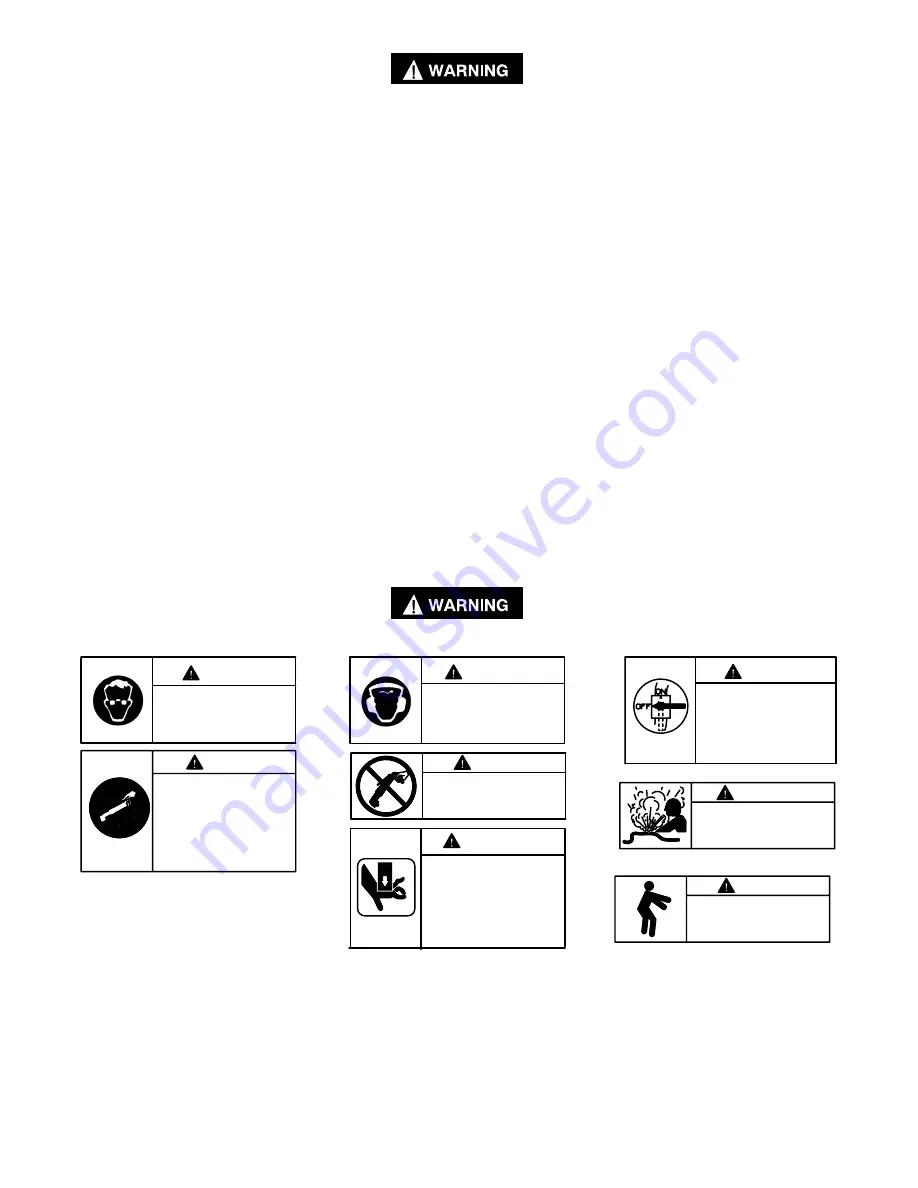
2–2
FAILURE TO OBSERVE THE FOLLOWING WARNINGS COULD RESULT IN INJURY.
USING THE TOOL (Continued)
•
Do not remove the Inlet Plug without first discon-
necting the live air supply.
•
Whenever the Angle Head is installed or reposi-
tioned, the Throttle Lever must be positioned so
that reaction torque will not tend to retain the
throttle in the “ON” position.
•
When installing or removing the output device on
any tool, ALWAYS grasp a metal component of
the tool while tightening or loosening the Coupling
Nut or Spindle Cap. Acceptable clamping
locations include, but are not limited to, the hex on
the Gear Case, the Tool Hanger, the Torque Reac-
tion Arm or any metal Mounting Plate. NEVER
grasp the composite tool body or handle in vise
jaws to restrain the torque of the Coupling Nut or
Spindle Cap. Such practice will result in damage
to the tool.
•
Do not use power units and gear trains that exceed
the capability of the output device.
•
The Tube Nut Attachment has an opening on
the front side for construction and application
purposes. DO NOT, under any circumstance
place your fingers in this opening.
•
The Torque Reaction Bar must be positioned
against a positive stop. Do not use the Bar as a
dead handle and take all precautions to make
certain the operator’s hand cannot be pinched
between the Bar and a solid object.
•
When operated continuously for long periods of
time, Series D Nutrunners may become hot at the
spindle end of the tool. Take all precautions
necessary to avoid skin contact with the hot
surfaces. Prolonged contact may result in burns.
•
All Series D Torque Control Wrenches and
Nutrunners with reverse capability have rotation-
al arrows molded into the housing in the area of
the reversing mechanism. When the direction
switching device is positioned nearest the molded
circular arrow with an “F” in the center, spindle
rotation will be forward or clockwise direction.
When the direction switching device is positioned
nearest the molded circular arrow with an “R” in
the center, spindle rotation will be reverse or
counterclockwise direction.
WARNING LABEL IDENTIFICATION
FAILURE TO OBSERVE THE FOLLOWING WARNINGS COULD RESULT IN INJURY.
Always wear eye protection
when operating or perform-
ing maintenance on this
tool.
WARNING
WARNING
Always wear hearing
protection when operating
this tool.
Always turn off the electrical
supply and disconnect the
power cord before installing,
removing or adjusting any
accessory on this tool, or
before performing any
maintenance on this tool.
WARNING
WARNING
Do not use damaged, frayed
or deteriorated power cords.
WARNING
Keep body stance balanced
and firm. Do not overreach
when operating this tool.
WARNING
The Torque Reaction Bar must
be positioned against a
positive stop. Do not use the
Bar as a dead handle and take
all precautions to make certain
the operator’s hand cannot be
pinched between the Bar and
a solid object.
Powered tools can vibrate in
use. Vibration, repetitive mo-
tions or uncomfortable posi-
tions may be harmful to your
hands and arms. Stop using
any tool if discomfort, tingling
feeling or pain occurs. Seek
medical advice before resum-
ing use.
WARNING
Do not carry the tool by
the cord.
WARNING