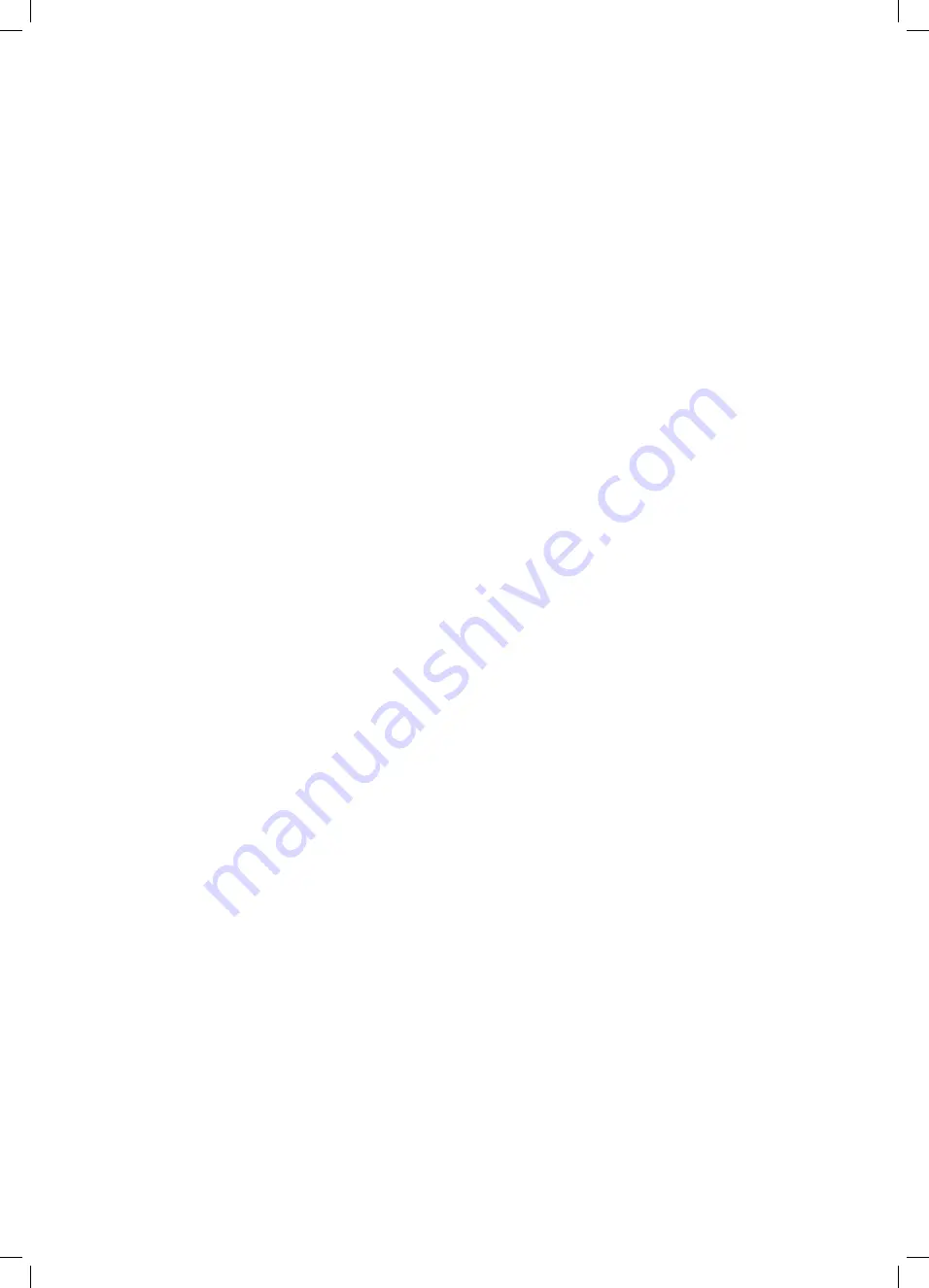
4
User’s
3. CONDENSATE DRAIN
This appliance is fitted with a siphonic condensate trap system
that reduces the risk of the appliance condensate from freezing.
