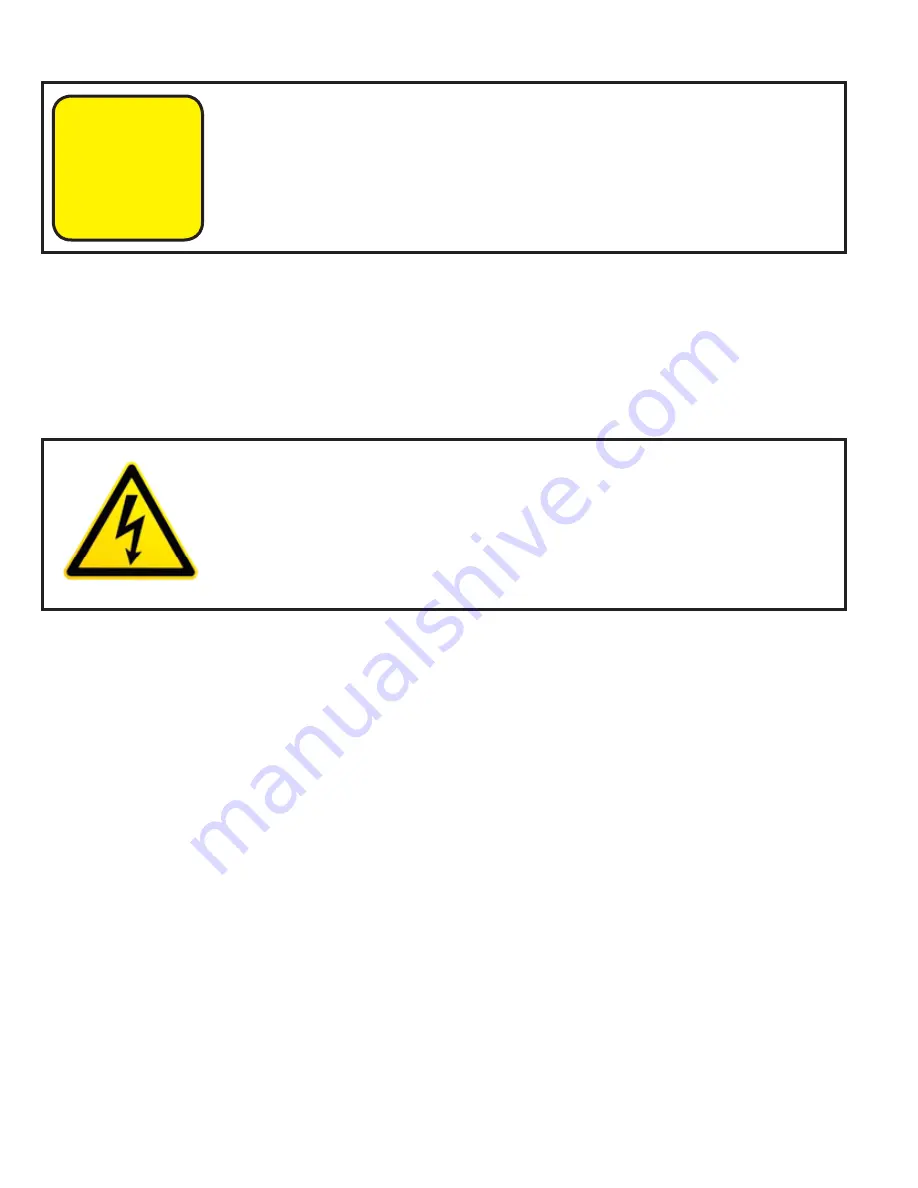
ASME coded pressure vessels must not be modified, welded,
repaired, reworded or subjected to operation conditions outside
the nameplate ratings. Such actions will negate code status,
affect insurance status and may cause severe personal injury,
death, and property damage.
The installation, wiring, and all electrical controls must be in ac-
cordance with ANSI C1 National Electric Code, ANSE C2 National
Electric Safety Code, state and local codes. All electrical work
should be performed by a qualified electrician. Failure to abide by
the national, state and local codes may result in physical and/or
property damage.
!
CAUTION
PRESSURE VESSELS
Air receiver tanks and other pressure containing vessels such as, but not limited to, pulsation bottles, heat
exchangers, moisture separators and traps, shall be in accordance with ASME Boiler and Pressure Vessel
Code Section VIII and ANSI B19.3 Safety Standards.
ELECTRICAL
Before installation, the electrical supply should be checked for adequate wire size and transformer capac-
ity. During installation a suitable fused or circuit breaker disconnect switch should be provided. Where a
3 phase motor is used to drive a compressor, any unreasonable voltage unbalance between the legs must
be eliminated and any low voltage corrected to prevent excessive current draw. Compressors must be
equipped with a properly wired magnetic motor starter or a pressure switch rated to carry the full motor
current load. The coil which engages and disengages the contact points in the motor starter is controlled
by the pressure switch. Never attempt to bypass the pressure switch or adjust it past the factory set pres-
sure range. Improper installation of the electrical system can cause the motor to overheat or a short circuit
to occur.
Industrial Gold Air Compressors
|
800-531-9656
| www.industrialgold.com
7.5, 10, 15 HP Electric Reciprocating Compressor