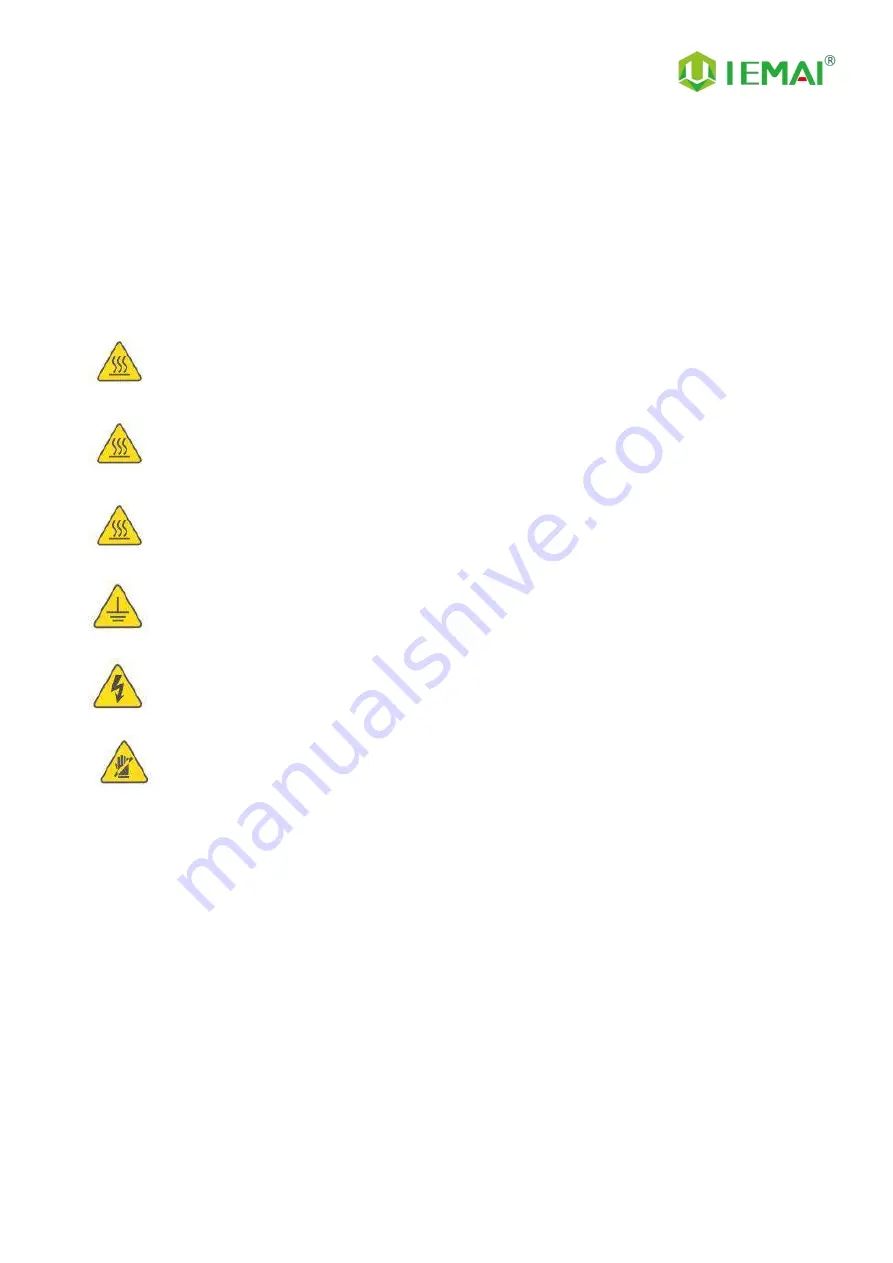
Print More Materials, All For Application
3
1.3 Safety
The device has a specialized motion structure, control system and electrical control parts, users
need to pay careful attention to the safety label when using it to prevent burns, pinching, electric
shock, or other safety problems.
The maximum temperature of the print head of this equipment can reach 450°
C, its heating is strictly prohibited to touch
The maximum temperature of the printing platform of this equipment can
reach 150 °C, its heating is strictly prohibited to touch
The maximum temperature of the chamber of this equipment can reach 90°C,
and it is strictly forbidden to touch it when it is heated.
Ensure that the power supply grounding terminal is well grounded to prevent
the printer from not working properly or posing a risk of electric shock
Do not disassemble the case without permission, be careful of electric shock
When the printer is working, it is forbidden to move in the printing area to
prevent collision, belt turning in, etc.