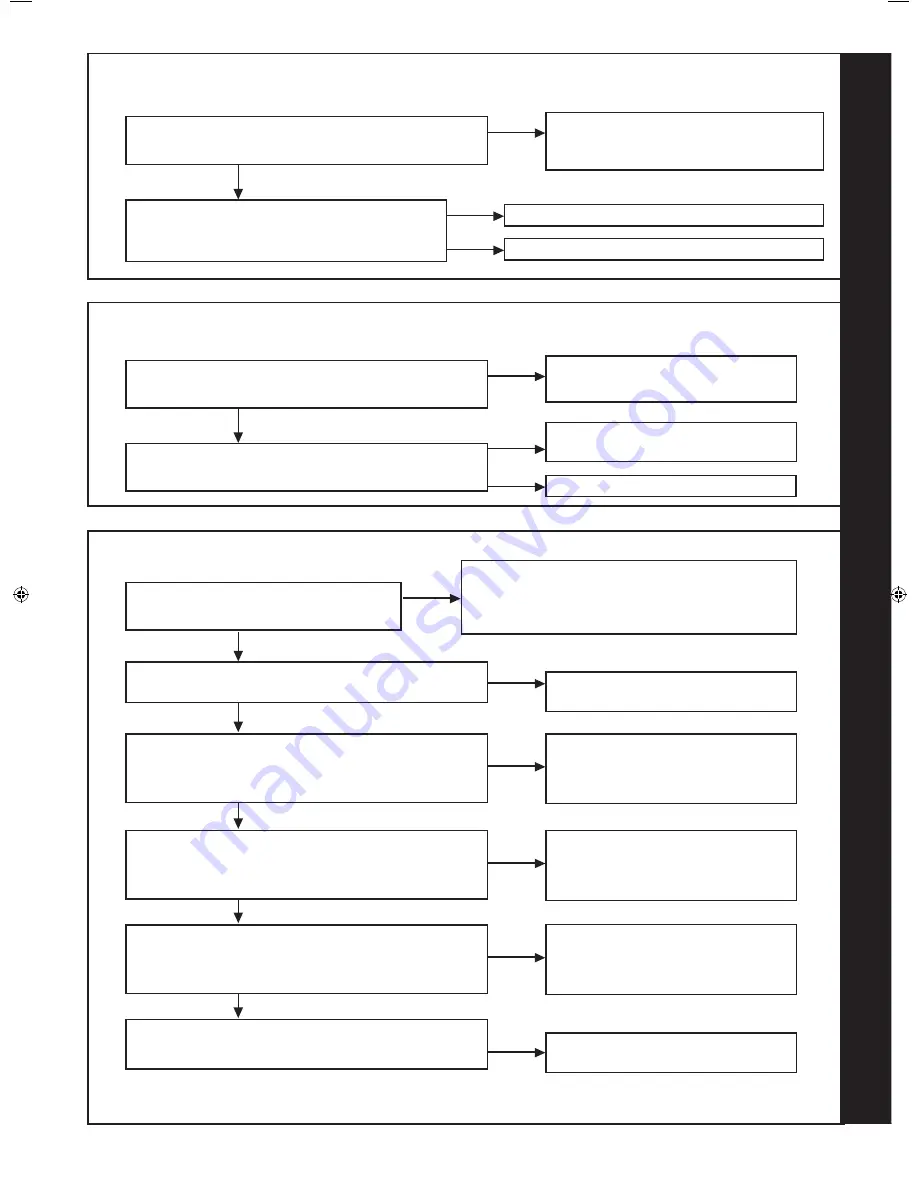
53
EVOMAX
-
Installation & Servicing
fAuLt fInDInG
f
A
u
L
t f
In
DI
n
G
f
A
u
L
t f
In
DI
n
G
f
A
u
L
t f
In
DI
n
G
f
A
u
L
t f
In
DI
n
G
f
A
u
L
t f
In
DI
n
G
f
A
u
L
t f
In
DI
n
G
76 FAlSE FlAME lOCKOUT / ERROR 20
Check routing and integrity of internal boiler
wiring is OK. Check condition of Flame
Sense Electrode and replace if deteriorated.
yes
Reset the boiler, does boiler work OK?
no
Replace Flame Detection Electrode
Replace Water Pressure Switch
Check routing and integrity of internal boiler wiring
yes
yes
no
Disconnect the electrical connection to the Flame
Sense Electrode. Is there continuity between the
Electrode and earth?
77 LoW WAtER PRESSuRE
Fill and vent the system and open all
Isolation Valves
no
Are the boiler and CH system filled with water and all
Isolation and Radiator Valves open?
yes
Ensure wiring has continuity and is
securely connected
no
Does the wiring from the Water Pressure Switch to the
PCB have continuity and is it securely connected?
78 fLAmE LoSS
Check the Detection Electrode and associated Harness
for continuity, visual condition and position (refer to
Frame 67). Check if the Condensate Pipe is blocked.
Check if the Flue is blocked. Replace as necessary
yes
If the boiler is Reset, does the boiler Ignite
for a short time and then Extinguish
no
Check Gas Supply and rectify fault
no
Is the Gas Pressure available at the boiler > 18mBar?
yes
Is the following voltage available at the Gas Valve?
(approximately 215Vdc for 30, 40, 60, 80 and 150kW)
(approximately 240Vac for 100 and 120kW) (*See note)
Check wiring from Gas Valve to PCB
and replace if necessary, otherwise
replace the main PCB
no
yes
Check Spark Generator and associated Harness for
continuity, visual condition and position (refer to Frame
58). Are these functioning correctly?
Replace Spark Generator and
Harness as necessary
no
yes
Check Ignition Electrode and associated Harness for
continuity, visual condition and position (refer to Frame
66). Are these functioning correctly?
Replace Ignition Electrode and
associated Harness as necessary
no
yes
Check Syphon and condensate drain pipework for
blockage and rectify if necessary. Boiler now working OK?
Replace Gas Valve
no
* Note: due to the wave form of the rectified voltage, the reading will vary depending on the type of meter used to measure the
value. In general terms a reading of greater than 150V indicates that the correct voltage is supplied to the gas valve
206210-3.indd 53
09/06/2011 13:35:00