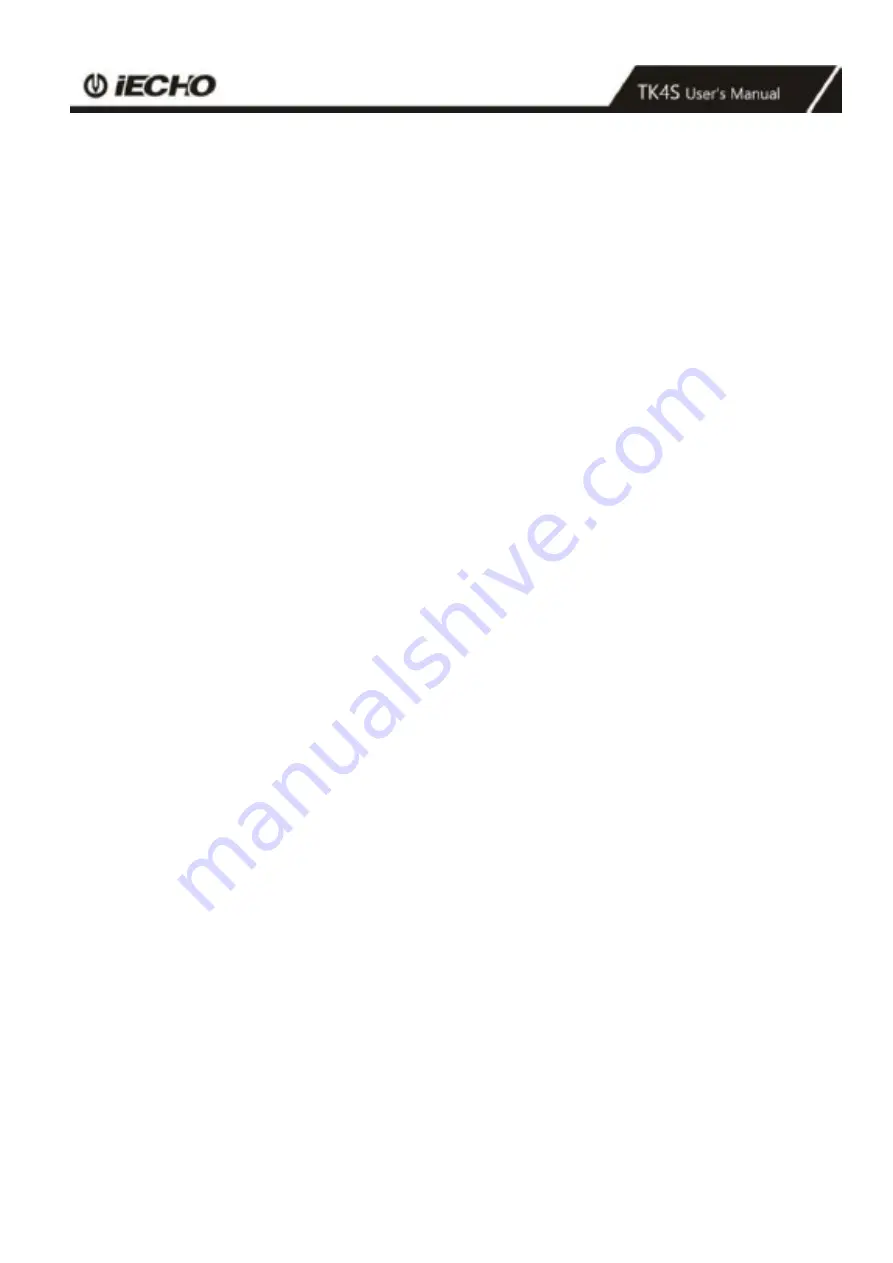
1
1. Equipment Overview
IECHO Automatic Digital processing line can be used for full-time production, fulfilling the requirement of high
efficiency, by using the maximum capacity of the machine to complete the 24/7 production.
1.1 Features
Regional vacuum zone
Vortex vacuum control
Automatic sheet feeding
Conveyor system
Camera registration system
High-speed and high-precision cutting tools
Collection table for cutout elements picking
No manual operation needed
1.2 Composition
TK4S series digital cutting machine series is composed of Electrical box, Main body, Vacuum and Auxiliary devices.
Software includes file processing part and machine controlling part.
According to user’s demand, one or more tools can be used: Tangent Tool, Oscillating Tool, Kiss-Cut Tool, Router,
V-Cut Tool, Creasing Tool, Driven Rotary Tool, North & Drill Tool, Pen.
User can scan the bar code created by RIP software.
1.3 Working Principles
Import the files into SmartCut/iBrightCut, the user can process the files (editing and nesting) and send the processed
cutting files to CutterServer. According to the cutting files, the controlling system will create motion control signals. With
the signals, servo motors execute the tools lift/down and modules movement. Thereby, the machine achieves the high-
speed and high-precision cutting
Summary of Contents for TK4S
Page 1: ...1...
Page 19: ...15 3 2 3 Connecting the Pause cables...
Page 22: ...18 3 3 2 On the basis of frame work assemble the aluminum table Aluminum table...
Page 31: ...27...
Page 48: ...44...
Page 50: ...46 3 17 2 Large table milling support device The total height 2 8 m...
Page 51: ...47...
Page 52: ...48 3 18 Install the Covers of The Front and Rear Side...