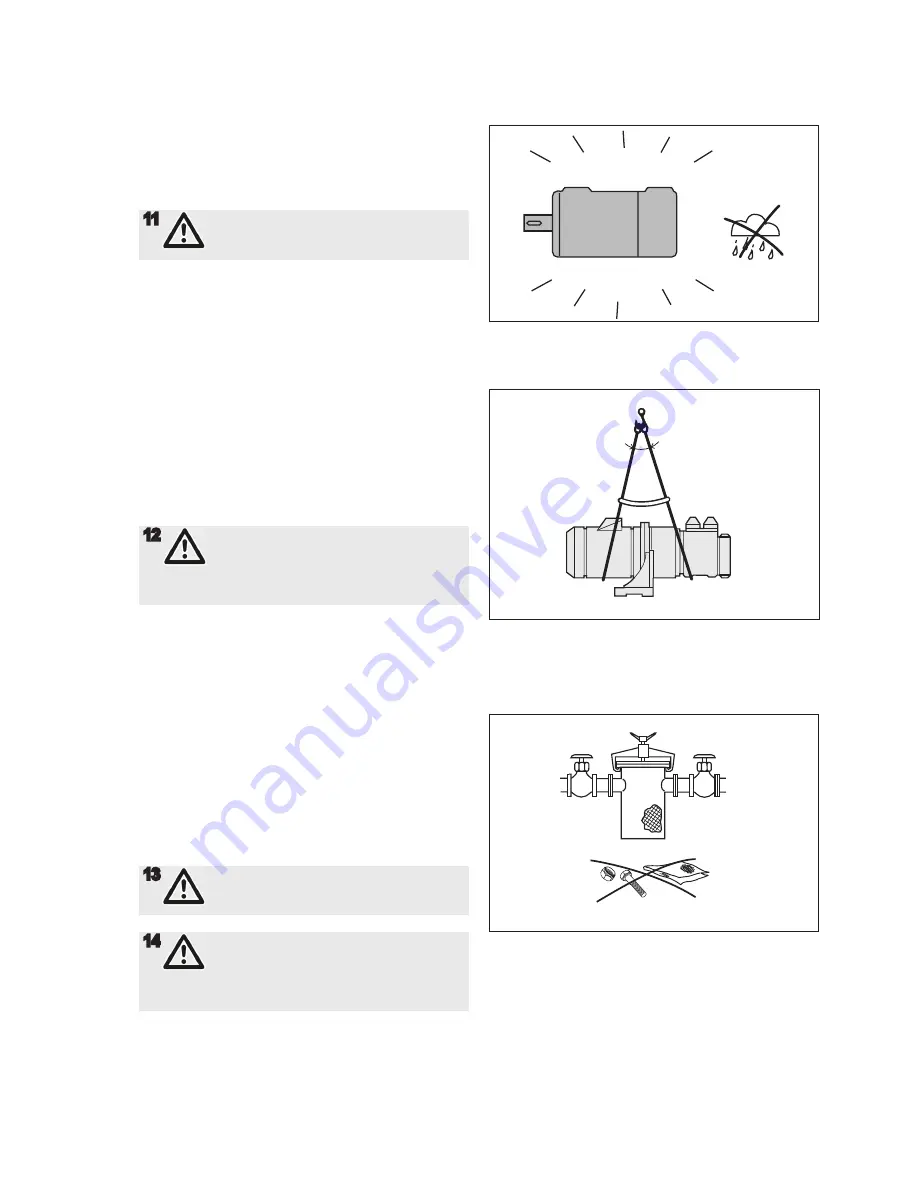
AC
G
8 2
01
8.
01
e
n-
G
B
, I
D
-No
.: 1
63
-0
43
/A
www.imo.se
5
max. 90°
min. 60°
Fig 2. Lifting the pump
Design limitations and technical data for each pump
are found in the Product description. Installation of IMO
AB low pressure pumps does not require special skills.
However, these instructions presume that the work is
carried out by experienced fitters!
11
Failure to comply with these instructions
may cause damage and personal injury
Transport and storage
Always protect the pump against ingress of water
and other impurities. Store the pump in a clean, dry
and warm environment. The pump is delivered with
the internals oiled and with protective covers over the
pipe connections and drain openings. These covers
should remain in place for as long as possible during
the mounting and installation procedure but must be
removed before start up.
Lifting of pump
Lifting of the complete pump unit with the lifting device
attached to the motor, should be avoided as the motor’s
lifting provisions may not be able to carry the combined
weight of the pump and motor.
12
All pumps should be lifted with straps
securely attached to the pump or pump
unit, so that the center of gravity is located
between the straps in order to avoid
tipping of the pump.
Strainer
The pump has to be protected from foreign matters
such as weld slag, pipe scale, etc., that could enter the
pump via the suction line. If the cleanliness of the sys-
tem cannot be guaranteed, a strainer must be installed
in the inlet pipe near the pump. For practical reasons
a suction strainer with 0.8-2.0 mm mesh openings is
recommended.
The size of the strainer should be selected so that it is
large enough to allow adequate pressure at the pump
inlet. The pressure drop across the strainer should
preferably not exceed 0.1 bar at max. flow rate and nor
-
mal operating viscosity. A vacuum gauge between the
strainer and the pump inlet is recommended to indicate
when the strainer needs cleaning.
13
All work carried out on the pump has to be
performed in such a manner that risks for
personal injury are observed.
14
Lifting a complete pump unit, using
slings or hooks attached to the pump or
connecting frame may be dangerous since
the centre of gravity of the pump unit may
be higher than the points of attachement.
Fig. 3 Strainer
Installation
Fig 1. Keep dry and clean