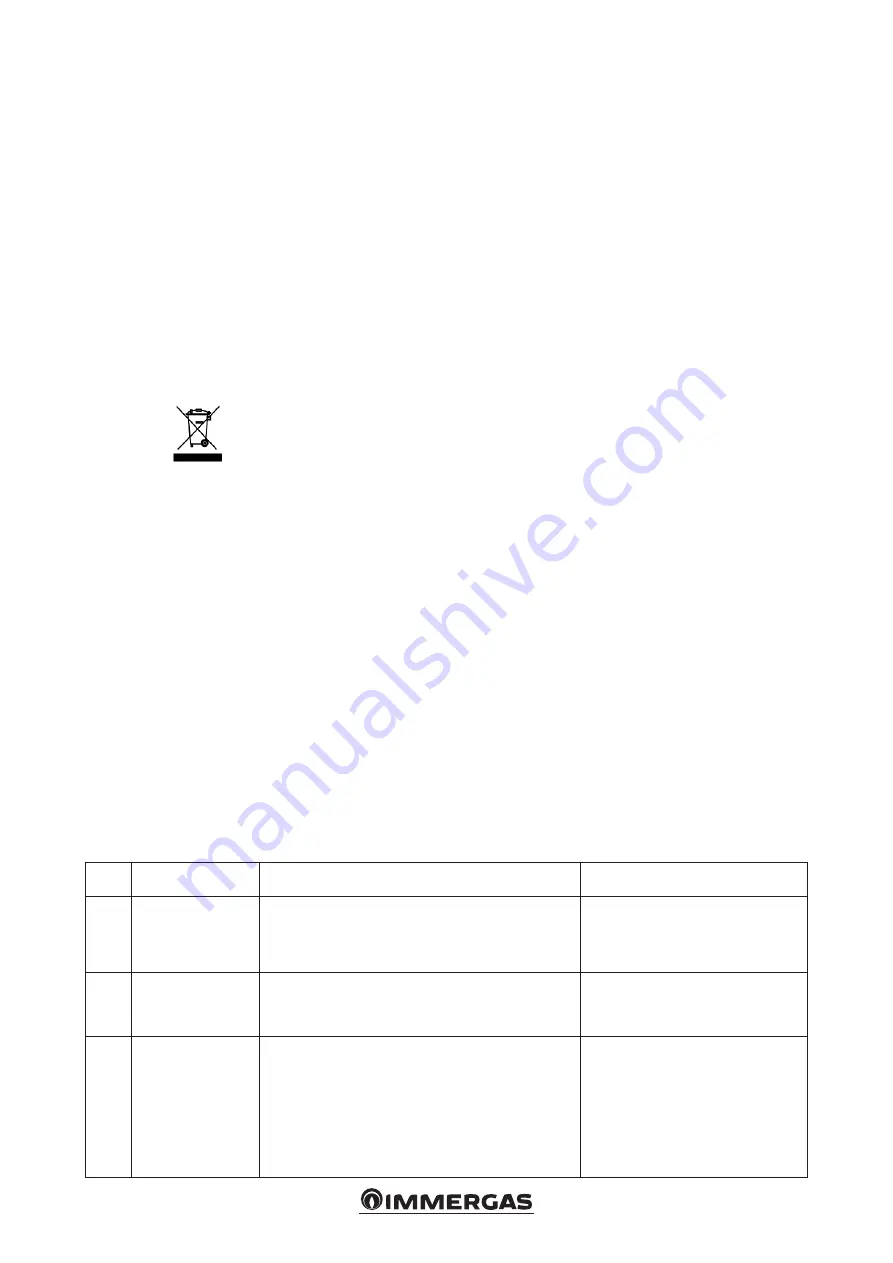
22
4
RECOMMENDATIONS
- MAINTENANCE AND
REPAIRS
4.1 ADVICE FOR THE USER.
You must empty the water heater if the absence
mode cannot be used or when the device is
powered down. Proceed in the following way:
• Cut the power supply.
• Close the cold water inlet tap.
• Open a hot water tap.
• Put the safety valve in the drain position.
Important note - End of the device’s service life:
• At the end of its service life, the device must
be taken to a sorting centre for electrical and
electronic equipment for recovery of fluids.
Do not dispose of the device with household
waste, but dispose of it in the collection cen-
tres provided, where it can be recycled. Check
your local collection service to find out about
existing waste collection centres.
