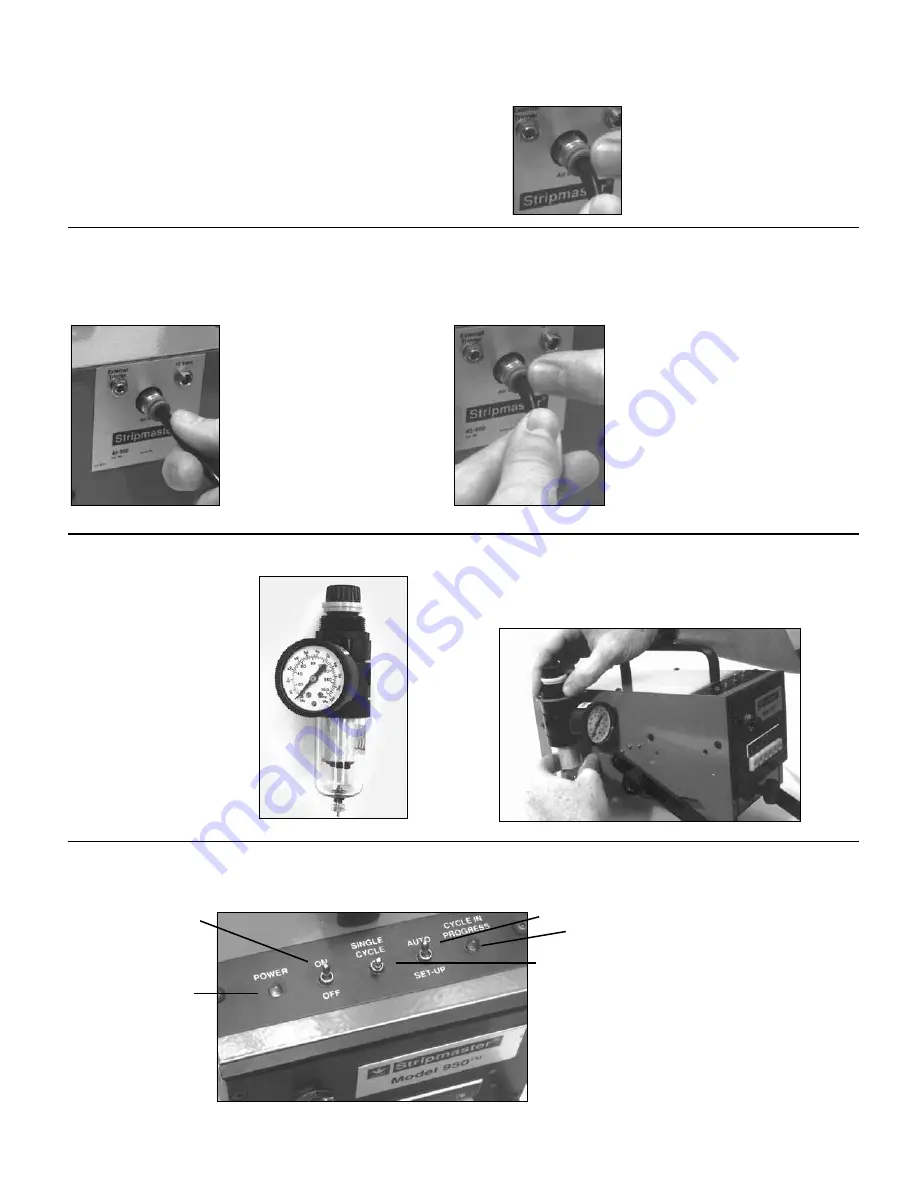
Operation
Hook-up Electrical
Connect 12-volt supply to power jack located at the rear of the unit.
Plug wall mount transformer in standard 115V outlet (use 45-951 and
proper cord set for 220V service).
Hook-up Air
Connect 1/4” coiled air hose to the air inlet fitting located at the rear of the unit. This is a reusable compression type fitting.
Connect the air hose by inserting hose firmly into the compression fitting.
Hook-up Air Regulator
1. Attach regulator mounting
bracket to either side of the
unit, using two button-head
socket screws provided.
(#45-906)
2. Remove the retaining nut from the regulator body,
locate the regulator in the mounting bracket and
replace the retaining nut securely.
Thermal Head Rotation Speed
4
Connect the air line to a clean, dry,
regulated air supply.
Air pressure must be regulated to a
maximum 65 PSI.
To disconnect, simply depress the
red ring and pull on the air hose.
CAUTION: Do not attempt to
connect or disconnect the air
hose with compressed air in
the line.
1. Turn the power switch
to the ON position.
Green power indicator
light will illuminate.
2. Place the AUTO/SET-UP switch to the AUTO position.
Red indicator light will illuminate.
3. Actuate single-cycle switch to cycle the unit. This will show
unit is ready for operation.
Note: CYCLE IN PROGRESS
light will illuminate
during stripping cycle.
Display
With proper air and electrical connections, the unit is now ready for operation.
Summary of Contents for Stripmaster 950
Page 1: ...45 950 45 954 45 950 1 Stripmaster Model 950 Model 954 Wire Stripper...
Page 14: ...Notes...
Page 15: ...Notes...