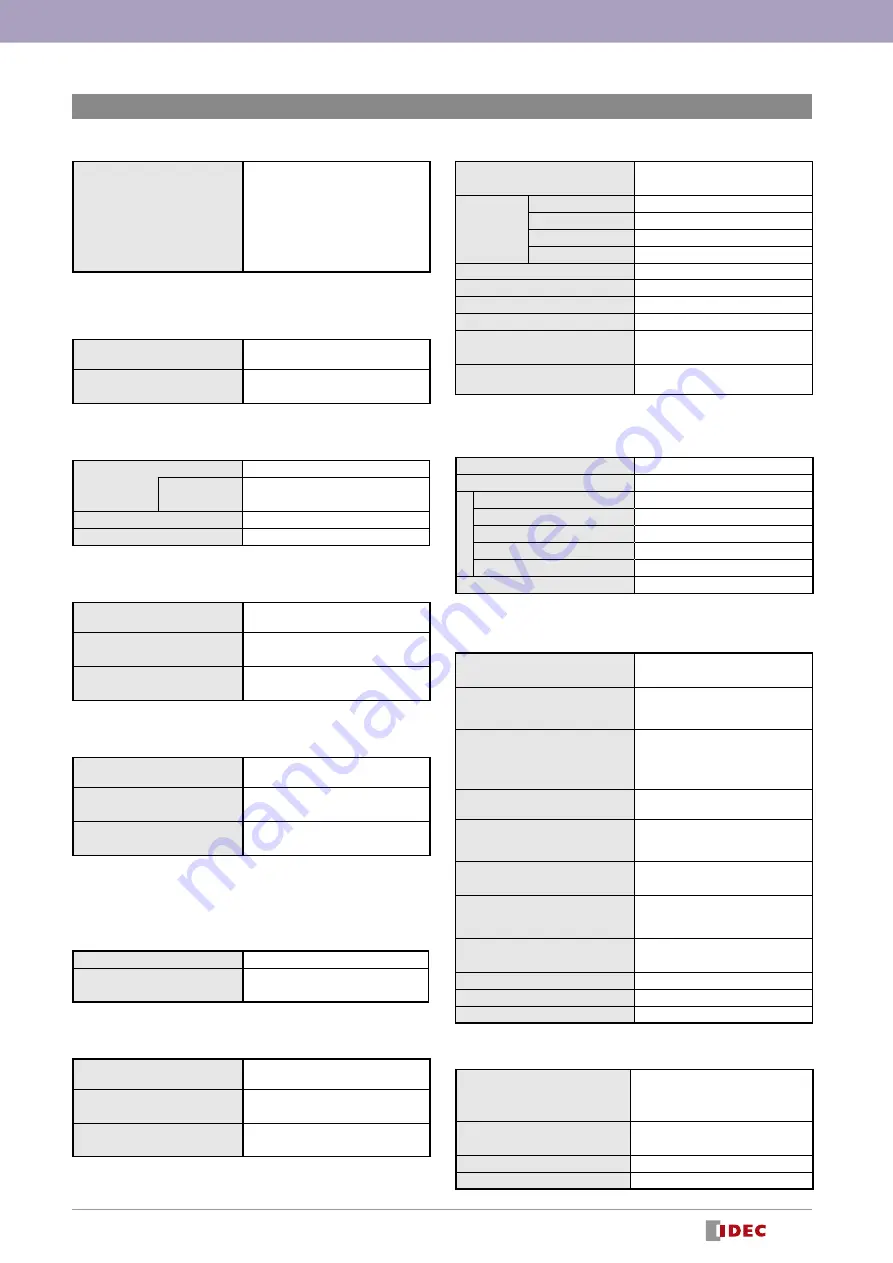
27
HR6S Safety Relay Module
Common Specifications
Environmental Characteristics for Operation
Maximum installation altitude above mean
sea level
2,000 m
Installation required in control cabinet/
enclosure with degree of protection
IP54
The device complies with class 3K5 and special class 3Z11 as per IEC
60721-3-3 (climatic conditions):
Ambient temperature
-25 to +55 °C (no freezing)
HR6S-DN
24 VAC: -25 to +50 °C (no freezing)
24V DC: -25 to +55 °C (no freezing)
Temperature variation rate
0.5 °C/min
Ambient humidity
5 to 95 % relative humidity (no condensation)
The device complies with class 3M4 as per IEC 60721-3-3 (mechanical
conditions):
Vibration, sinusoidal, displacement amplitude
2 to 9 Hz
3 mm
Vibration, sinusoidal, acceleration amplitude
9 to 200 Hz
10 m/s
2
Shock, shock pulse shape: half-sine,
peak acceleration
100 m/s
2
The device complies with the following vibration and shock values as
per IEC 60947-1:
Vibration, sinusoidal, displacement
amplitude 2 to 13 Hz
1 mm
Vibration, sinusoidal, acceleration amplitude
13.2 to 100 Hz
7 m/s
2
Shock, shock pulse shape: half-sine,
peak acceleration
150 m/s
2
Environmental Characteristics for Storage
The device complies with class 1K5 as per IEC 60721-3-1 (climatic
conditions):
Ambient temperature
-40 to 70 °C, no freezing
Ambient humidity
10 to 100 % relative humidity,
no condensation
The device complies with class 2M2 as per IEC 60721-3-2 (mechanical
conditions):
Vibration, sinusoidal,
displacement amplitude 2 to 9 Hz
1.5 mm
Vibration, sinusoidal,
acceleration amplitude 9 to 200 Hz
5 m/s
2
Shock, shock response spectrum type L,
peak acceleration
40 m/s
2
Wire Cross Sections, Stripping Lengths, and
Tightening Torques
Stripping length for Push-in terminals
12 mm
Stripping length for screw terminals
7 to 8 mm
Wire cross section
Single wire without wire ferrule (*1)
0.2 to 2.5 mm
2
(24 to 12 AWG)
Single wire with wire ferrule (*2)
0.25 to 2.5 mm
2
(24 to 12 AWG)
Two wires without wire ferrule (*1)
0.2 to 1.5 mm
2
(24 to 16 AWG)