However should the condensate pipe to this appliance freeze,
please follow these instructions:
a. If you do not feel competent to carry out the defrosting
instructions below please call your local Gas Safe Registered
installer for assistance.
b. If you do feel competent to carry out the following instructions
please do so with care when handling hot utensils. Do not attempt
to thaw pipework above ground level.
If this appliance develops a blockage in its condensate pipe, its
condensate will build up to a point where it will make a gurgling
noise prior to locking out an “
L 2
” fault code. If the appliance is
restarted it will make a gurgling noise prior to it locking out on a
failed ignition “
L 2
” code.
To unblock a frozen condensate pipe;
1. Follow the routing of the plastic pipe from its exit point on the
appliance, through its route to its termination point.
Locate the frozen blockage. It is likely that the pipe is frozen
at the most exposed point external to the building or where
there is some obstruction to flow. This could be at the open
end of the pipe, at a bend or elbow, or where there is a dip in
the pipe in which condensate can collect. The location of the
blockage should be identified as closely as possible before
taking further action.
2. Apply a hot water bottle, microwaveable heat pack or a warm
damp cloth to the frozen blockage area. Several applications
may have to be made before it fully defrosts. Warm water
can also be poured onto the pipe from a watering can or
similar. DO NOT use boiling water.
3. Caution when using warm water as this may freeze and
cause other localised hazards.
4.
Once the blockage is removed and the condensate can flow
freely, restart the appliance. (Refer to “To Start the boiler”)
5. If the appliance fails to ignite, call your Gas Safe Registered
engineer.
Preventative solutions
During cold weather, set the central heating temperature knob
(A) to maximum, (Must return to original setting once cold spell is
over).
Place the heating on continuous and turn the room thermostat
down to 15ºC overnight or when unoccupied. (Return to normal
after cold spell).
4. LOSS OF SYSTEM WATER PRESSURE
The gauge (G) indicates the central heating system pressure.
If the pressure is seen to fall below the original installation
pressure of 1-2 bar over a period of time then a water leak may
be indicated. In this event conduct the re-pressurising procedure
as follows:
Re-pressurise via the filling loop to 1 bar (if unsure contact
your installer). Turn off the tap on the filling loop and press the
“RESTART” button to restart the boiler.
If unable to do so or if the pressure continues to drop after filling
a Gas Safe Registered Engineer or in IE a Registered Gas
Installer (RGII) should be consulted.
NOTE. THE BOILER WILL NOT OPERATE IF PRESSURE
HAS REDUCED TO LESS THAN 0.3 BAR UNDER THIS
CONDITION.
5. GENERAL INFORMATION
BOILER PUMP
The boiler pump will operate briefly as a self-check once every 24
hours, regardless of system demand.
MINIMUM CLEARANCES
Clearance of 165mm (6
1
/
2
”) above, 100mm (4”) below, 2.5mm (
1
/
8
”)
at the sides and 450mm (17
3
/
4
”) at the front of the boiler casing
must be allowed for servicing.
Bottom Clearance
Bottom clearance after installation can be reduced to 5mm
This must be obtained with an easily removable panel to provide
the 100mm clearance required for servicing.
ESCAPE OF GAS
Should a gas leak or fault be suspected contact the National Gas
Emergency Service without delay.
Telephone 0800 111 999
.
Ensure that;
- All naked flames are extinguished
- Do not operate electrical switches
- Open all windows and doors
CLEANING
For normal cleaning simply dust with a dry cloth. To remove stubborn
marks and stains, wipe with a damp cloth and finish off with a dry cloth.
DO NOT use abrasive cleaning materials.
MAINTENANCE
The appliance should be serviced at least once a year by a Gas
Safe Registered Engineer or in IE a Registered Gas Installer
(RGII).
Summary of Contents for LOGIC SYSTEM S15IE
Page 4: ...4 Installation and Servicing...
Page 6: ...6 Installation and Servicing...
Page 60: ...60 Ideal Logic System Installation and Servicing...
Page 61: ...61 Installation and Servicing...
Page 68: ...68 NOTES Ideal Logic System Installation and Servicing...
Page 69: ...69 NOTES Ideal Logic System Installation and Servicing...
Page 70: ...70 NOTES Ideal Logic System Installation and Servicing...
Page 71: ...71 NOTES Ideal Logic System Installation and Servicing...
Page 80: ......