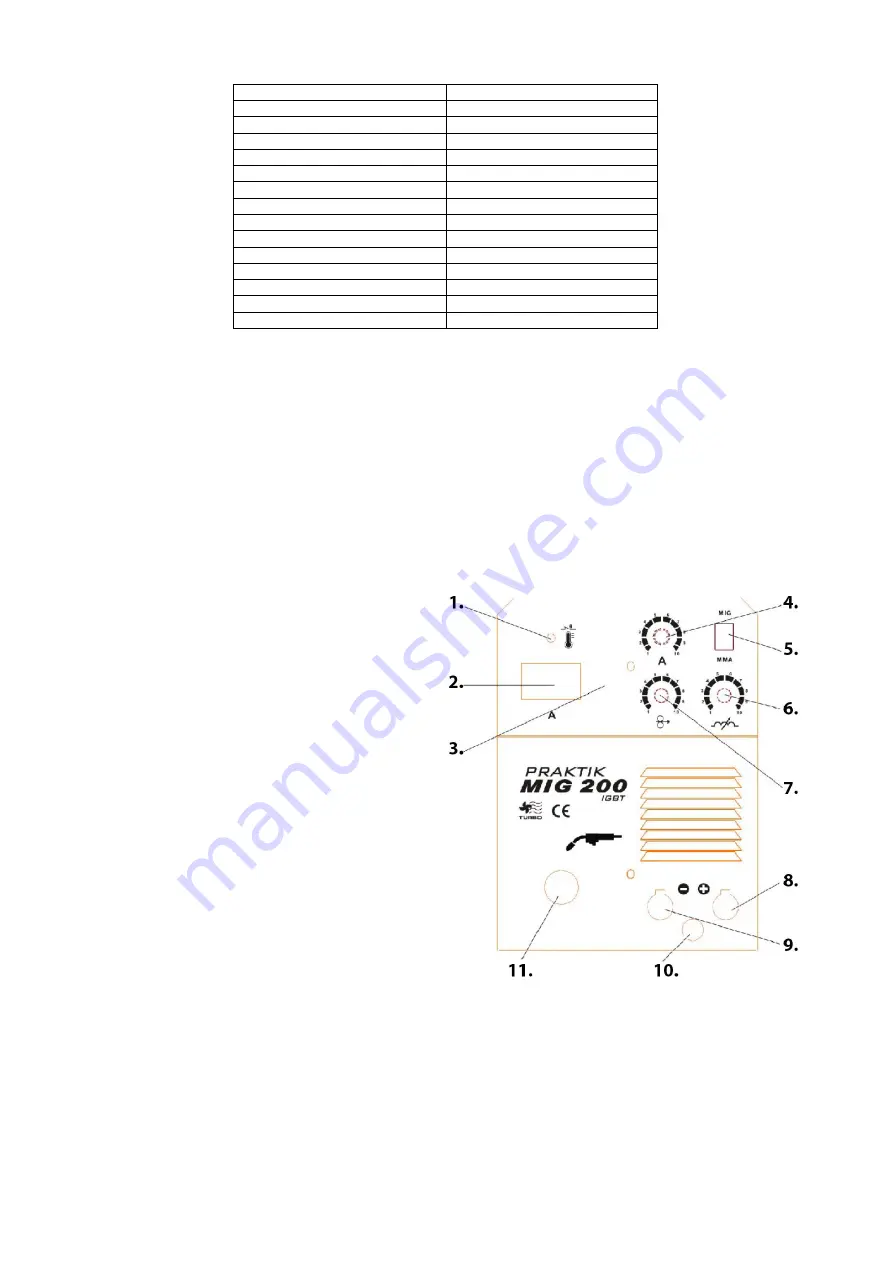
1. Technical specification
Power supply
AC 230V / 50Hz (1ph)
Welding processes
MIG, MAG, MMA
Technology
IGBT
Welding current MIG/MAG
30A - 200A
Welding current MMA
180A
Duty cycle
100% (130A) / 60% (180A)
Current regulation
Stepless (fluent)
No load voltage
56V
Power consumption
5.2 kW
Wire spool weight
5 kg
Compatible wire diameter
0.6 / 0.8 / mm
Minimum fuse
25A
Protection class
IP21S
Weight
15 kg
Wire feeder
2 rollers
2. Applications
Device is intended for light industry applications and works with material thickness not greater than 5-8
mm depending on conditions and type of material. Welding process that can be conducted using the
device is manual coated electrode welding (MMA) and semi-automatic arc welding with shield gas or
flux core wire (MIG/MAG)
The manufacturer is not liable for damage caused by improper use of the device.
3. Welding machine description
3.1 Front view
1. Overheat / malfunction indicator
2. Amperage display
3. Control panel
4. Amperage adjustment knob
5. MIG/MAG / MMA process selector
6. Inductance regulation knob
7. Wire feed speed adjustment knob
8. Positive polarization socket ( + )
9. Negative polarization socket ( - )
10. Polarization selector plug
11. MIG torch