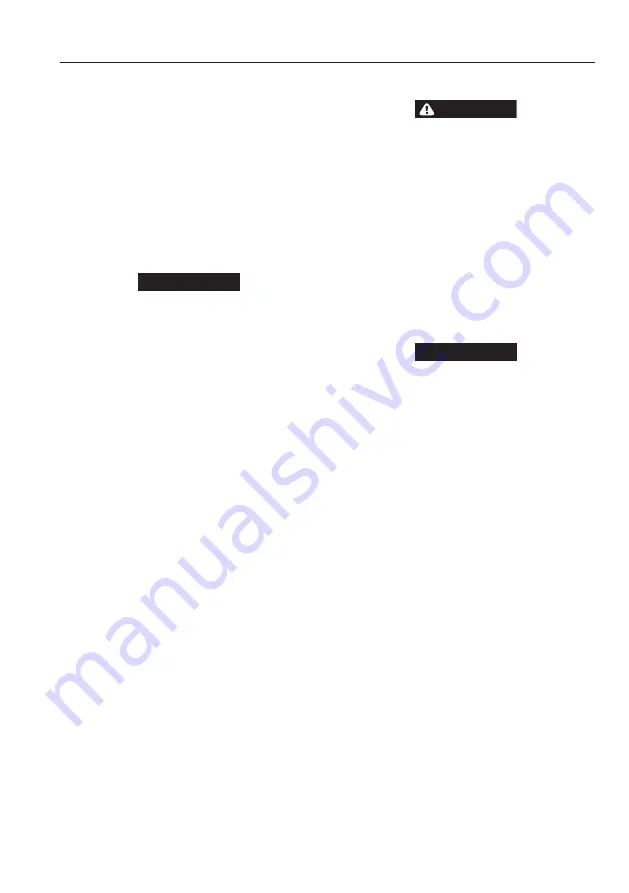
16606006_ed1
3
Assembly
General Instructions
Always press on the
inner
ring of a ball-type bearing when
installing the bearing on a shaft.
Always press on the
outer
ring of a ball-type bearing when
pressing the bearing into a bearing recess.
Whenever grasping a tool or part in a vise, always use
leather-covered or copper-covered vise jaws. Take extra care with
threaded parts and housings.
Always clean every part and wipe every part with a thin film of oil
before installation.
Apply a film of O-ring lubricant to all O-rings before final
assembly.
Assembly of the Motor
Using an arbor that contacts only the
outer
ring of the Bearings,
press the Rotor Bearings (31),
shielded side first
, into the
recesses in the Cylinder End Plates (32).
NOTICE
Press only on the bearing inner ring when installing the end
plate and bearing assemblies on the rotor hubs.
Be sure to press each assembly onto the rotor hub until the
bearing
inner
ring contacts the Rotor Bearing Spacer (30).
2. Be sure the rubber Air Port Gaskets (27) and Gasket Retaining
Springs (28) are in good condition and that one of each is in
position in each of the six air ports in the wall of the Cylinder (26)
before sliding the motor assembly into the Motor Housing (1).
3. Install the Backhead (21) and secure the Backhead Cap
Screws (24).
Assembly of the Impact Mechanism
Stand the Ball Cam (58), large open end up, on the press table.
Seat one hammer spring thrust bearing ring, grooved side up, in
the recess in the Ball Cam.
Place the ball and retainer assembly on top of this ring. Place the
second bearing ring, grooved side first, on top of the bearing
balls.
Stand the Hammer Spring (56), either end first, on top ring of the
Hammer Spring Thrust Bearing (57). Pass the Arbor (60), large
end first, through the spring and bearing bores and centralize it
in the Ball Cam.
Align the holes in the hammer wall with the cam groove points
in the Ball Cam and slide the Hammer over the Cam, allowing the
arbor pilot to pass through the hole in the front of the Hammer.
Place a sleeve over the arbor pilot and seat it against the end faces
of the hammer jaws. Press on the sleeve, forcing the Hammer
down over the Ball Cam, against the compression of the Hammer
Spring, until a Cam Ball (59) can be inserted into each cam groove
through the holes in the hammer wall.
Insert one Ball into each hole and slowly release the pressure.
Replacement of Planet Gear Bearings
1. When replacing Planet Gear Bearings (43), use a bearing Inserting
Tool. Using a flat-faced arbor can damage the bearing shell.
2. Press only on the bearings
stamped face
.
3. Press one Bearing in from each end of the gear bore. Do not use
one Bearing to force the other into position.
1.
2.
3.
4.
5.
1.
1.
2.
3.
4.
5.
6.
7.
Assembly of the Impact Wrench
WARNING
Never attempt to assemble a Model 599A1 Impact Wrench
without a hoist, block and tackle or other lifting device. The
complete Impact Wrench and its major assemblies are too heavy
to be manually handled. Follow the recommended procedure for
assembly below.
1. Make sure that the square driver is engaged in a large Socket, and
that the Socket is resting on level footing so that the Hammer
Case containing the assembled impact mechanism components
are standing upright to prevent the tool from tipping over during
assembly.
2. Screw a hook or eyebolt having a 3/4”-10 thread shank into the
tapped hole in the Arbor (60). Using the hoist, lower the
Hammer (55) with assembled parts, into the Hammer Case.
3. Attach the hoist sling to the planet gear frame assembly and
lower the Gear Case with assembled parts onto the
Hammer Case (62).
4. Attach the hoist sling to the Motor Housing and lower the Motor
Housing with assembled parts onto the Gear Case.
5. Install the Hammer Case Bolts (51) and (52) to secure the Gear
Case and Motor Housing in position.
NOTICE
Periodically examine the Hammer Case Bushing (63). Install a
new Bushing if the present one is worn to the extent that the
shank on the Anvil (61) is a loose fit in the bushing bore. See the
following instructions.
Oversize Hammer Case Bushings
The continued use of a worn Hammer Case Bushing may permit the
Bushing to deform or enlarge the hole in the front of the Hammer
Case so that the Case no longer retains the Bushing properly. Should
the Bushing become loose in the Case, an oversize Bushing should
be installed. Bushings .005”, .010”, .015” and .031” are available. The
amount of oversize is etched on the oversize Bushing; the standard
size Bushing is unmarked. After removing a loose Bushing, examine
it for oversize etching. If unmarked, replace it with a .005” oversize
Bushing; if it is marked, replace it with the next larger oversize
Bushing. When pressed in, the oversize Bushing will automatically
true up the deformed opening in the Hammer Case.
Reverse Valve Bushing
When installing a new Reverse Valve Bushing (4), align the scribe
marks on the Bushing and Motor Housing (1).