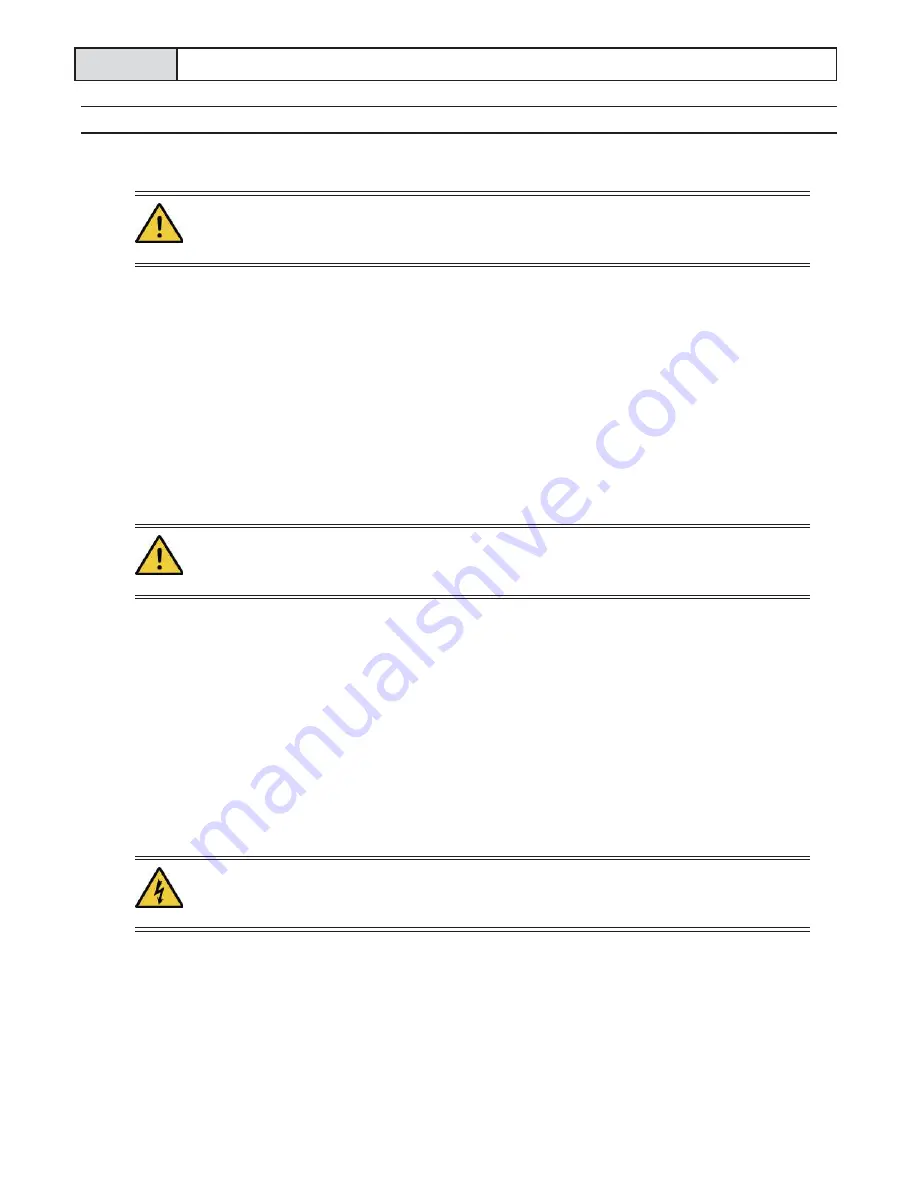
S125E
Operating Manual
6
2.5
Repair Work, Maintenance Activities, and Default Repair on the Job Site
Mechanical Service Work
These activities can only be undertaken by qualified personnel. Please follow any
special safety instructions in the various chapters on servicing the machine (see
Chapter 7).
Before starting any servicing work on the machine, put the machine in the Safety off position (as
described in Chapter 2.6) in order to prevent the machine from being switched on accidentally.
Adjustments, servicing, and inspection work and inspection intervals specified in these Operating
Instructions as well as any information on the replacement on parts and systems of the machine must
be undertaken and/or complied with.
The operator must be informed of any maintenance or repair work done to the machine.
Startup and shut off procedures must be done in accordance with the Operating Instructions during
all work related to the use, repair, and adjustment of the machine. The repair personnel must also be
aware of the safety devices during inspection, maintenance, and repair.
The machine must be shut off completely for repair or maintenance work. Please
disconnect the main plug in order to prevent the machine from being switched on
accidentally.
The dust collector bin must be emptied before transportation. Please handle in accordance with the
regulation how to dispose the dust and make sure that you meet the local regulations. Do not use any
aggressive cleaning materials! Use only lint-free cleaning cloths.
Always remember to tighten any screw connections that are undone during servicing and
maintenance work!
If safety devices need to be dismantled during setting up, servicing, or repair work, these safety
devices must be reinstalled and inspected immediately after completion of the service.
Make sure that process materials and replacement parts are disposed of safely and in an
environmentally-friendly manner.
Work on the electrical parts of the equipment may only be undertaken by a skilled
electrician or by a trained person under the guidance and supervision of a skilled
electrician in accordance with the electrical engineering regulations.
Make sure that electrical components used for replacement purpose comply with the original parts
and are correctly adjusted if necessary.
Summary of Contents for STREAMER S125E
Page 1: ...Operating Manual S125E Your Partner for Mobile Surface Preparation IMPACTSamericas com...
Page 35: ...Operating Manual S125E 33 10 2 Wheel Drive...
Page 36: ...S125E Operating Manual 34 10 3 Housing Assembly...
Page 37: ...Operating Manual S125E 35 10 4 Valve Actuator Assembly...
Page 38: ...S125E Operating Manual 36 10 5 Base Seal Assembly...
Page 39: ......