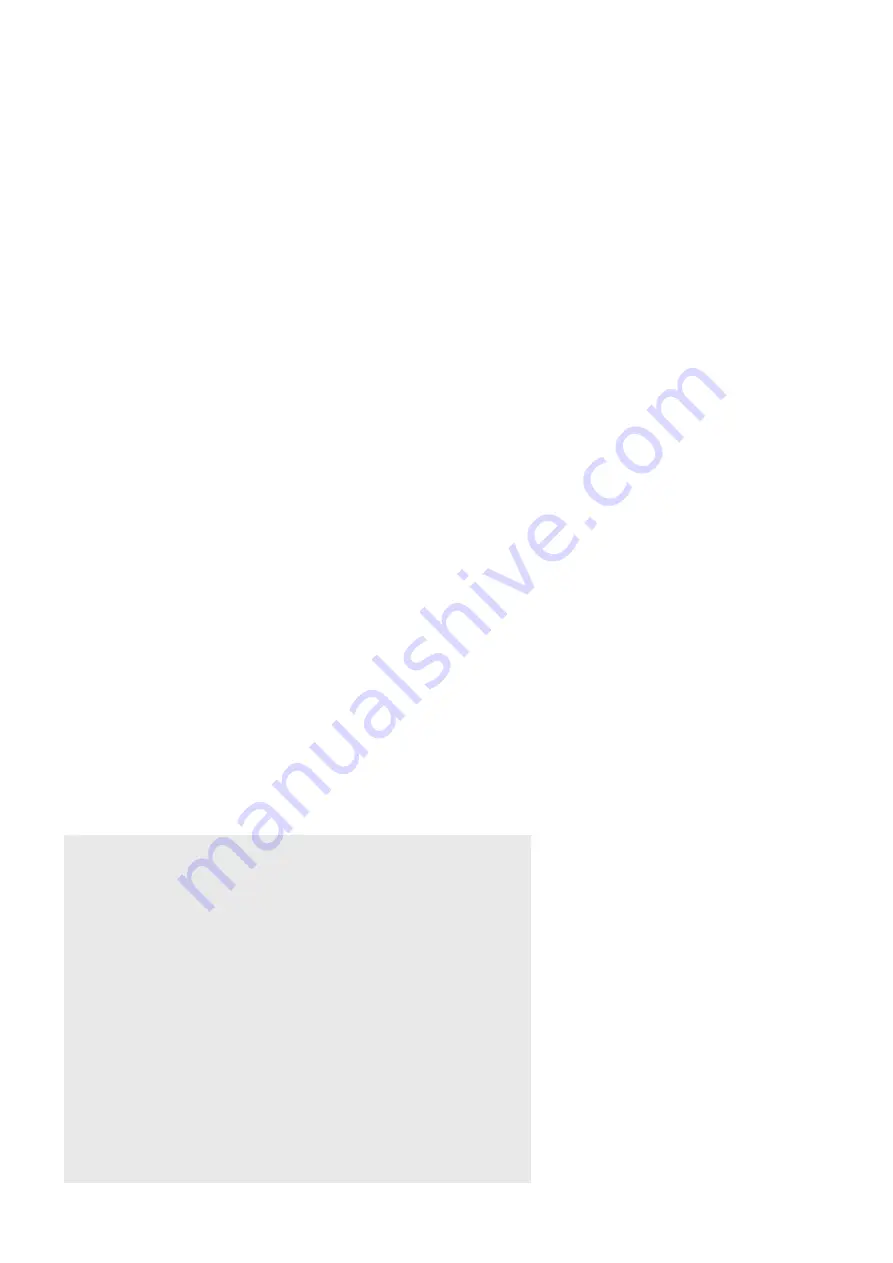
Page 18
All factory fitted components are tightened during manufacture, however all should
be checked before installation.
For the control thermostat set points of the immersion heaters for direct heating
of our cylinders, please refer to page 16 of this manual. The control thermostat for
indirect heat exchanger heat up of our cylinders are usually set at between 60°C - 65°C.
During commissioning the actual temperature that the cylinder reaches when the
thermostat(s) operate should be tested and adjusted so that it achieves a minimum
of 60°C. This temperature needs to be achieved on a regular basis.
Check the pressure on the air side of the expansion vessel = 3 bar. This must be done
when the water in the cylinder is free to expand in atmospheric pressure or the cylinder
and relevant pipe work is empty.
Check that the drain cock is closed, and open all the cold and hot water taps and other
terminal fittings. Allow the system to fill with water, and to run until there is no air left
in the system. Close the taps and inspect the system closely for leaks.
Manually open the Relief Valves one by one and check that water is discharged and
run freely through the tundish and out at the discharge point. The pipework should
accept full bore discharge without overflowing at the tundish, and the valve should
seat satisfactorily.
In line with good plumbing practice, use of excessive flux should be avoided. When
soldering above the cylinder, ensure flux/solder does not contaminate the cylinder
below, since this can cause corrosion. Flushing should be done performed as per BS
EN 806:4 2010 section 6.2.
Allow the cylinder to heat to normal working temperature, then thoroughly flush the
domestic hot and cold water pipework through each tap.
NOTE:
If this appliance is to be installed in other than a single domestic dwelling ie. in
an apartment block or student flats etc., the hot and cold water system will need to be
disinfected in accordance with BS EB 806:4 2010 section 6.3 and the Water Regulations.
Because the Ideal Pro appliance is stainless steel, the use of chlorine as the disinfection
agent can cause damage unless the appliance is adequately flushed and refilled with
the mains water immediately on completion of the disinfection procedure. Damage
caused through a failure to do this adequately will not be covered by the warranty.
For the reasons mentioned, we recommend the
use of a non chlorine based disinfectant such as
Fernox LP Sterox as manufactured by Cookson
Electronics when carrying out disinfection of
systems incorporating these appliances.
Remove the filter from the combination inlet
group clean and replace. Refill the system and
open all hot taps until there is no air in the pipe
work.
ENSURE CYLINDER IS DRAINED PRIOR
TO CHECKING OR REMOVING FILTER FROM
THE COMBINATION INLET GROUP
.
Allow the cylinder to heat to normal working
temperature with whatever heat source is to be
used, and check again for leaks. The pressure
relief valve or the P&T valve should not operate
during the heating cycle. If the P&T valve
operates before the pressure relief valve due to
high pressure, check that the inlet control group
is fitted correctly, and no valve is between the
inlet control group and the cylinder.
The boiler/heating systems should be filled and
commissioned in accordance with good practice
following the guidance in BS 7593:2006/the
boiler manufacturers instructions. This includes
adequately flushing the system to remove any
debris that may have been introduced during
installation/maintenance.
NOTE
At the time of commissioning, complete all
relevant sections of the Benchmark Checklist
located on the inside back pages of this
document.
This must be completed during commissioning
and left with the product to meet the Warranty
conditions offered by Ideal Boilers.
IMPORTANT - DRAIN DOWN PROCEDURE
1 Switch off both the boiler and the immersion heater
2 Open the nearest hot tap and run all hot water until cold, then close it
3 Close the incoming cold main at the stop tap
4
Hold open the pressure and temperature relief valve until water stops
discharging into the tundish and leave it open
5 Open the cold taps starting from the highest point and working down to
the lowest tap, leaving them open
6 When the cold taps have stopped draining, open the hot taps starting from
the highest and working down to the lowest tap
7 Open the drain cock and ensure the pressure and temperature relief valve
is held open until the cylinder is empty
INSTALLATION
COMMISSIONING