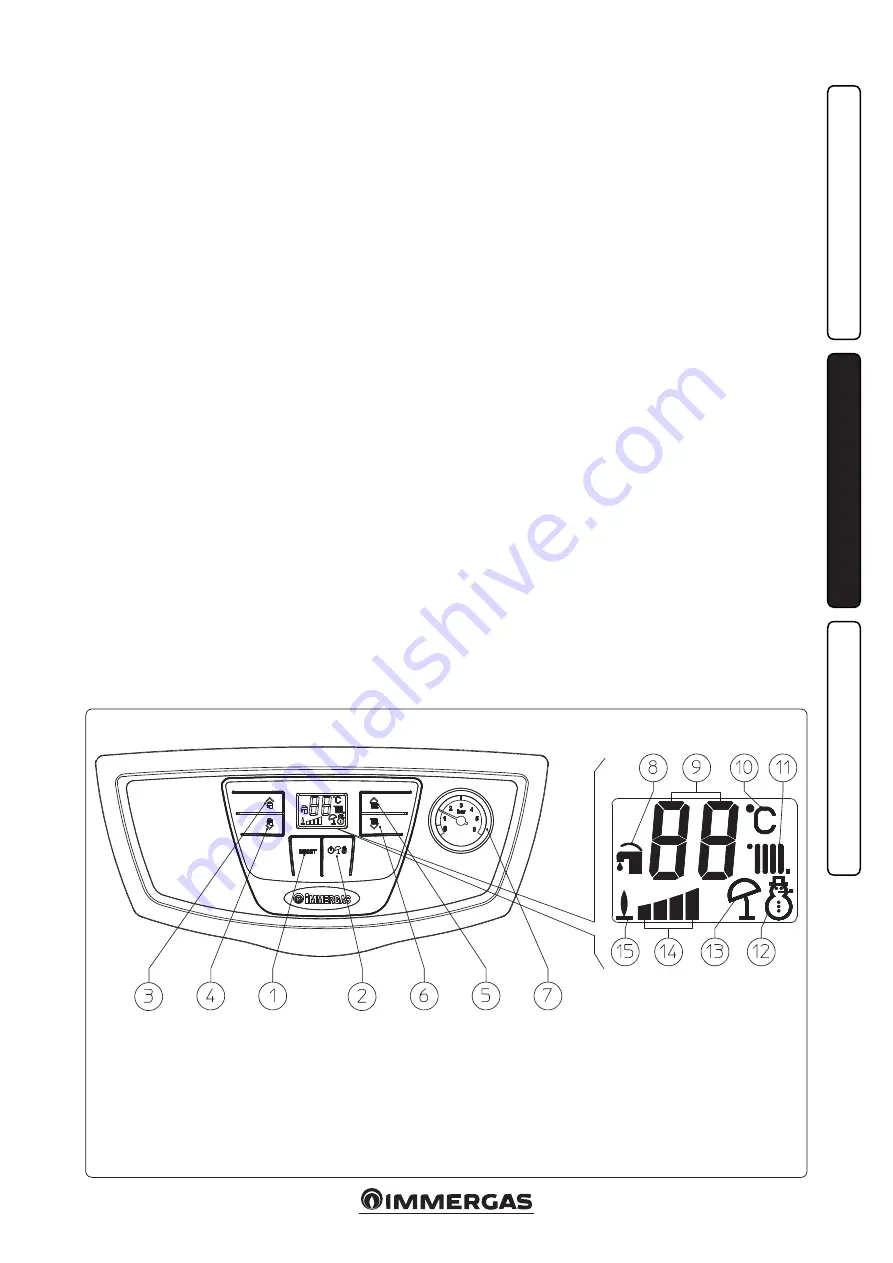
19
2-1
INS
TALLER
US
ER
MAINTEN
AN
CE TECHNI
CI
AN
2
USE AND MAINTENANCE
INSTRUCTIONS
2.1 CLEANING AND MAINTENANCE.
Attention:
to preserve the boiler's integrity
and keep the safety features, performance and
reliability, which distinguish it, unchanged over
time, you must at least execute maintenance
operations on a yearly basis in compliance
with what is stated in the relative point at “an-
nual check and maintenance of the appliance”,
in compliance with national, regional, or local
standards in force. Annual maintenance is es-
sential to validate the conventional warranty of
Immergas. We recommend stipulating a yearly
cleaning and maintenance contract with profes-
sionally qualified personnel.
2.2 GENERAL WARNINGS.
Never expose the wall-mounted boiler to direct
vapours from cooking hobs.
Use of the boiler by unskilled persons or children
is strictly prohibited.
Do not touch the flue gas exhaust terminal (if pre-
sent) due to the high temperatures it can reach;
For safety purposes, check that the concentric
air intake/flue exhaust terminal (if fitted), is
not blocked.
If temporary shutdown of the boiler is required,
proceed as follows:
a) drain the heating system if anti-freeze is not
used;
b) shut-off all electrical, water and gas supplies.
In the case of work or maintenance to structures
located in the vicinity of ducting or devices for
flue extraction and relative accessories, switch
off the appliance and on completion of opera-
tions ensure that a qualified technician checks
efficiency of the ducting or other devices.
Never clean the appliance or connected parts
with easily flammable substances.
Never leave containers or flammable substances
in the same environment as the appliance.
•
Attenzione:
the use of components involving
use of electrical power requires some funda-
mental rules to be observed:
- do not touch the appliance with wet or moist
parts of the body; do not touch when barefoot.
- never pull electrical cables or leave the appli-
ance exposed to weathering (rain, sunlight,
etc.);
- the appliance power cable must not be replaced
by the user;
- in the event of damage to the cable, switch off
the appliance and contact exclusively qualified
staff for replacement;
- if the appliance is not to be used for a certain
period, disconnect the main power switch
upstream of the appliance.
2.3 CONTROL PANEL.
Key:
1 - Reset button
2 - Stand-by/summer/winter button
3 - Button (+) to increase
the domestic hot water temperature
4 - Button (-) to reduce
the domestic hot water temperature
5 - ) to increase the system water
temperature
6 - Button (-) to reduce the system water
temperature
7 - Boiler manometer
8 - Domestic hot water functioning
9 - Temperatures and error code display
10 - Unit of measurement
11 - Central heating functioning
12 - Winter
13 - Summer
14 - Power distributed
15 - Flame presence
Summary of Contents for NIKE MYTHOS 24 2E Series
Page 1: ...EOLO MYTHOS 24 2E IE Instruction and warning book 1 038791ENG ...
Page 2: ......
Page 31: ...31 ...