• It is forbidden by law to discharge into the
atmosphere the cooling fluid contained in the
appliance. Degassing operations are strictly
forbidden, and may be hazardous.
N.B.:
the GWP (Global Warming Potential) of
R513A is 631.
4.2 HOUSEHOLD MAINTENANCE.
The user must perform some minor home main-
tenance operations on the water heater: act on the
safety valve once or twice a month to remove any
limestone deposits and ensure it is not blocked.
Regularly check that there are no alarms on the
display. If there are any alarms, contact the au-
thorised local service centre to address the faults.
It is recommended to treat water with a softener
in the areas where there is a high amount of scale
(Th>20°f).
Water hardness must remain above
15°f.
The softener does not lead to warranty der-
ogations, provided it is dosed in a workmanlike
manner and regularly maintained.
Water treatment must comply with the National/
local provisions in force.
4.3 MAINTENANCE BY APPROVED
PROFESSIONALS.
The appliance must be checked by a profession-
al every 2 years, in order to ensure its long-term
performance
.
• Disconnect the appliance from the electricity
(circuit-breaker, fuses, etc.)
• Drain the tank:
- close the cold water inlet tap of the safety unit,
- open a hot water tap,
- put the safety valve in the drain position.
• Remove the front cover.
• Disconnect the wires from the thermostat
terminals.
• Dismantle the heating unit.
• Replace the magnesium anode. The magnesium
anode has to be changed every 2 years or as
soon as its diameter is less than 10mm.
• Remove the scale deposited as sludge or flakes
in the bottom of the tank, and carefully clean
the casings of the heating elements and ther-
mostat. Do not scratch or remove the scale
attached to the walls, as this could affect the
coating. Residues may be removed using a
water and dust vacuum cleaner.
• Refit the heating unit with a new seal, carefully
and gradually tightening the nuts (cross-tight-
ening).
• Fill the water heater by leaving a hot water tap
open, if the water flows it indicates that the
water heater is full.
• Check the water tightness of the seal and only
then replace the thermostat and its fittings, and
reconnect the power supply.
• The next day, check the water tightness of the
seal again and gently tighten the nuts again if
necessary.
• Check the electrical connections.
• Check that the temperature probe is properly
positioned in the sample point near to the
electrical integration (the probe must be at the
bottom of the sample point).
Evaporator:
• The cleanliness of the evaporator and the fan
must be checked
every year
. Clogging of these
components may reduce the performance of
the heat pump.
• Unscrew and remove the front cover to access
the evaporator. The rear cover may also be
removed if necessary.
• If necessary, the evaporator and the fan are to
be cleaned with a soft bristle brush. Brush the
evaporator very gently to avoid damaging its
fins. If the fins are folded, straighten them using
a suitable brush.
Note:
always disconnect the device from the
power supply before starting any work.
Expansion valve:
• Only a refrigeration engineer is permitted to
access the expansion valve adjustment screw.
If the expansion valve is adjusted without
approval from the manufacturer, the product
warranty shall be voided.
• Generally speaking, it is not recommended to
change the expansion valve setting before all
other repair solutions have been exhausted.
Condensate draining pipe:
• Check cleanliness of the condensate evacuation
pipe. Any pollution (dust) in the room may in
fact cause deposits in the condensate recovery
tank. These deposits may block the condensate
evacuation tube, and cause excessive accumu-
lation of water in the tank, which could lead to
malfunctions.
4.4 TROUBLESHOOTING SUPPORT.
Control panel alarm codes
Errors can be suspended or reactivated by
pressing “OK”.
This action also stops the buzzer.
Error
Code
Cause
Consequences
System status / Solution
03
Faulty water
temperature probe or
out of measurement
range
Water temperature reading impossible: no central heating / C.H.
Check the connection (reference A1) of the wa-
ter temperature probe (sample point). Check
the resistance of the probes (see table below).
If necessary, replace the probe.
07
No water in the
storage tank or ACI
connection open
No warming up.
Put the storage tank in the water.
Check the thread connection (reference AC),
conductivity of the water.
09
Water temperature too
hot (T> 80°C)
Risk of mechanical safety device activation: no central heating /
C.H.
Check if the real water temperature at the sam-
ple point is high (T>80°C).
Check the connection (reference A1) and the
positioning of the water temperature probe
(sample point), it must be at end run.
Check that the electrical integration is not
permanently fed. Reset the mechanical safety, if
necessary.
Summary of Contents for 3.030072
Page 31: ...31...