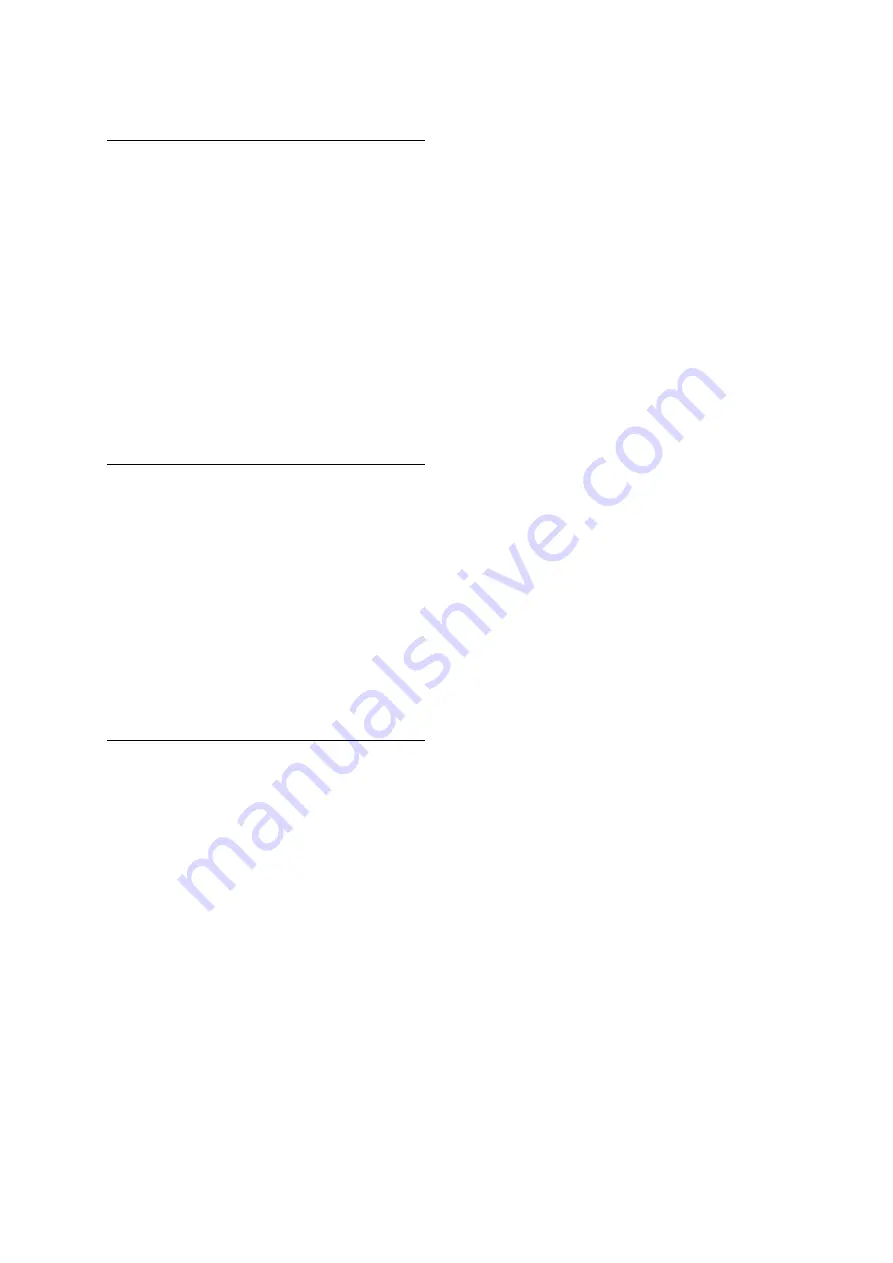
11
ASSEMBLY OF THE IR15BV AND IR15BS PAVING BREAKERS
GENERAL INSTRUCTIONS
•
Before assembly of the breaker, clean all parts
thoroughly and lubricate surfaces with a thin
film of recommended oil (see Lubrication).
•
Apply a film of O-ring lubricant to all O-rings
before final assembly.
•
It is recommended that the assembling of the
nozzle (2) and the liner (33) should be carried
out by the manufacturer or authorised distribu-
tor.
•
The existence of a piston air cushion should be
determined. Hold the cylinder vertically and al-
low the piston to drop down the bore small di-
ameter first. An air cushion is present if the pis-
ton “bounces” at the bottom of the cylinder and
no metal to metal contact noise can be heard. If
a cushion is not present contact your authorised
Ingersoll –Rand repair centre for advice.
CYLINDER ASSEMBLY
Grip the cylinder (1) vertically in a vice protected
with leather or copper covered vice jaws.
Lubricate and insert the piston (4) small end first
into the bore. - Check for cushion.
Position valve location pins (38) into the holes in the
end of the cylinder.
Lubricate and slide the valve (35) into the valve body
(36) renew valve ring (37) and replace valve cover
(31) over valve body.
Grip the assembly and shake to check that the valve
can be heard to move freely.
Locate the valve assembly onto the location pins (38)
and position the valve spacer (30) on top.
Replace the sealing ring (28).
HANDLE ASSEMBLY
BV models only:
If the handle stop (14) was removed during disas-
sembly it should be replaced with a new part as the
retaining feature is severed on removal. Locate the
stop in the hole in the handle and tap sharply into
place using a soft drift and hammer.
If the hand grip rubbers (10) have been removed these
should now be replaced. Lubricate the inside of the
rubber with soapy water and slide the new rubber
into position, retain each rubber with washer (39) and
screw (40).
Assemble left and right hand, hand grips (8 and 9),
trigger (7) together with sleeve (13), lubricate around
the pivot area and position the sub assembly along
the slot in handle body (5).
Note it is usual to position the trigger lever on
the same side as the air inlet of the handle body.
Locate the handle springs (11) between hand grips
and handle body and fix the assembly in place by
drifting or pressing in handle pivot pin (12).
Lubricate the trigger pin (15) , trigger ball (16) and
replace in the air inlet connection of the handle body.
Note the trigger pin has a reduced diameter
which is placed next to the trigger ball.
Locate the trigger spring (17) on top of the trigger
ball. Apply thread retainer (loctite 243, or similar)
on the thread of the inlet bushing (18) and tighten
to 200 Nm (147 lb.ft) torque.
Check that the handles and trigger move freely.
BS models only:
If the handle bar has been disassembled from the
handle body.
Securely support the handle body (42) beneath a
press and position the handle bar (43) in the mating
body hole.
Note: Ensure that the handle bar has the cor-
rect orientation and alignment to accept the
trigger pin (45) when pressed home.
Press home the handle bar to depth until the lock
pin-hole is aligned.
Press or drift in the lock spring pin.
Lubricate and replace the trigger pin (46). Note the
trigger pin has a reduced diameter which is placed
next to the trigger ball.
Check that the trigger pin can move freely.
Position the trigger lever (44) and secure in place
with spring pin (45)
Lubricate the trigger pin (46), trigger ball (16) and
replace in the air inlet connection of the handle body.
Note the trigger pin has a reduced diameter
which is placed next to the trigger ball.
Locate the trigger spring (17) on top of the trigger
ball. Apply thread retainer (loctite 243, or similar)
on the thread of the inlet bushing (18) and tighten
to 200 Nm (147 lb.ft) torque.
Check that the trigger moves freely.
Lubricate the inside of the handle grip rubber (47)
with soapy water and slide the new rubber into po-
sition.