluid drained should be disposed of in an
environmentally safe manner. Excess moisture in the housing will decrease bearing
life. In addition, freezing moisture can damage motor components.
WARNING
• Before operating winch replace any oil drained from motor while removing
any excess moisture. Refer to “LUBRICATION” on page 9.
n
Slack Line Detector
CAUTION
• Slack line detector and limit switch functions are not operable when
emergency release valve is activated.
Refer to Dwg. MHP3147.
If slack line exists between winch and sheave, slack line detector limit switch valve
stops wire rope payout. When slack wire has been detected, operator must determine
and rectify problem prior to resuming operation.
Slack Line Detector arms may vary in design depending on required take-off angle.
Ensure correct arms are used for desired take-off angle.
WARNING
• Operator and signal persons must watch for any conditions that allow slack
wire rope to exist between sheave and lifted person which may not be sensed
by the slack wire detector. If slack wire condition is noticed, all winch
operations must cease until problem is rectified.
n
Press Roller
Refer to Dwg. MHP2740.
The press roller, positioned between drum flanges, assists proper spooling of wire
rope onto the drum and maintains tight wraps when winch is not in operation. Ensure
wire rope is always trapped between press roller and drum barrel. Press roller
adjustments are not required.
n
Limit Switches
Pre-set limit switch settings prevent winch wire rope payout and haul-in by stopping
air flow to the winch motor when a set point has been reached. It is the owner’s and
operator’s responsibility to adjust winch operating limits prior to using the winch to
transport personnel. To adjust the limit switch set points refer to the “INSTALLATION”
n
Stowage Valve (Optional)
Stowage valve is for use in applications where contact with the winch wire rope by
other equipment could occur. In the un-stowed position, the winch will operate as
usual. In the stowed position, the main air supply to the winch is shut off. Main
supply air is ported to the automatic disc brake, which holds the disc brake open. If
other equipment contacts the wire rope, the winch will be able to spool out, allowing
wire rope tension to decrease. A load of approximately 200 lbs (90 kg) is required to
cause the winch to spool out. None of the winch controls are operable in the stowed
position. The valve must be locked in either position to prevent inadvertent change
of valve position.
CAUTION
• If the stowage valve is not used and the wire rope is contacted by other
equipment, damage could occur to winch and/or wire rope. Damage to winch
may not be visible and could result in a catastrophic failure of the winch.
n
Stowing Winch
1. Haul-in winch until wire rope is in a stowed condition.
2. Press emergency stop button to shut off air supply to winch.
3. Release manual band brake.
4. Remove lock from the stowage valve.
5. Engage stowage valve by depressing red knob.
6. Reinstall lock on stowage valve.
n
Un-Stow Winch
1. Remove lock from stowage valve.
2. Release stowage valve by pulling knob in an upward manner.
3. Reinstall lock on stowage valve.
n
Emergency Lowering
The following information is provided to allow for emergency lowering of a person if
air supply is lost to winch. These procedures should be used if no other method of
safely lowering personnel is available.
Winch is equipped with two emergency lowering devices.
n
Precautions
1. Emergency lowering operations must be performed by a minimum of two
personnel trained in the operation of the winch.
2. Communication must be established between lifted person and winch operators.
Operators should be able to visually monitor lifted person until landed.
3. If line of sight between operators and lifted person is not possible, signals must
be conveyed to the operators.
4. The winch must be isolated from the supply air system during emergency lowering
operations.
n
Procedure
Use the following options for lowering in an emergency.
Automatic Band and Disc Brake:
The use of two people are required for this procedure. Both operators shall monitor
the lifted personnel.
1. Shut off main power supply at the source.
2. To activate emergency lowering device, remove pipe plug from valve body and
connect an air or nitrogen line of 60 psi (410 kPa/4.1 bar). Refer to Dwg. MHP2289
A.
Push button to release brake;
B.
Remove plug and connect
auxiliary air to port 1/4 inch NPT.
NOTICE
• With maximum rated load, lowering speed can reach 50 feet per minute (15
metres per minute).
3. Release of valve button stops emergency lowering and sets the disc brake. Speed
may be improved by moving throttle lever in payout direction.
4. Ensure emergency stop button is in the off position (not activated).
5. With one operator in control of the automatic drum brake, the other operator
presses and holds emergency release valve button to begin lowering.
6. Remove release lever from its stored location on winch.
7. Refer to Dwg. MHP3150 on page 13,
A.
Install release lever under cylinder clevis;
B.
Disengage slowly.
8. Slowly release automatic band brake by pushing down on release lever. Do not
fully open band brake.
9. Drag band brake to control lowering speed.
10. If lowering speed becomes too fast, allow spring in brake cylinder to pull release
lever up, allowing further drag to band brake.
11. Return release lever to its stored location once emergency lowering operation is
completed.
12. If there is insufficient weight for Emergency Lowering Device to work refer to
‘Alternative Measures’ on page 7.
Three Way Valve (optional lowering procedure):
Refer to Dwg. MHP3143 on page 11,
A.
Normal Inlet Air Supply;
B.
Rotate handle
to use in normal condition;
C.
FRL;
D.
Emergency Lowering Inlet.
This device allows the person to be moved the shortest way to safety in case of normal
air supply failure. In the event of air supply failure, operate the three way valve from
normal air supply to the emergency inlet. For an emergency power source, a 50 litre
nitrogen bottle can be used.
1. Open the emergency power source. Rotate valve lever towards normal inlet air
supply side.
2. Ensure that downstream pressure is 5 to 7 bar.
3. Operate winch slowly to open brakes for lowering the person the shortest way to
safety.
NOTICE
• After each use of emergency lowering device, return the three-way valve to
the main air inlet and check the secondary power source is in proper working
condition and able to fulfil its task.
n
Emergency Lowering Using Accumulator (optional feature)
Winch may be supplied with an accumulator. In an emergency lowering condition
open accumulator valve air tank and follow steps 1 through 11 above in ‘Automatic
Band and Disc Brake’ section on page 7. The use of two people are required for this
procedure.
n
Alternative Measures
If brake release methods listed above do not allow the person to lower, there may
not be enough weight to overcome the natural mechanical resistance of winch
gearbox and motor. The minimum load for emergency lowering is 200 lbs (91 kg) on
the first layer.*
* Refer to Table 2 ‘General Specifications’ on page 3 or minimum load at different
layers.
1. If motor will not backdrive, attach a line to the man riding device and carefully
pull down suspended person.
Form MHD56470 Edition 4
7