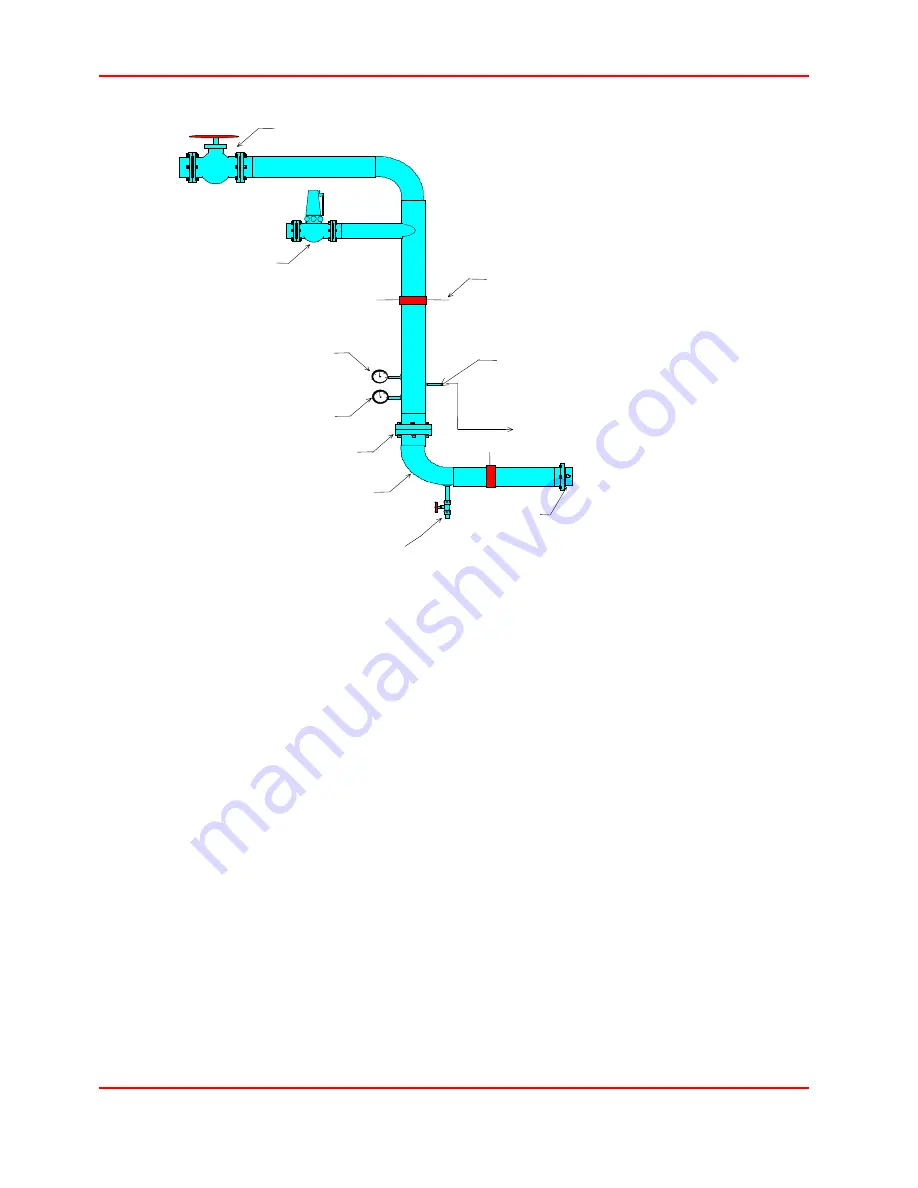
C950 PLANNING & INSTALLATION MANUAL
15
TP0029 Rev.5
Ó
2000 Ingersoll-Rand Company
Date of Revision: 15 August, 2000
Figure 6
Model Discharge Pipe
Adequate piping support is needed to prevent excessive dead loads on the compressor
flange. Provisions should be made in the discharge piping so that all alignments are made in
the piping and not the compressor.
Discharge Air Piping for Multi-Compressor Installation
Parallel Operation with Positive Displacement Compressors
The steep performance curve of the Centac compressor allows for operation in parallel with
piston or rotary screw compressors (s
ee Figure 7)
. However, piping layout design should
isolate the Centac compressor from the pulsations in the discharge produced by these
compressors. Piping the Centac compressor into the discharge header downstream of the
pulsation bottle or receiver effectively eliminates pulsation problems.
Fast valve operation allows the lagging compressors to supply huge quantities of air at
system pressure. Proper consideration to the entry of this added capacity into the system will
eliminate control or surging problems commonly associated with this type of installation.
Discharge piping from the compressor should enter the system header by way of long radius
elbows or at an angle in the direction of flow. By staggering entry into the header the added
capacity will have no detrimental effect on the other units already on line.
Centac compressor connections and sizes are located on the certified customer prints. Refer
to the General Arrangement Drawing and the Process and Instrumentation Diagram for
further detail.
Located a minimum
of 3 pipe diameters
from check valve
Block valve
Pipe hanger
Low point drain
Long radius elbow
Maintenance flange
Discharge pressure
Discharge temperature
Safety valve
check valve
CA tap in. To be located a minimum
of 10 pipe diameters from check valve
in non-turbulent flow area.
Compressor
mounted
Non-rusting control air line.
Connects to control panel at
connection marked ‘CA’
01_
23 of 41
90.10_Pre-Installation and Operation Manual