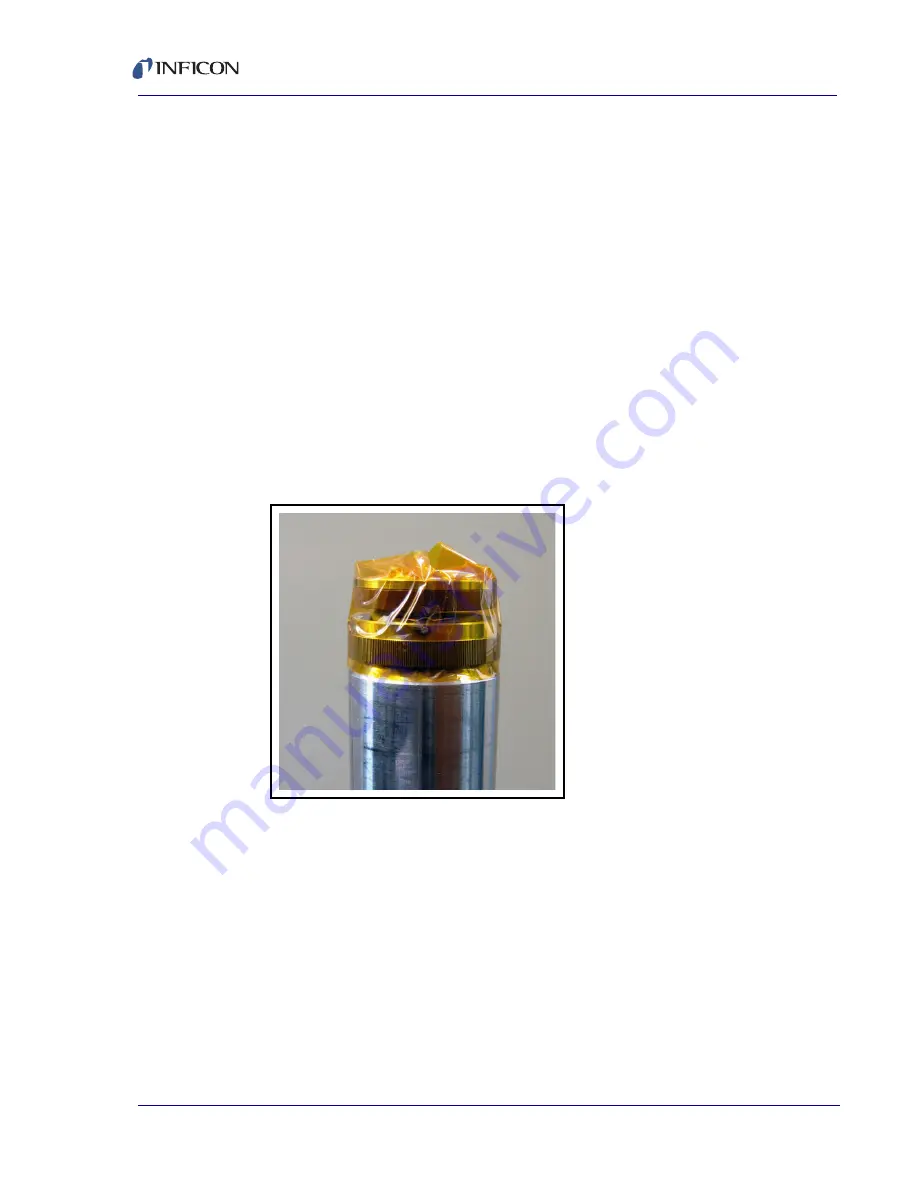
2 – 6
RSH-600 Operating Manual
2.5 Adjustable Flange Installation
1
Apply a small amount of vacuum compatible grease to the entire surface of the
O-ring that is included with the adjustable flange and then install the O-ring into
the O-ring groove in the adjustable flange.
2
Loosen the hex socket head screw on the adjustable flange.
3
Remove the cover from the RSH-600 sensor.
4
If the crystal holder contains any crystals, remove the holder and remove and
discard the crystals. Reinstall the crystal holder.
5
Cut a piece of Kapton® tape (or equivalent), 3.8 cm (1.5 in.) to 5.08 cm (2 in.)
wide, to a length of approximately 16 cm (6.3 in.).
6
Position the Kapton tape with the bottom edge of the tape on the beveled
surface just below the knurled ring. Not starting at any of the three bayonet
pins, wrap the tape around the circumference of the sensor. Fold the excess
tape over the top of the crystal holder. See
.
Figure 2-5 Wrap Kapton tape