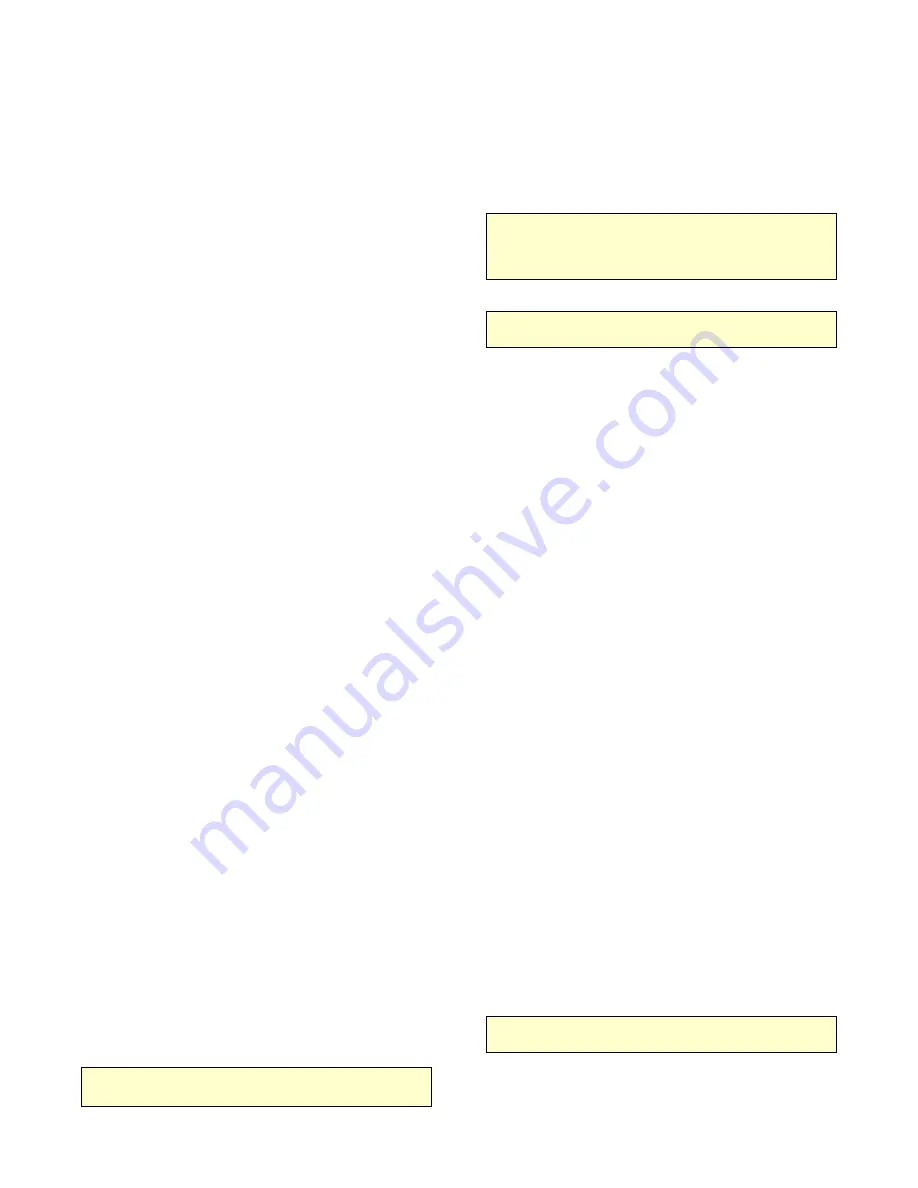
DA440HU:
4-2
99900782: 19941223
Periodically, draw off a sample of the oil and check
the oil for breakdown. To check oil quality:
1. Place the oil in a clean glass.
2. Smell the oil to detect a burnt or rancid odor.
3. Visually examine the oil for a dark or cloudy
appearance.
4. Allow the sample to stand for several minutes.
Inspect the sample for water which will settle to the
bottom of the glass if present. Water can result from
a system leak or condensation due to temperature
extremes.
When any of these conditions is observed, the
system should be purged and filled with new oil. In
addition, the oil should be changed in the reservoir
and complete system:
1. After every 800 hours of operation or every six
months, whichever occurs first.
2. After pump or other major hydraulic component
failure, drain the hoses.
4-3-4. HYDRAULIC SYSTEM PURGING
Purging the hydraulic system requires a new oil
supply sufficient to completely fill the reservoir,
hoses, filters, valves, etc., and an extra allowance for
loss during this procedure. To reduce oil loss,
operate the engine at a low speed (idle).
When purging, new oil is supplied to the pump
suction line via the reservoir, and the old oil is
discharged through the reservoir return line.
Two operators will be required; one to operate the
compressor and the other to regulate pump flow
(engine speed).
Purging is accomplished as follows:
1. Drain the hydraulic reservoir and disconnect the
suction hose to the pump. Drain the hose and
reassemble. Change the suction filter cartridge
(Paragraph 4-3-5).
NOTE
THE METHOD OF WASTE DISPOSAL IS LEFT TO THE
DISCRETION OF SERVICE PERSONNEL.
2. Disconnect the reservoir return line at the
reservoir and direct the discharge into a sump or
waste container. Plug the return line port on the
reservoir and fill the reservoir with clean oil (refer to
Paragraph 4-3-1).
NOTE
BE THOROUGHLY FAMILIAR WITH THE FOLLOWING
STEPS AND PREPARED TO PERFORM THEM IN AN
UNINTERRUPTED SEQUENCE. IF THIS IS NOT DONE,
EXCESSIVE OIL WASTE WILL OCCUR.
CAUTION
DO NOT ALLOW THE RESERVOIR LEVEL TO DROP
BELOW 1/3 CAPACITY DURING THIS OPERATION.
3. Start the engine and engage the PTO. Slowly
release the clutch. Activate the control valve so that
the fluid passes through the motor. Allow fluid to
discharge for about 15 seconds. Kill the engine.
4. Reconnect the return line to the reservoir port
and change the return line filter. All components of
the system are now purged.
5. Check the reservoir oil level and add oil as
necessary.
4-3-5. FILTER ELEMENT
REPLACEMENT
To avoid residue accumulation in the reservoir and to
protect the hydraulic components (valves,
pumps,motors, etc.), the filters must be serviced on a
regular basis.
They must be changed after the initial 50-hours of
new unit operation and every 200-hours thereafter.To
change filter elements:
1. Shut the gate valve and remove the filter
element.
2. Install the new filter ensuring proper rubber seal
seating and tighten as much as possible using both
hands.
3. Open the gate valve and check for leaks.
CAUTION
PUMP FAILURE CAN RESULT IF THE SHUTOFF VALVE
IS LEFT CLOSED.
Summary of Contents for Diamond air DA440HU
Page 6: ...DA440HU 99900782 1 2 19941223 NOTES...
Page 12: ...DA440HU 99900782 3 2 19941223 NOTES...
Page 16: ...DA440HU 4 4 99900783 19941223...
Page 18: ...DA440HU 99900782 5 2 19941223 FIGURE E 2 HYDRAULIC SYSTEM TROUBLESHOOTING CHART...
Page 20: ...DA440HU 6 2 FIGURE F 1A DA440HU HYDRAULIC UNDERDECK COMPRESSOR 23000081 2 23000081 02 19941223...
Page 22: ...DA440HU 99900782 7 2 19941223 FIGURE G 2 TIRE LOAD AND INFLATION PRESSURES...
Page 23: ...DA440HU 99900782 7 3...