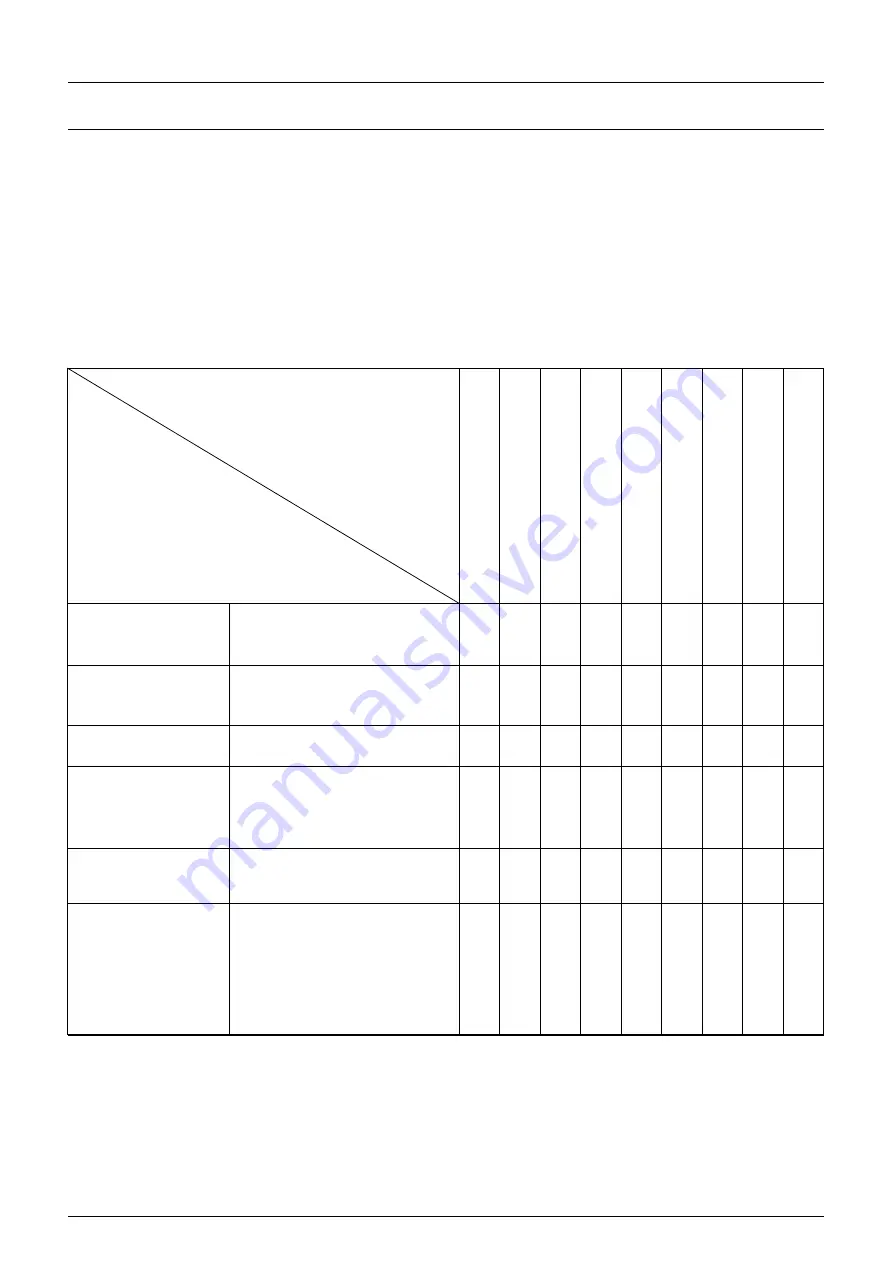
CHECK FAULTS
When abnormal situation such as failure of welding, unstable arc, poor welding result, do not
consider that it must be some faults.
The machine may be well but just some reasons cause abnormality such as that some connectors
are loosened, forget to turn on the switch, wrong setting, broken cable and gas pipe, etc. So before
maintenance, Please check it up first, some problem may be solved.
The following is earlier checking diagram by this way. In the top right corner item you can find the
problem, please check according to the diagram for the one with “O” mark.
EARLIER CHECKING DIAGRAM FOR THE ABNORMAL
The abnormal
Place and item to be checked
N
o
arc
ing
N
o
ga
s
Ca
n
no
tS
en
d
w
ire
Po
or
A
rcin
g
init
iati
on
U
nst
ab
le
arc
W
eld
ing
m
arg
in
un
cle
an
W
ire
an
d
M
ate
ria
lc
on
glu
tin
ate
d
W
ire
lin
ks
Ele
ctr
ic
lea
din
g
ho
le
fco
n
co
ng
luti
na
ted
H
av
e
air
ho
le
Power supply box
(
input protective
set
)
1
、
connected or not
2
、
fuse broken
3
、
connector loosen
〇
〇
〇
〇
〇
〇
Input cable
1
、
Broken or not
2
、
Connector loosen
3
、
overheat
〇
〇
〇
〇
〇
〇
Power
1
、
Switched or not
2
、
lack phase
〇
〇
〇
〇
〇
〇
〇
〇
Gas cylinder&adjuster
1
、
open cover
2
、
remains of gas
3
、
flow setting volume
4
、
Connecting point loosen
〇
〇
Gas pipe (access from
the high-pressure
cylinder to torch)
1
、
Connecting point loosen
2
、
Pipe broken
〇
Wire sending
equipment
1
、
Wheel and leading tube not
match
2
、
Wheel broken, slot blocked
or lack
3
、
Over pressing or loosen,
powder store up in entrance
of SUS tube
〇
〇
〇
〇
〇