Two wires with uninsulated wire ferrule
0.25 to 1 mm
2
(24 to 18 AWG)
Two wires with insulated wire ferrule (*2) 0.5 to 1.5 mm
2
(20 to 16 AWG)
Tightening torque for screw terminals
0.5 to 0.6 N m
*1: Stranded or solid
*2: See page
28
"Recommended ferrules" for ferrules.
Electrical Data
Supply voltage
24V AC -15 to 10 % 50 to 60 Hz
24V DC -20 to 20 %
Nominal input
power
HR6S-AB / EP / BAC
3.5 VA (24V AC), 1.5 W (24V DC)
HR6S-AF / AK
5 VA (24V AC), 2 W (24V DC)
HR6S-AT
6.5 VA (24V AC), 3 W (24V DC)
HR6S-DN
10.5 VA (24V AC), 4.5W (24V DC)
Overvoltage category
II
Pollution degree
2
Insulation voltage
300 V
Impulse withstand voltage
4 kV
Conducted and radiated emissions
as per IEC CISPR 11
Group 1 / Class B
Usage in environment as per
IEC/UL 60947-1
Environment B
Dynamization of Safety-Related Inputs and Start Input
(except HR6S-EP)
Test pulse duration (safety-related input
must be activated for longer than duration
of test pulse)
2 ms
Test pulse interval
500 ms
1000 ms (HR6S-DN)
Maximum delay of test pulse
40 ms
Test pulse phase shift (except HR6S-BAC)
At least 70 ms
Timing Data
Maximum response time to request at
safety-related input (except HR6S-BAC)
20 ms
Maximum response time after
power outage AC
140 ms (HR6S-EP)
150 ms (HR6S-BAC)
200 ms
Maximum response time after
power outage DC
80 ms (HR6S-BAC)
100 ms (HR6S-EP)
120 ms
140 ms (HR6S-DN / AT)
Recovery time after request at safety-related
input (except HR6S-BAC)
200 ms
Switch on delay after
power on and automatic start
1500 ms (HR6S-BAC)
2500 ms
3000 ms (HR6S-DN)
Delay after activation of safety-related input
or valid start condition
100 ms
Delay after power on and monitored start
1500 ms (HR6S-BAC)
2500 ms
3000 ms (HR6S-DN)
Minimum duration of start pulse
for monitored start
80 ms
Debounce time, standard
2.5 ms
Debounce time, with OSSD
4 ms
Signal interlock monitoring time
200 ms
Applicable Standards
Applicable Standards
IEC 61508:2010
IEC 62061:2015
ISO 13849-1:2015
IEC 60947-5-1:2016
IEC 60947-1:2007
UL60947-5-1
CAN/CSA C22.2 No. 60947-5-1
GB/T14048.5-2017