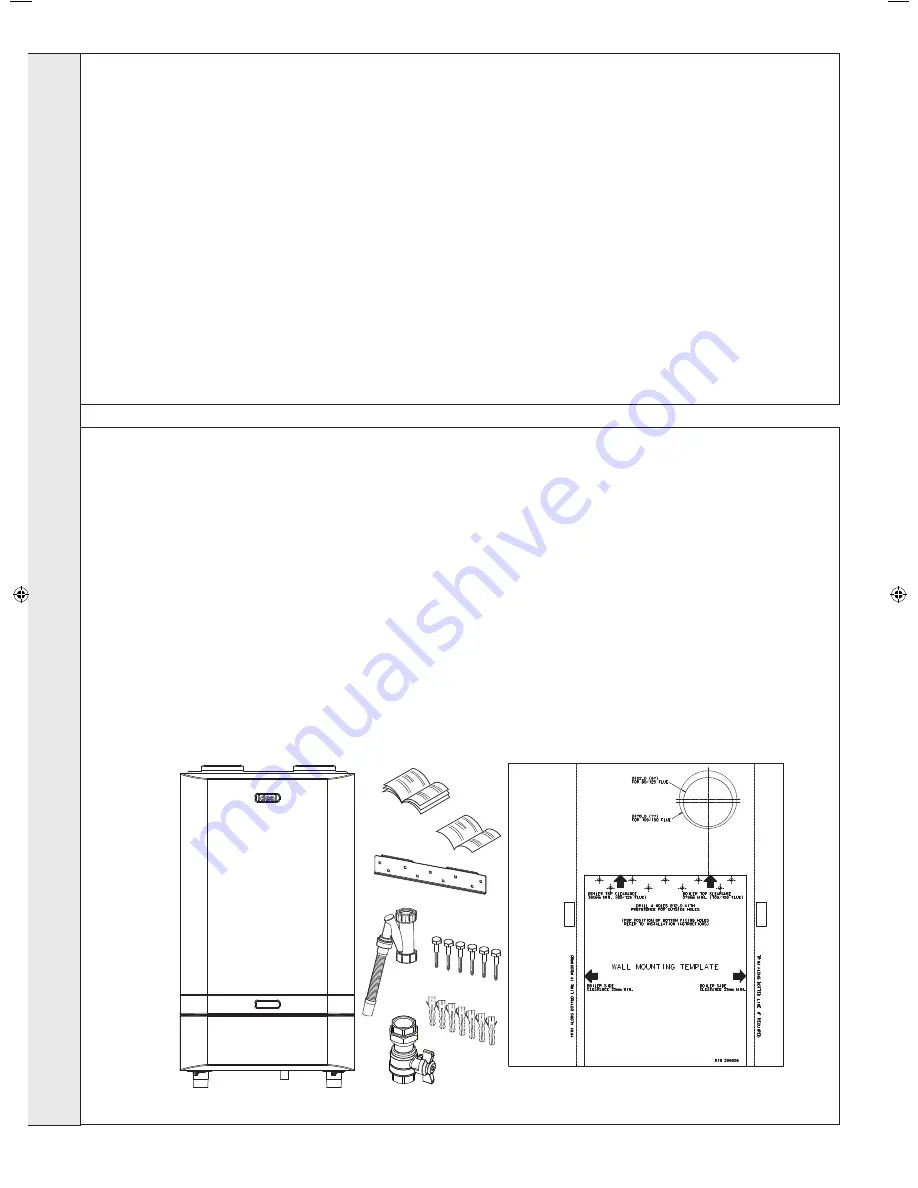
10
EVOMAX
-
Installation & Servicing
InStALLAtIon
6 unPACkInG
5 PACkAGInG REmoVAL
The boiler is supplied fully assembled in one pack. When
unpacking the boiler check the contents against the list
shown. Do not dispose of the packaging until all contents
are accounted for, as some parts are held within the
cardboard packing pieces.
•
The boiler should be laying on its back with the straps
removed.
•
Carefully read the installation instructions before proceeding.
•
Remove the outer packing sleeve.
•
Remove the protective cardboard wall mounting template
from the front of the boiler.
•
Remove the packing piece from the top of the boiler.
•
Check the contents against the list in Frame 6 ‘Unpacking’.
Note: some items are contained within the top packing
piece.
•
The boiler may now be stood on its base, with the
cardboard bottom packing piece still in place to protect the
connections. Due care should be taken when standing up
the boilers, with respect to their weights, see Table 2 on
page 2.
In
S
t
ALLA
t
Ion
B
A
C
D
F
E
G
H
J
Pack Contents
A
Fully assembled boiler
B
Installation & Servicing/User Instructions
C
Log Book
D
Wall mounting bracket
E
Wall mounting template
F
Condensate Trap
G
M10 x 70 Hex Head Coach Screws - 6 off
H
M10 Wall Plug - 6 off
J
Gas cock
206210-3.indd 10
09/06/2011 13:34:14